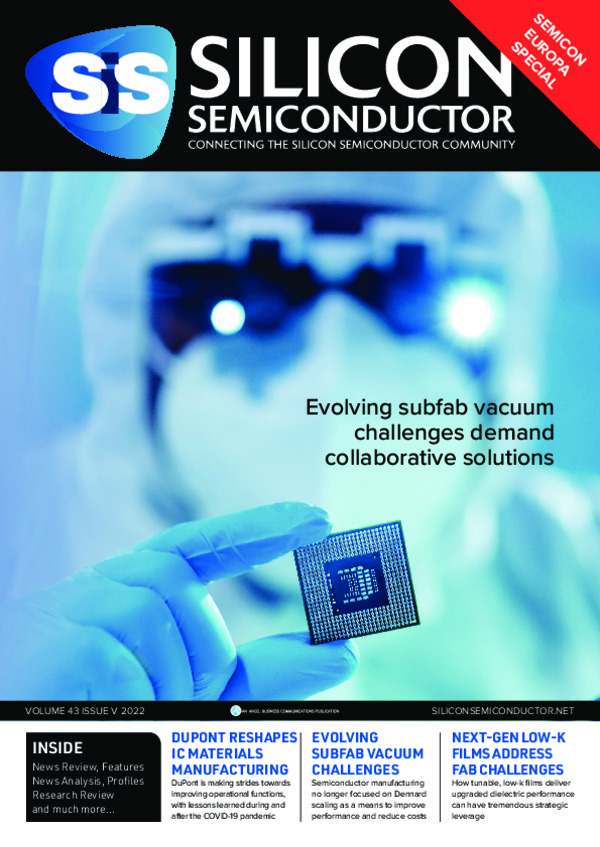
Evolving subfab vacuum challenges demand collaborative solutions
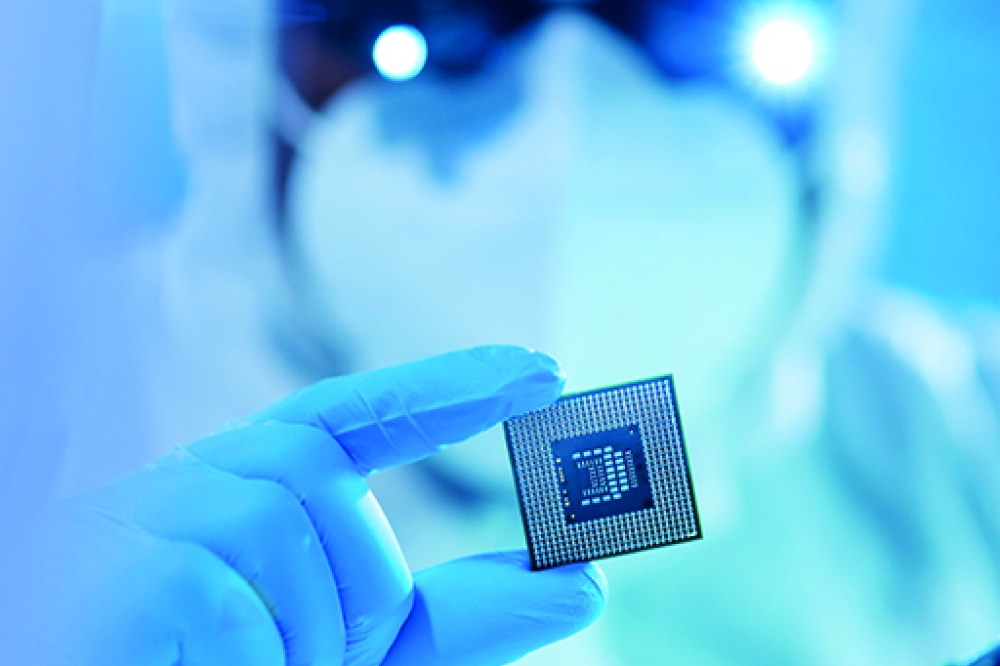
Semiconductor manufacturing is no longer focused on Dennard scaling as a principal means to improve performance and reduce costs. Coordinated, lock-step efforts have given way to a sometimes-bewildering collection of new materials and technologies, often adding complexity in the form of new and different process tools, techniques and chemistries. This evolving IC production environment means manufacturers and suppliers need to collaborate in developing next-generation solutions that positively impact climate change, reduce costs and improve device performance.
