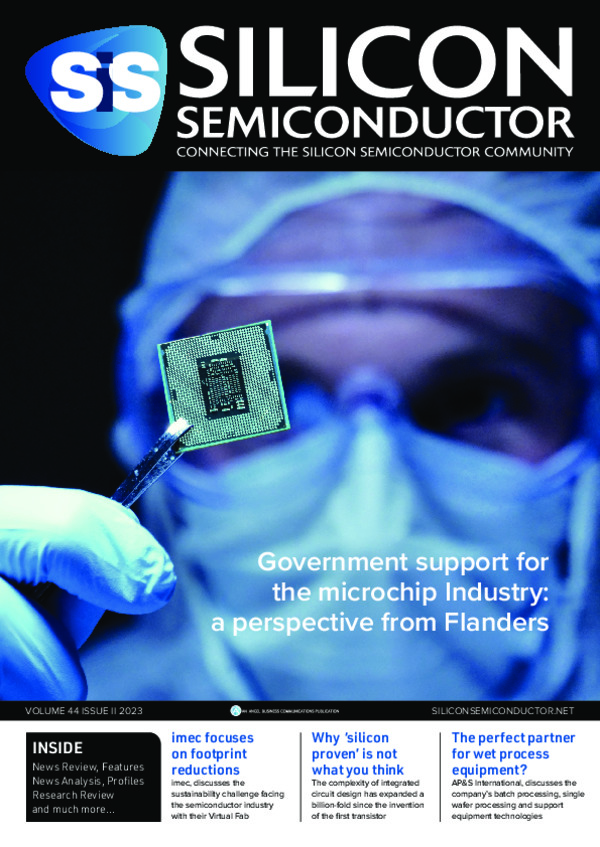
Fab scheduling is now so complex that it needs next-generation intelligent software
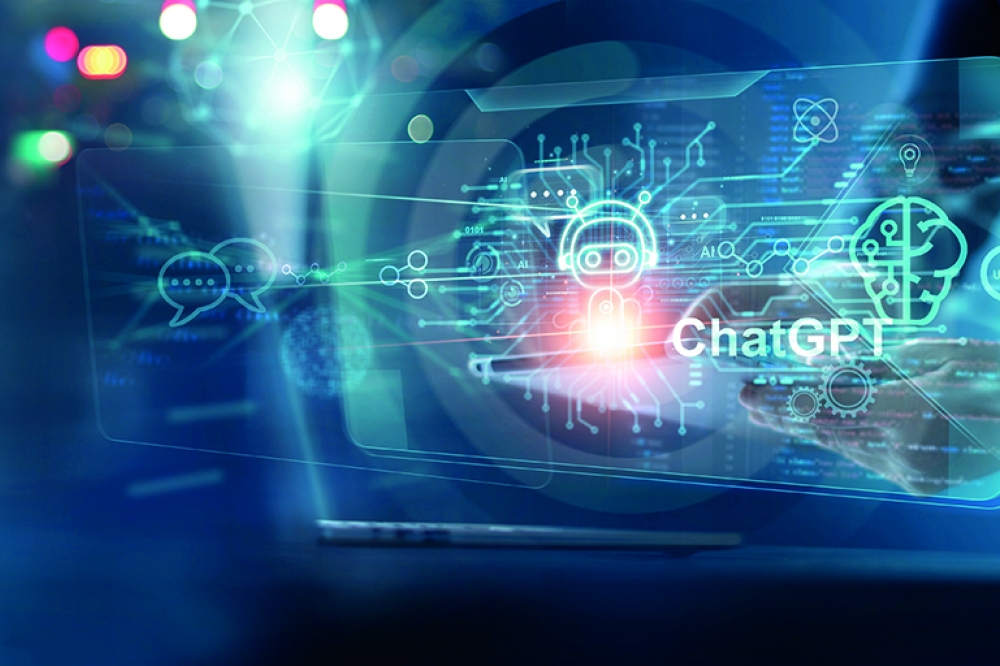
There are literally billions of possible ways to schedule all the work
through a fab, so finding the best way is an immense challenge. This is a
multidimensional problem that current heuristic scheduling software
just cannot handle. A new approach to the complexities of scheduling,
developed by Flexciton, is already making a significant impact in the
semiconductor industry.
BY JAMIE POTTER, CO-FOUNDER AND CEO, FLEXCITON
Global megatrends such as autonomous cars, AI and high performance computing are driving technological advancements and the need for ever more sophisticated chips and smaller process nodes. As a result, the wafer fabrication process is becoming even more complicated, with certain types of products requiring wafers to go through thousands of process steps and taking several months to manufacture. In addition to the challenge of complexity, there is an expectation for wafer fabrication to become more sustainable and energy efficient while increasing productivity and keeping the cost per wafer low.
