
Screening and analyzing: The two realms of acoustic micro imaging
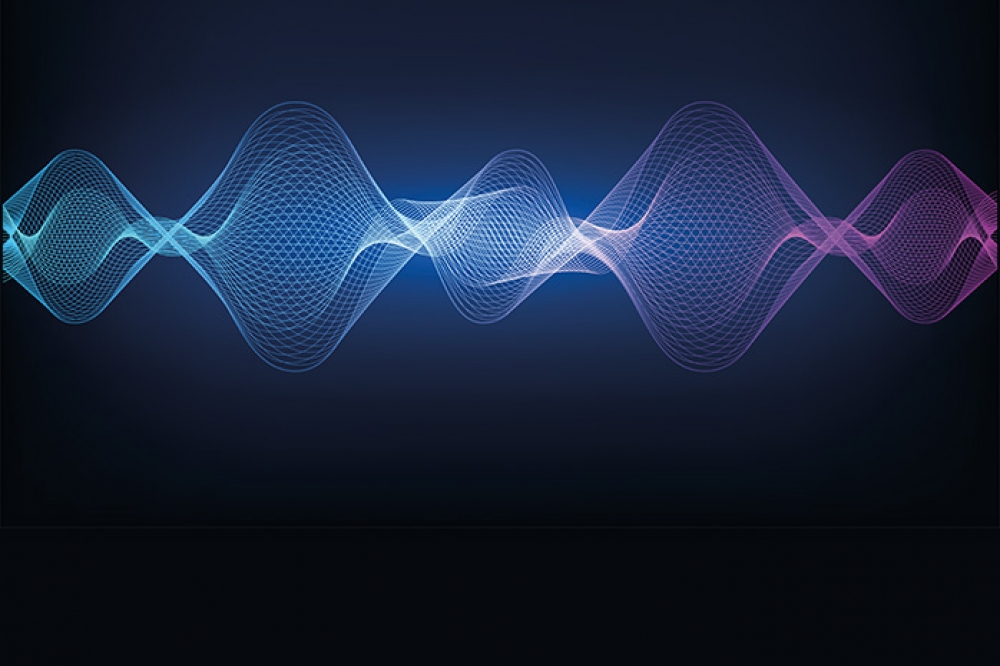
From the time they exist merely as part of an undiced wafer until they
are installed in the end product, electronic components undergo testing
and measuring by a variety of instruments to ensure a long, failure-free
life. One instrument is the Acoustic Micro Imaging (AMI) tool, which
uses the multiple types of data delivered by ultrasonic echoes to its
transducer to characterize internal material interfaces and material
properties within a given component.
By Tom Adams, consultant, Nordson
Test & Inspection
EVEN BEFORE production of a component begins, the Acoustic Micro Imaging tool’s ability to locate and image internal structural features in component prototypes permits evaluation of the package design’s integrity and robustness without activating or cutting open the component. The tool’s images can verify, for example, that a prototype’s die bond contains no unbonded areas, or that the encapsulant or underfill has no air-filled voids. The tool is also valuable in evaluating and viewing the results of thermal excursions in components after stress testing.
When a component in normal service has experienced a field failure, AMI data and images can help pinpoint the cause by non-destructive imaging before the component is physically cut open to permit visual inspection. The destructive process is known as Acoustically Guided Destructive Physical Analysis (AGDPA).
In the design and prototype applications mentioned above, the AMI tool operates in a laboratory, and usually analyzes small numbers of components at a time. But both the manufacturer and the user of the components perform large-scale screening.
The components are placed on trays and imaged at high speed by an automated AMI tool. The two imaging environments - low-volume analysis and high-volume screening - are described separately in this article.
Principles of Acoustic Micro Imaging
When the transducer of an Acoustic Micro Imaging tool fires a pulse of ultrasound into the surface of an electronics component, the pulse moves (#1 in Figure 1) through the water that couples the transducer to the component. When the pulse strikes the interface (#2) between the water and the surface of a component, a portion of the pulse’s energy is reflected (#3) back to the transducer, where its arrival time reports the distance from the transducer to the component’s surface.
