Avoiding unscheduled downtime in with Preventive Vacuum Service
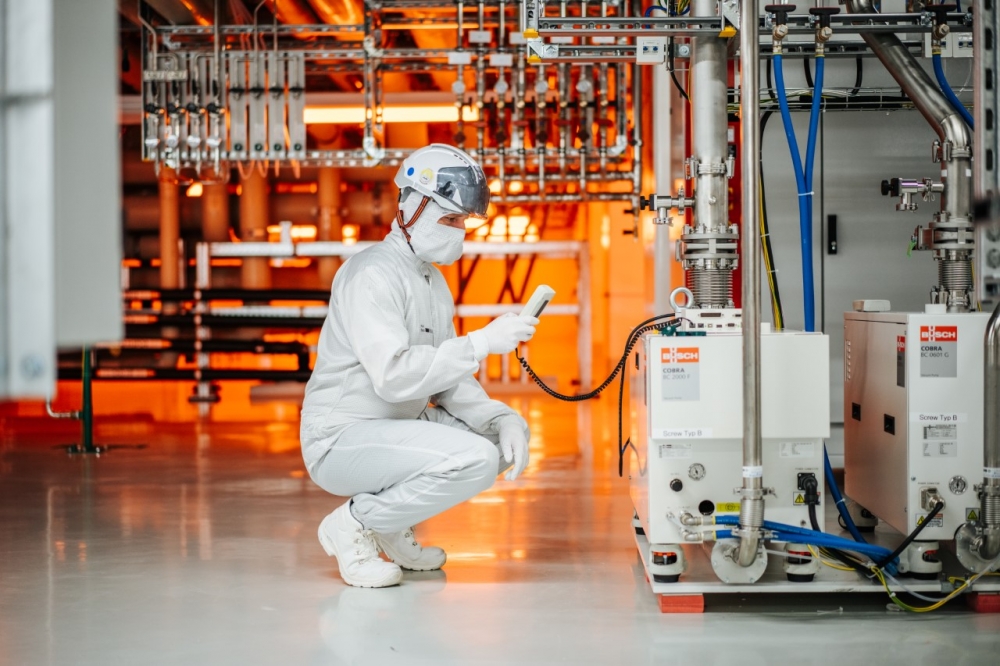
Busch Vacuum Solutions has developed a new service concept that ensures the availability of the vacuum supply, which plays an essential role in the semiconductor production process.
The global demand of computer chips is so high now, that existing product capacities can’t keep up. Unscheduled production downtimes in Semiconductor fabs must be avoided by any costs. Busch Vacuum Solutions developed a new service concept that ensures the availability of the vacuum supply, which plays an essential role in the semiconductor production process. This new service ensures to avoid unpredictable downtimes and even makes it possible to reduce the overall operational costs by up to 35 percent.
Busch Vacuum Solutions developed the unique vacuum pump remanufacturing service ARPQP (Advanced Remanufacture Product Quality Planning). The new concept of service follows the four core principles of the automotive world class standards of APQP in remanufacturing vacuum pumps. Following these principles is considered as the highest standard for safe production leading to an efficient, reliable, and optimized manufacturing. ARPQP represents a 'new level of reliability' for customers. The innovative service concept is focused on advanced thinking and preemptive action for prevention. Because the number one priority given to all suppliers in the semiconductor and flat panel market is the reduction of unscheduled downtime. Busch is the first company in the field of vacuum technology to have embraced this standard. Vacuum pumps are remanufactured to automotive quality standards.
ARPQP has already proven to be successful among many Busch customers. The reasons why customers decide to use ARPQP vary. Yet, they all have the same objectives: avoid unscheduled downtime and improve performance. Their experiences after a few months are convincing. In all fabs the failure rate for all types of vacuum pumps has decreased. One of the biggest Semiconductor manufacturers in the world experienced a 35 percent reduction in vacuum pump exchanges per year, after implementing ARPQP for the entire installed base of vacuum pumps. This improvement led to 7 percent increased production equipment availability, which is key when the loading of the Fab is already 100 percent.