By Matt Halsey, Edwards Vacuum
Semiconductor manufacturing technologies continue to diversify at all levels, from device architecture to multi-chip and chiplet integration schemes, through an expanding variety of advanced packaging technologies. Long gone are the days when device manufacturers advanced lock step down a road map focused almost exclusively on shrinking device sizes. Gone too is the luxury of developing a new process tool to meet a widely acknowledged, well defined set of requirements, with the assumption that there would be time to fine tune the design based on customer feedback after the product introduction.
In an environment with multiplying pathways to technical and commercial success, close collaboration between device manufacturers and equipment suppliers will acquire increasing importance as both seek to hasten development cycles, reduce time-to-market for new products, and target new products more precisely on key applications.
These same pressures apply in the subfab as well, where exist the essential systems that support the process tools above. Most semiconductor manufacturing processes require a vacuum; consequently, loss of that vacuum will take down a production line just as surely as a failure in the tool itself. Integrating new processes and materials into the production line must include careful consideration of the impacts on the vacuum systems tasked with removing excess gases and byproducts from the tools. Failure to do so will inevitably lead to more frequent maintenance, shorter service lifetimes and reduced reliability. In the worst case, it will result in unplanned down time with all its associated costs.
In addition to changes in processes and materials, vacuum challenges in the subfab include shrinking space, increasing energy costs, and growing concern about the sustainability of the manufacturing process. Many of the design choices will require carefully balanced trade-offs among conflicting requirements.
The Process
The ever-increasing capital cost of new manufacturing capacity at advanced process nodes exerts relentless pressure on manufacturers to increase throughput in order to amortize higher fixed costs over a larger product output. For vacuum systems, higher throughput usually means higher flow rates and larger pumps.
Changes in process chemistry include the use of more aggressive reactions with harsher chemicals which require more resilient pumps. Pumps must incorporate materials and coatings that can withstand process gases and their by-products, as well as the corrosive chemicals used to clean process chambers.
Higher (and sometimes lower) temperatures for critical processes like atomic layer deposition and chemical vapor deposition require pumps that can handle the greater temperature range. Tolerances for rapidly spinning rotors are very tight and thermal expansion must be carefully managed. Materials used for seals at more conventional temperatures may not withstand higher temperatures. Often the temperature profile of the pump and associated piping must be carefully managed to avoid deposition of condensable materials.
Figure 1 shows how cluster tools might be reconfigured from the traditional radial layout to linear. The tools (and the pumps below) occupy less space, but the required pumping capacity remains the same.
Subfab space
Demands for higher throughput are leading manufacturers to put more smaller tools in less space in the fab. Following the convention that supporting systems must fit within the footprint of the process tool as projected down to the subfab, pumps and abatement must also fit in less space while handling increased flows. This can be especially challenging for pumps where the physical size of the pump has a direct relationship to its pumping capacity. Fab operators are currently looking for a 20-30% reduction in pump footprint, just to keep up with decreasing tool size. Stacking pumps in the subfab offers one solution, but there are limits related to safety and maintenance concerns.
Utility costs
Semiconductor manufacturing is energy intensive. The energy invested in a completed device can be 5.4 MJ (1.5 kWh) or more per square centimeter. Power is expensive and prices are increasing. Manufacturers are demanding more energy efficient systems, often for the simple reason that it reduces operating costs, with a sustainability aspect secondary to this.
Unfortunately, the desire for reduced energy consumption often conflicts with the need for increased pumping speed and pump temperature. Vacuum pumps do mechanical work, and, in the simplest analysis, more work takes more energy. The problem is exacerbated in harsh applications where additional power may be required to overcome resistance caused by material deposition within the pump or heavy particle loads in the process exhaust stream.
