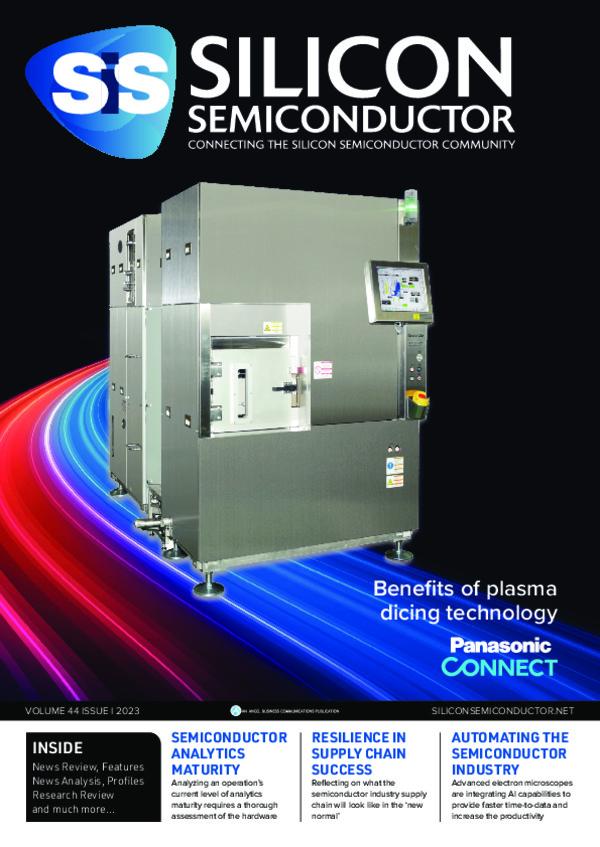
Semiconductor manufacturing analytics maturity: common barriers and methods to advance
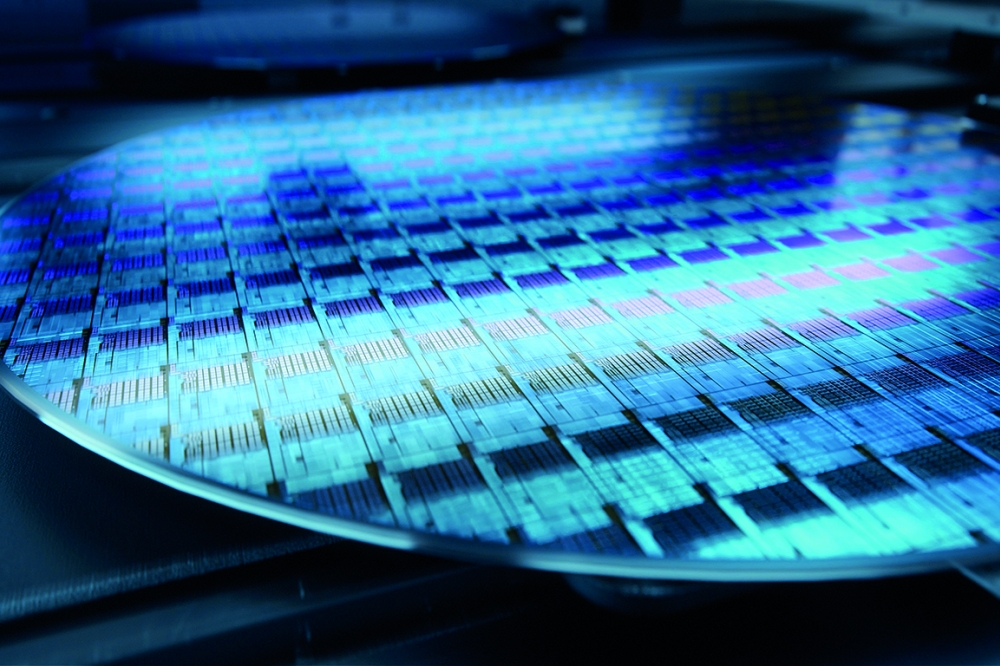
Analyzing an operation’s current level of analytics maturity requires a thorough assessment of the hardware, analytics software and data management practices.
By Yuji Minegishi, General Manager, Gigaphoton Inc.
Imagine a manufacturing line in which every tool and every process, including the interactions among them, were being optimized automatically for precision, accuracy and speed.
What if you had a data clean room, where data pertaining to every process and tool in the production line was ready to use — standardized and clean — and you could quickly apply any artificial intelligence (AI) model to any data set across every process and tool? What if equipment could notify you when servicing is due, or alert you that a tool in the production line might fail before you complete your process?
This could be the fab of the future. More and more, advanced analytics and Industry 4.0 solutions are being recognized as the key to increased uptime and yield improvement in semiconductor manufacturing.
An analysis by McKinsey calls advanced analytics “the next leap forward in semiconductor yield improvement,” and a recent report by Deloitte notes that leading Japanese semiconductor manufacturers are already seeing improvements in productivity and yield from using AI to build real-time predictions about errors, equipment failures and more. In fact, that same report noted that AI systems can analyze data thousands of times per minute — nearly 600 times the rate of human staff.