Figure 1. Sequence of events when a pulse is launched into a component
The other portion of the pulse enters (#4) the first layer of material, which is typically an encapsulant. The smaller size of the pulse represents the partitioning of the energy at the interface. The ultrasound travelling through the encapsulant reaches the interface (#5) between the encapsulant and the silicon die. From this material interface a portion of the ultrasound will again be reflected (#6) back to the transducer. The rest of the ultrasound crosses (#7) the interface into the die.
Figure 2. IGBT imaged by Water Plume through the heat sink.
This echo returning from the interface, #6, arrives at the transducer and reports its travel time, and thus the depth of that interface. It also reports its amplitude, its ultrasonic frequency content, and the polarity (positive or negative) of the interface. These bits of data tell the user the depth of the interface and much about the two materials at the interface.
The transducer scans rapidly across the surface of the component and each second launches a pulse at each of tens of thousands of x-y locations, receiving the echoes from each location before launching the next pulse. Software will turn the returning echo from each location into one pixel in the acoustic image of the component. The pixel can be made to represent various aspects of the echo, for example, amplitude, frequency content, arrival time, etc.
The completed acoustic image may show the interface between the encapsulant and the silicon die as one color, and an interface between the encapsulant and copper as a different color.
Figure 3.Why ultrasound sees so much: the 14 acoustic imaging modes.
But the AMI tool will image the interface between a solid material and air (through which ultrasound at these frequencies will not travel) most brightly because the solid-to-air interface reflects nearly 100% of the arriving pulse. AMI systems easily find hidden internal defects because most performance-threatening defects contain air and thus present a solid-to-air interface to the arriving pulse. In black and white acoustic images, solid-to-air regions are typically imaged in bright white. In color images, red is often selected for these air gaps, which represent the voids, cracks, delaminations that often cause electrical failures in service.
In some components, the user’s interest may be only in a single depth within the component. In a given component type, if failures usually involve the die bond, a narrow electronic gate can be set that collects only those echoes that arrive at the transducer in the time slot matching the vertical extent of the die bond material.
Figure 4.Acoustic screening image of a tray of plastic-packaged ICs.
Laboratory Analysis
From the basic technology briefly described above, acoustic micro imaging tools have been developed to ensure that electronic components installed in products are free from internal structural anomalies that could result in electrical failures in service. One of these is SONOSCAN’s laboratory C-SAM® from Nordson Test & Inspection. It does not handle multiple trays of components; instead, it was designed to image anything from a single component to a tray of components, but it is equipped with all of the C-SAM imaging modes, which total about 14.
C-SAM analysis may be used for one or more components of the same type. They may be components that failed in service or during environmental testing, or they may be a few sample parts from a new shipment of a component that is in constant use. Or they may be an entirely new component that will be introduced soon. All of these may be imaged to find anomalies or material changes that could lead to defects. Multiple acoustic imaging modes are frequently used to ensure that even hard-to-detect anomalies are found and imaged.
Components may also be analyzed without imaging to determine whether the mold compound in a new shipment differs from the mold compound used in previous shipments. Typically a small number of components receive a single pulse at five locations. If the acoustic impedance and acoustic absorption values are close to the values from previous shipments, very likely the materials are identical.
An IGBT module may be imaged in the C-SAM reflection mode, as shown in Figure 1. In this mode echoes are received from all depths to assemble the acoustic image. This method may provide an overall view, but if the purpose is to examine closely all depths, the user may find that some depths are out of focus and cannot be accurately assessed.
A better choice may be the PolyGate mode. In this mode, the transducer divides a stream of incoming echoes from each x-y location into, say, 5 groups by their arrival time, and is thus able to create 5 images showing five separate depths.
