New underlayer developments
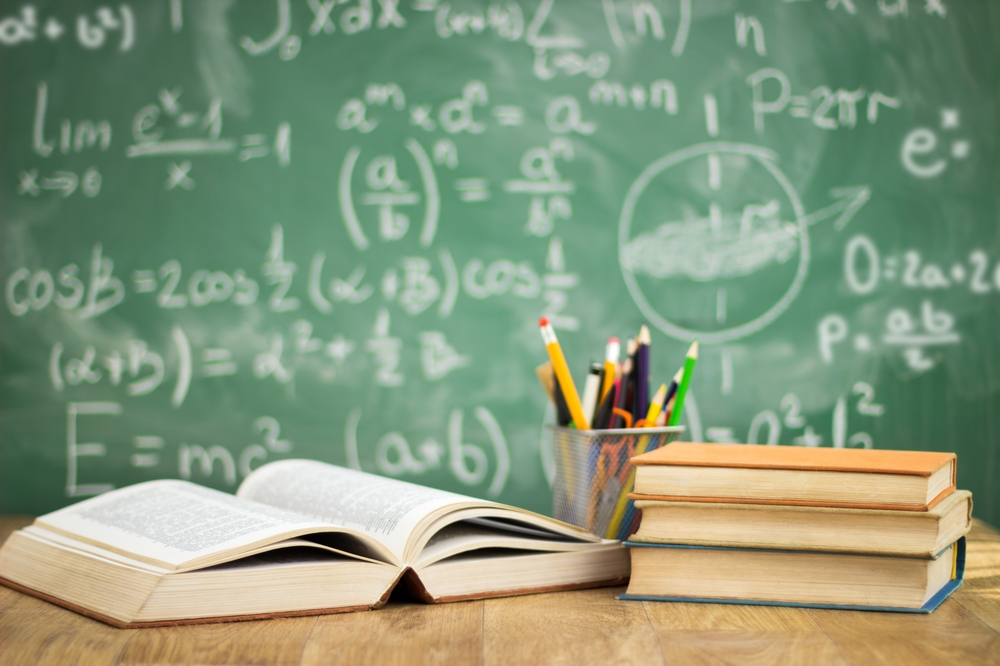
Brewer Science will present New Developments in Underlayers and Their Role in Advancing EUV Lithography at Critical Materials Council (CMC) Conference.
Demand for smaller devices requires material innovation to pattern small features
Extreme ultraviolet (EUV) lithography is used to pattern the smallest features in advanced semiconductor devices. The demand for smaller devices with more capabilities requires industry innovation in EUV processes and materials. Additionally, EUV plays a critical role in the evolution of technology and enables the continuous advancement of the semiconductor roadmap, as it provides the capabilities of higher processing power while using less energy and providing higher performance. However, one of the biggest challenges facing EUV lithography is material requirements, recognizing the critical role underlayers play in the patterning of EUV lithography.
EUV lithography underlayers play a critical role in the scalability of processes
Unlike bottom antireflective coatings (BARCs), reflectivity control is no longer the driving mechanism for underlayers. Underlayers are now necessary to support resist performance and enable scaling of the process. Underlayers that offer optimum adhesion while ensuring pattern defects are minimized are key. For pattern transfer, underlayers need to offer etch resistance beyond their predecessors and at a much-reduced thickness.
Material approaches presented that offer process and defectivity improvements for traditional EUV lithography schemes.
Joyce Lowes, Director of Emerging Materials Technology at Brewer Science, will present New Developments in Underlayers and Their Role in Advancing EUV Lithography at the Critical Materials Conference. This discussion will be featured in Session III: Immediate Challenges of Materials and Manufacturing on April 19 at 2:25 pm. In this presentation, a variety of material approaches are introduced that offer process and defectivity improvements for traditional EUV lithography schemes.
These materials demonstrate improved:
process window
depth of focus
LWR/CDU (line width roughness/critical dimension uniformity)