Figure. 1: The four levels of possible insights provided by analytics tools range from descriptive to prescriptive.
Analytics Maturity is the Key to Actionable Intelligence
For most semiconductor manufacturers, gathering data isn’t the problem. Sensor-laden fabs are sitting on enormous amounts of data. What’s challenging is the process of turning the data into actionable intelligence (Fig. 1).
Many manufacturers currently rely on labor-intensive manual processes to gather, analyze and visualize data. To set up thousands of charts, watch them and react to them is extremely inefficient. And with hundreds of parameters and the interactions among them to track on a daily basis, manual analytics processes can’t keep up; there are simply too many factors to comprehend.
Some chip manufacturers use AI-enabled predictive and prescriptive analytics for certain isolated processes or tools. But according to a recent survey conducted by the light source vendor Gigaphoton, only 26 percent of semiconductor manufacturers have access to this type of advanced analytics. Moreover, there are substantial impediments to achieving AI-enabled analytics integration across the entire production line.
Yet, achieving this level of advanced analytics capabilities is a goal semiconductor manufacturers must work toward to realize significant yield improvement and increased output in the context of increasingly complex manufacturing processes.
The Three Major Barriers to Advancing Analytics Maturity
Investing in Industry 4.0 solutions will help improve performance and efficiency, but turning an operation into the fab of the future can’t happen overnight. To achieve a more advanced degree of manufacturing analytics maturity, it’s important to know where the greatest impediments lie. Typically, barriers to achieving advanced manufacturing analytics maturity stem from three sources:
- Hardware
- Analytics Software
- Data Management
In terms of hardware, chip manufacturers typically use a mix of legacy and highly advanced manufacturing equipment, networks and sensors. The capabilities range from mere logging of descriptive data to receiving real-time data feedback and optimizing based on deep vendor-specific intelligence.
When it comes to analytics software, there isn’t a standardized platform for semiconductor manufacturing analytics. In fact, survey data reveals that 73 percent of semiconductor manufacturers weave together multiple disconnected equipment analytics solutions to get the information and intelligence they need. It is true that multiple software programs can be a sign of a robust data science program and not a symptom of inefficiency. But simply put, one standardized platform for on-premise semiconductor manufacturing analytics does not exist. Capabilities range from pulling basic data for viewing and manipulation to sending AI-driven feedback to equipment for performance optimization.
With data management it is important to reiterate the point that chip manufacturers have access to enormous amounts of data, but the way it’s currently received, stored and accessed often negatively impacts their ability to turn it into actionable insights. Data management solutions range from basic data storage in a single file to vast, frequently updated databases.
Fig. 2: The semiconductor manufacturing analytics maturity model developed by Fabscape aims to help chip manufacturers conceptualize progress toward advanced analytics.
A 5-Step Maturity Model Toward Progress
An analytics maturity model recently developed by Fabscape uses the three barriers of hardware, software and data management as a jumping-off point and further defines analytics maturity progression through five separate stages:
- Initiate
- Propagate
- Integrate
- Automate
- Radiate
Figure 2 illustrates that a manufacturer whose operation falls within the “Initiate” category is at the most basic level of analytics maturity across hardware, software and data. Only the most rudimentary data is logged within the simplest possible file formats, and processes are highly manual and ad-hoc.
On the other end of the spectrum are manufacturers who are at the highest level of maturity advancement, or the “Radiate” category as this model describes them. These are manufacturers who are already optimizing production with streamlined data collection, automatic equipment adjustments and advanced AI modeling techniques.
Even the most elementary semiconductor manufacturers can log, access and manipulate basic equipment data that is stored in individual files (e.g., CSV, XML, etc.). Yet to be truly successful, modern chip production needs to leverage more sophisticated techniques to gather, analyze and manage data.
This is where the power of AI truly shines: by developing advanced AI models, chip manufacturers can quickly trace failure points, optimize production and ultimately increase yield.
Identify Where an Operation Lies on the Maturity Scale
Analyzing an operation’s current level of analytics maturity requires a thorough assessment of the hardware, analytics software and data management practices. The end goal of such an analysis is to identify gaps and opportunities that will enable a manufacturer to move away from analytics practices that are descriptive and diagnostic, and toward advanced analytics that are predictive and prescriptive.
Semiconductor manufacturers seeking help in identifying their current maturity level and the associated opportunities can take the maturity assessment designed by Fabscape. By answering approximately 10 questions, survey respondents can learn where their operation lies on the maturity scale of 1-5 and receive tailored recommendations for next steps to advance their analytics.
Plotting where an operation is on this maturity framework can help manufacturers think about how they are currently using data to drive actionable insights and optimize systems. The journey may not be linear for some, but it is critical that chip manufacturers fill important gaps and develop a roadmap to achieve advanced analytics maturity.