Figure 2 was made to reveal possible internal defects in an IGBT module. Unencapsulated IGBT modules must be imaged through their bottom surface because topside imaging might leave residue that could lead to an electrical failure in this high-power component.
Bottom-surface scanning is done with a type of C-SAM tool having the transducer inverted. It pulses ultrasound into the IGBT that is above it. Ultrasound from the transducer reaches the heat sink at the bottom surface of the IGBT through a column of water called the water plume.
The gate is often set to collect echoes from a depth beginning just above the inside of the heat sink and ending just above the surface of the ceramic raft. If it is desired to image the die themselves, which are on the top side of the raft, the gate is extended to include them.
But in Figure 2 the depth of interest was the solder layer between the heat sink and the raft. Two facts were immediately evident:
⊕The thin ceramic raft is warped. The Time Difference mode was used for this image. The color of a pixel is determined by the feature’s distance from the transducer, or from a reference layer in the sample, but not its amplitude or some
other property. The red region is farthest from the transducer; the barely visible white region at the lower left corner may actually lack solder and be in contact with the heat sink.
⊕ The small variously shaped features within the solder are voids filled with air. The color reflected by a void is determined by the depth from which echoes are being returned. White voids are probably flat against the heat sink. There are green
and blue and pink voids, and some multi-colored voids that extend through more than one depth color.
The message in this image is quite direct: there are significant differences in solder thickness, which will lead to uneven distribution of heat from the die above. There are in addition air-filled voids that will reflect heat back to the die. This IGBT may not be suitable for use in production.
All of the imaging modes (Figure 3) developed for C-SAM may be used in the laboratory analysis of components. One mode is Q-BAM, which enables the user to select a vertical plane of interest and perform a nondestructive cross-section through the component along that line. The acoustic image shows details in the face of the component, as though the component has been sawn in two. Because the process its nondestructive, it can be repeated along as many other straight lines - of any orientation - as the user wishes. Q-BAM is sometimes followed by physical sectioning to compare the results. Using the nondestructive and destructive methods in sequence is known as Acoustically Guided Destructive Physical Analysis (AGDPA).
A quick look at some of the other modes:
Acoustic 3-D uses ultrasound to image non-vertical internal interfaces in colors that indicate each feature’s depth.
Acoustic Surface Flatness (ASF) uses color to reveal local departures from flatness in, for example, the surface of a BGA package or a 300mm wafer. Frequency Domain displays specific frequencies from the echoes to reveal internal features that are better revealed in this mode than by looking at the total echo amplitude. The echoes may contain a wide range of frequencies, say 75 to 125 MHz but the feature may only show up over a relatively brief frequency range - 93 MHz to 98 MHz, for example.
PolyGate lets the user create, during a single scan, multiple images, each of a specific vertical range. The result may be, for example, a sequence of 20 images each showing one of the 20 slices into which the returning echoes were divided.
THRU-Scan uses two transducers, one on top of the component and one beneath it. Each is coupled to the component surface by water. A C-shaped mount keeps both at the same x-y position at all times. The top transducer fires a pulse, but ignores echoes reaching it from all depths. A portion of the pulse passes through the back wall and is collected by the transducer below. No ultrasound passes through air gaps such as voids and delaminations, so these defects appear in the acoustic image as solidly black features.
STAR stands for “Simultaneous Transmission and Reflection Mode,” in which images are made from echoes returning (reflected) from internal interfaces and from energy that has passed through the component and has been detected by the receiving transducer underneath.
VRM means “Virtual Rescan Mode,” and permits re-imaging of a component that is no longer available to image because, for example, it may have been destroyed or lost. This could be important for establishing the root cause of a component failure that passed a screening test but failed anyway due to a previously unanticipated defect. The VRM mode records raw echo data from throughout the thickness of the sample and creates a matrix data file. If an FA engineer wants to rescreen the part acoustically using different modes of analysis the matrix file is rescreened instead of the missing component. In recent years some imaging modes that were once used only for analytical work have been adapted for use in screening. These modes are marked by an asterisk in Figure 3.
