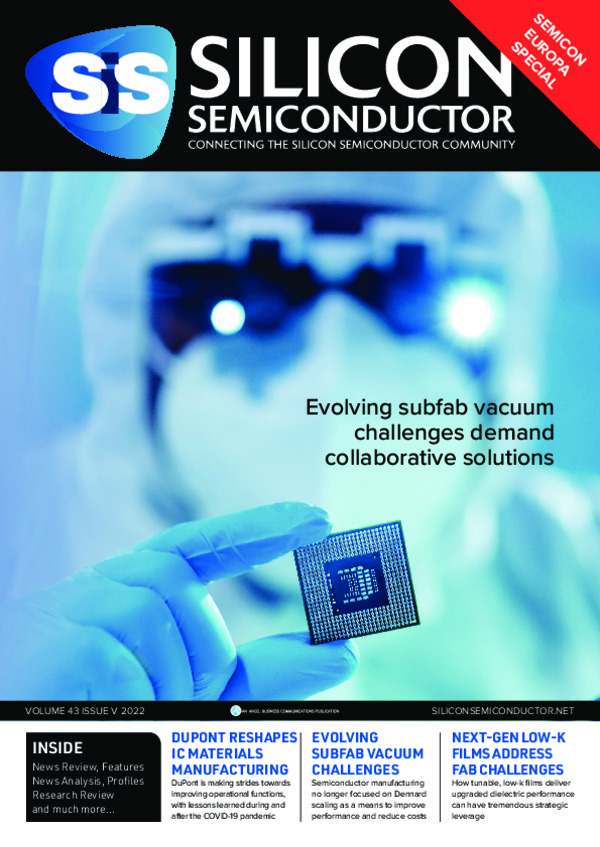
Critical Manufacturing redefines semiconductor MES
Semiconductor manufacture is highly complex. Production involves a lengthy global supply chain and hundreds of steps at nanometre scale. Manufacturing execution system (MES) software is typically used to enhance yields, control processes and help ensure quality. Silicon Semiconductor Technical Editor Mark Andrews spoke with Critical Manufacturing’s Sales Manager, Tom Bednarz, about ways his company’s MES differs from the rest.
Silicon Semiconductor Technical Editor Mark Andrews spoke with Critical Manufacturing ahead of SEMICON Europa to learn what sets their MES apart from the rest
Semiconductor fabs operate around the clock in strictly regulated clean room environments with tightly controlled processes of extreme precision and accuracy. A single manufactured product may consist of multiple interconnected layers and require hundreds of manufacturing process steps using sophisticated tools and techniques. To handle rising demand, greater product complexity, an ever-growing process mix, and new application requirements, semiconductor makers must increase their pace of both learning and new product innovation to succeed in global markets. According to Tom Bednarz, Critical Manufacturing Sales Manager, MES must expand beyond work-in-process (WIP) and track and trace functionality to become the data platform for production innovation, change, and efficiency.
MA: Can you please explain how Critical Manufacturing’s change management and versioning capabilities differ from other MES programmes that also offer change management and version control applications?
TB: Critical Manufacturing’s MES comes with a built-in versioning and change management solution. All important master data objects are versioned. A change to the process can include one or multiple objects like recipes and parameters, BOMs, data collections, SPC charts and so on. The new versions of these objects can be created by super-users in the organization and then sent for approval. The approval process can be designed by our customers to reflect their business rules and as such it can support change management instruments such as a process change review board (PCRB), which some of our customers already have in place. Approvers in various roles including quality, planning, etc. can approve or reject the changes, or send them back for rework.
Critical Manufacturing supports the use of versions and revisions to manage the complexity of WIP-affecting changes. Our process enables full control of how changes will impact your running lots in the fab. This feature allows our customers to introduce changes faster and with less risk than other MES solutions.
MA: Can CM please offer an overview of how its experiments management system works & how this facilitates experimentation within an active production environment?
TB: Experiments are important to all our customers. New products and processes are a major driver, but there is always the need for continuous improvements, qualification of new consumables, durables or process tools/machine, not to mention new characterizations of process windows and so on. Experiments are run pretty much in each fab with or without the support of the MES, but the Critical Manufacturing system helps researchers and production management engineers alike to control and record all pertinent actions and results obtained from experimental runs. At present, many manufacturers are using manual processes to control their experiments. They usually put the lots on hold at the relevant steps which are then sitting and waiting for an engineer to attend the processing of such experiments.
The concept of a fully integrated experiment management is completely the opposite. You want the material to run through the line with the same speed and degree of automation as the standard lots. Critical Manufacturing’s system supports you in defining and planning your experiment. It allows you to define split groups of individual wafers, the slots of each experimental lot and the changes that these different groups shall see in the process compared to POR lots.
Once you assign selected lots to the experiment, the system will take care of executing your experiment as planned. It will perform splits and merges, future holds, and releases as well as changes in recipes, equipment, measurement, and data collection plans and so on. Since it’s fully integrated, it can also consider the impact on sampling rules, SPC charts or non-conformance management.
When the lot reaches an experiment step, the processing can either be fully automated or the operator can take care of processing the lot according to whatever the requirements are within an individual experiment. The system will guide the operator through the necessary actions in case a split or some special action needs to be performed. But essentially, the operator does not need to have any specific knowledge of the experiment or wait for additional persons to perform his job. The automation option can be a huge accelerator for experimentation and a tool for achieving consistency that manually interjected parameters can’t achieve.