Implementation of idle mode technologies that reduce power consumption when the supported tool is not operating promise some relief; but again, harsh processes pose a specific challenge to vacuum systems where a halted pump may be difficult to restart reliably in the presence of deposition buildup and high particle loads.
The urgency of power concerns varies somewhat by region; power availability in Taiwan is severely restricted and energy efficiency is a high priority. In Europe, energy prices have soared recently, largely as a result of the war in Ukraine and the heavy reliance on natural gas as an energy source across the EU. Geopolitical tensions seem unlikely to diminish in the near term, adding additional pressure to demands for energy efficiency.
Sustainability
There is now a complete consensus within the scientific community that our environment is warming and that the warming is the result of human activity. Every industry, including semiconductor manufacturing, has an obligation to do everything possible to reduce the carbon emissions that are the primary cause of warming. Relative to some industries, semiconductor manufacturing is not a large direct emitter of greenhouse gases (GHG). But manufacturing ICs does consume vast amounts of energy, most of which currently comes from burning fossil fuels. The solution lies ultimately in the conversion of power generation to renewable sources, and as an industry with significant financial and political influence, we must advocate for that conversion.
However, the greatest potential for short-term reductions in GHG emissions lies in reducing our power consumption by improving our energy efficiency and minimizing the use of supporting utilities, all of which cost energy to produce.
Some of the trends we have mentioned work against reducing power consumption, such as the need for higher flow rates and temperatures. Fortunately, the most powerful influence – the always present drive to reduce costs – aligns directly with the environmental imperative to reduce power consumption. This powerful combination has driven broad commitment across the industry to embrace principles of environmental stewardship. As part of the Atlas Copco Group, Edwards Vacuum has signed on to the Science Based Target Initiative, which commits participants to take all possible actions to limit global warming to less than 2°C. SEMI, our industry association, has updated its guidance (S23) to semiconductor manufacturers and equipment manufacturers to provide a basis for measuring energy consumption that will facilitate comparisons and encourage greater efficiency.
Figure 2. In this example from an ISMI study, more than half of the power consumed by a CVD process tool is attributed to vacuum generation.
Vacuum requirements vary greatly from process to process. Some, like plating and chemical mechanical polishing, require no vacuum. Some, like EUV lithography and atomic layer deposition, require constant turnovers of chamber gases under vacuum conditions. Figure 2 shows an example taken from an ISMI Fab and Equipment Energy Study showing the power consumption attributed to a chemical vapor deposition (CVD) tool.
Most estimates allot something like 40% of overall fab power consumption to process equipment. In the case of CVD, over half of that power goes to creating and maintaining vacuum - 41% for chamber vacuum provided by dry pumps in the subfab and another 10% for the load lock pump on the tool itself. This is consistent with estimates that put power consumption for process vacuum at 20% of overall energy usage in semiconductor manufacturing.
Clearly, improvements in the energy efficiency of vacuum systems can make a significant contribution to energy savings. Demands to take verifiable action to support sustainability goals is mounting throughout the supply chain and in capital markets. Downstream companies, especially consumer-facing companies, are under mounting pressure from customers to enhance their sustainability.
This ripples up the supply chain where subfab equipment can be a critical enabler. In an internal study at Edwards, we found that 97% of all GHG emissions (carbon dioxide equivalent) generated over the lifetime of a vacuum pump, including all inputs (power, water, cooling, nitrogen, etc.) from initial manufacture to final disposal, comes from energy consumed during use, which makes reductions in these emissions a primary target for equipment manufacturers.
Summary
Semiconductor manufacturers and their equipment suppliers face a constantly evolving array of often conflicting design and development priorities. Tightly coordinated advances toward the monolithic goal of smaller transistors has given way to a sometimes-bewildering collection of new materials and technologies.
In this environment it is more important than ever for equipment and device manufactures to collaborate closely in developing the next generation of solutions, working together to gain a better understanding of these evolving challenges from those who must live with them every day.