High-Throughput Screening
When the laboratory completes its detailed analysis of the chips that experienced similar failures, enough data has been collected to write the procedure for high-throughput acoustic screening of large numbers of a single component or component type.
The specific locations of known defects within the chip, and the most revealing parameters, are shared with all of the company’s locations where this chip is being used in assembly. Some defects are elusive. The details of the optimum imaging method will be shared by the laboratory with the firm’s assembly locations, which may be worldwide. This requires that each AMI tool be capable of achieving precisely the same image from the same component. Nordson Test & Inspection SONOSCAN makes this possible by supplying multiple matched tools that are in fact operational twins, triplets, etc., even if a component requires imaging using parameters that differ substantially from the usual menu. AMI tools with different operators speaking different languages and on different continents will produce precisely the same image from a single component.
Screening can take place both before and after components are mounted on a board. The purpose of screening is to identify and remove those components that possess internal features that the laboratory has identified as anomalies that could generate field failures.
The result is a demanding environment. The components, which are already in trays used in the manufacturing process, are scanned by Nordson Test & Inspection SONOSCAN FastLine® high-throughput AMI tools. If there is more than one depth of interest, or if anomalies are suspected that may not all be imageable by the same means, then echoes from multiple gates are collected during the same scan. The screening tools must be highly automated in order to characterize thousands of components quickly.
The transducers must be able to focus automatically. They must be able to image in a dozen or more modes and must be able to use precisely the same parameters - imaging mode, frequency, amplitude, and depth range. They must be able to capture returning echoes within the same sub-millionths-of-a-second time period. And they must avoid permitting any residue or contamination to reach components being imaged. Even the analysis of the images to select which components must be scrapped is automated.
The acoustic frequency used is designed to give maximum resolution at the desired depths within the component. The frequency of ultrasound being pulsed into the components may range from 10 MHz (low resolution, but deep penetration) to 300 MHz (high resolution, but less penetration).
Because the laboratory’s analytical work has identified the most likely locations where a given defect may occur, scanning may be simplified by using only those echoes arriving at the transducer within a specific time span. The time span defines the “gate,” the vertical depth within which defects are most frequent. For example, if the most frequent depth for defects is at the interface between the die face and the encapsulant, it may not be judged necessary to process echoes from other depths in this component.
Figure 4 is the AMI 30 MHz reflection mode image of a tray filled with components. They were screened because the laboratory had found that similar defects in components caused failures during testing. The images were made with the SONOSCAN FastLine tool from Nordson Test & Inspection.
This image is one of several made during a single scan of the tray. Several gates were set, and echoes originating between two gates would be used to make a single image for that very thin horizontal slice of the component. This image was made from echoes originating at the interface between the mold compound and the top of the silicon die. This image’s gate was set from just above the mold compound to die interface to just below that interface. Red was selected as the color to identify pixels at a solid-to-air interface.
The red defects are air-filled delaminations - flat air bubbles. In this location thermal excursions during use may cause them to move upward and downward, actions which may result in breaking wires attached to the die or in cracking the die itself. The result in either case is electrical failure.
Laboratory analysis can use any of the 14 imaging modes. There has been a gradual trend over the years of modes from the laboratory being modified for use in screening environments - PolyGate is one example. But some imaging modes are simply too time-consuming and data intensive for high-speed screening. Examples are Q-BAM nondestructive cross-sectioning and three-dimensional acoustic imaging.
Together, the laboratory C-SAM and the production floor FastLine find risky components before they can blossom into field failures. The key is the variety of imaging modes that can report many different data forms from diverse types of internal structural anomalies. The benefactors are end users whose electronic devices, vehicles, computers, telephones, appliances and tools fail to break down.