In the end, the MES will track and record all actions performed and evaluation of the experiment will be possible based on the data in the system. Our customers value these capabilities a lot, especially since there is no need for manual instructions, excel sheets with split plans and tedious data gathering from various sources that are typically found in manual or ‘ad hoc’ experimental environments.
Critical Manufacturing MES business data
MA: Can Critical Manufacturing please define what it means as ‘send-ahead’ wafers and what the utility of the CM MES offers in this area that competing systems do not?
TB: A send-ahead wafer is a common scenario in a front-end process. Usually, when reaching a certain step in the process flow, one wafer will be split from the lot and move into one or several steps individually. The result of processing the individual wafer will then be assessed and a decision will be made regarding the processing of the remaining wafer lot. This decision can be either to apply the same process setup to the rest of the lot, adjust the process parameters based on the process results achieved, or to run another send-ahead with a changed setup.
This scenario is typically used where a process depends on certain conditions such as a chemical concentration influencing etch rates or some exposure conditions impacting the quality of the patterning results. These conditions can come from within the process step or from previous process results such as a thickness or uniformity. What they have in common is that it is hard to exactly determine the optimal settings without running a trial wafer and validating the setup.
This use case is present in pretty much any front-end fab, but very often it cannot be handled within the MES. In contrast, Critical Manufacturing’s MES comes with built-in send-ahead support. This means that a process engineer can define the process flow that considers the steps where send-ahead wafers will be required. The system allows defining the starting and finishing steps of each case, the selection of wafers and the decision to be taken at the end. With these definitions in the MES, execution can be fully automated or can take place with operator support.
If you do this outside of MES, which many fabs do,you will rely on experienced operators, local documentation and have no control over what happens.
Similar to the experiment use case, the benefits of native support in the MES are speed and ease of use, as well as the creation of a fully documented history. MES-based control also enables very important qualities such as integration with all the other functional modules like recipe and parameter management, WIP management, experiments, and process control.
MES Experiment design table
MA: Can Critical Manufacturing please explain the major approaches to managing ever-changing process ‘recipes’ and how the CM version is superior?
TB: Recipe Management is an essential functionality in semiconductor manufacturing and should be a core feature of the MES. Thanks to the standardization efforts of SEMI, it’s possible today to provide a comprehensive recipe solution within the MES to allow users to do everything from creation and storing, to controlling changes, and comparing recipes. With automation capabilities of modern equipment, recipes can be automatically selected, downloaded, and parameterized.
To manage variations and complexity, Critical Manufacturing uses a concept called flexible context resolution. It means that based on predefined precedence rules, the system decides at runtime which recipe to use for a process step based on several different criteria. These criteria can be as generic as the product family and the equipment model and even result in a default recipe. On the other hand, there can be more specific criteria such as a process chamber, a consumable used (or not used) or even a specific lot or split group within an experiment.
On the dynamic side, the resolution can consider input from a previous process, properties of a consumables batch or characteristics of the current process such as an etch rate or a rework counter.
Using these capabilities, our customers can manage their recipes supported by change management functionality, including approval processes and version control. But they can also create algorithms to dynamically adjust recipes and parameters resulting in fewer recipes needed and fewer changes required.
MA: Can you please define how Critical Manufacturing defines run-to-run control and explain briefly how this capability benefits production management?
TB: Run-to-Run control is a method that applies adjustments to process recipes or parameters between each time a lot or wafer is processed, or between process runs. The adjustments will be calculated by an algorithm known as the ‘controller’ based on various input values coming from previous runs, current process conditions and properties of the input material which could be results of previous process steps. The objective is to minimize process variability coming from drifts, shifts and other influences.
Some examples are calculation of etch times or transport speed depending on chemical conditions in an etching line, polish time or pressure settings in a CMP process depending on the polish rate which can vary over the lifetime of a pad or depend on the layer stack on the wafer. Also, CD and overlay optimizations in lithography are typical applications.
The development of a controller usually requires an analytical process of gathering the right amount of data from various sources, creating a model how certain input values will result in predictable process output and then running experiments to prove the algorithm and mature it for productive use.
The MES can support controller development by providing all the necessary data for the modelling process. It can also support the process of running experiments through the line from the planning to the evaluation if it offers an experiment management functionality.
When it comes to applying Run-to-Run control at runtime in production, the Critical Manufacturing MES will provide the input data, execute the algorithm, and dynamically calculate the recipe parameters for the run. This can happen fully automatically and will ensure optimized and stable processes.
Run-to-Run control not only benefits the production manager by avoiding excursions, rework and scrap while stabilizing processes, it also offers better reproducibility and predictability.
Critical Manufacturing will highlight its advanced semiconductor MES capabilities at SEMICON Europa, collocated with Electronika, Nov 15–18, 2022, at Messe Munchen, Germany. Designed specifically to manage complex processes within a semiconductor manufacturing environment, the Critical Manufacturing MES is an advanced solution that fully integrates the shop floor, gives complete visibility of operations, promotes manufacturing agility and innovation while enabling continuous process improvement.
Critical Manufacturing experts will be at stand C1736 in Hall C1. To schedule a live demonstration of the key capabilities of the Critical Manufacturing MES, please visit: https://www.criticalmanufacturing.com/campaign/semicon-europa-2022