The level of complexity in the production process is only expected to increase and unless fabs adopt new methods to simplify and streamline management, the challenge will become overwhelming. Chip companies must improve their performance and output by addressing the sophistication of their products. The current common approach of fabs to deal with complexity involves breaking down a big problem into smaller, more manageable ones, with specific teams assigned to tackle each challenge. In principle, this approach seems the right one, however, in practice it has significant drawbacks. Different teams within the fab often have different priorities and KPIs, which leads them to work in isolation. As individual teams strive to maximise their own KPIs, conflicts can arise as the KPIs of one area may be in opposition to those of another, negatively affecting the overarching fab objectives.
For example, while process engineers prioritise yield, industrial engineers are focused on reducing cycle time and increasing throughput, and manufacturing operators seek to maximise the number of moves per day. As an illustration, the objective of maximising the yield can impede the increase in throughput. Conversely, altering the recipe to enhance yield can impact throughput and cycle times, particularly if the changes require optimization over time.
Using scheduling to conquer complexity
Let’s dive deeper into the issue of complexity and how it impacts the scheduling of wafer production in particular. The process involves various stages such as; metrology, photolithography, diffusion furnace, epitaxy and more, each with its own unique set of guidelines and tools. The most common approach to scheduling is utilising rules-based software that dictates the sequence in which wafers are processed.
However, the sheer number of rules per area can be overwhelming, and industrial engineers often resort to simplifications and shortcuts to manage and control each stage’s parameters. Again, these ‘shortcuts’ may lead to suboptimal decisions made by the scheduler, with a negative impact on performance. Another problem with this approach is that it requires a huge amount of manual input from skilled industrial engineers to write and maintain the rules in an attempt to keep pace with a fab’s dynamic nature. In a fully operational fab, things are constantly evolving, which requires constant human intervention to ensure that scheduling rules are proactively monitored and updated. This is necessary to accommodate any changes that may occur and to create new rules in situations when new tools, recipes, or product mix are added. As the complexity of chips increases, so does the complexity of their production, necessitating frequent updates and additions to the rule set.
Figure 1: Rules-based scheduling requires proactive and time-consuming rules maintenance to sustain performance.
As shown in Figure 1, these constant changes have an impact on the performance of the rules-based scheduling. Sometimes it can make good decisions, but other times – due to the lack of intelligent algorithms – it can make decisions that are not optimal. It has significant peaks and troughs due to the time lags between introducing a change in a fab and, subsequently, new rules. In order to sustain performance, It does require proactive rules maintenance and full-time industrial engineering resources to work on it. This is currently a problem in itself. The industry is suffering from a skilled labour shortage and industrial engineers are particularly in high demand. Attracting a new generation of IEs to work in a wafer fab, often built in remote locations, is proving to be a challenge. If a huge amount of their capacity is taken up by tweaking a rules-based scheduling system, we are only making this challenge harder.
Working smarter, not harder
How can we effectively manage production complexity without compromising its potential? Attempting to simplify data is not the solution, as its complexity is what makes it a potent tool. Instead, by fully embracing smart manufacturing technologies that allow us to fully utilise the abundance of data, we can achieve a more complete and accurate understanding of a fab’s operations. Rather than simplifying the data, the focus should be on streamlining the process.
How does Flexciton software work?
There are literally billions of possible ways to schedule all the work through a fab so finding the best way is an immense challenge. This is a multidimensional problem that current heuristic scheduling software just cannot handle.
Flexciton’s next generation scheduling software is the only solution on the market that is able to solve this. It pairs powerful mathematical optimisation technology with smart decomposition techniques to work out solutions with complete autonomy. This advanced, intelligent software has the ability to generate an optimised production schedule within a few minutes by searching through billions of scenarios and honing in on the best possible one that achieves the overall KPIs. This repeating, iterative process ensures that it is continually updating the schedule to allow for any changes in fab conditions or business objectives (Figure 2).
Importantly, the software does not need a skilled industrial engineer to create an initial set of rules and to be modifying or creating new rules all the time. The intelligent software is learning all the time how to optimise the running of the fab to meet the given KPIs. If the objectives change, then it looks through the myriad of possible scenarios to find the one that meets the new objectives which is why it does not need any rules to guide it. This makes it the first and only, goal-centric and self-adapting scheduling solution.
Figure 2: When compared with conventional rules-based software,
Flexciton’s software is able to maintain optimal performance with
greater autonomy.
How Flexciton eliminates bottlenecks
The scheduling software looks at how the queueing changes over time for each toolset. The Flexciton scheduling application has a heatmap that illustrates any considerable queuing in front of a toolset in red and then going to green for toolsets with little or no queuing. The software then focuses on each red section and tries many different possible adjustments to the scheduling to balance the load across all toolsets and reduce bottlenecks. Because the software has the vital insight of future activities, it can see how a single change can have a knock-on effect not only on the timeline of the toolset in question but also the timeline of all the other toolsets.
Seagate case study
The photolithography area has a long and highly reentrant process with 1,600 steps and is the core of the fab so it is critical to have an optimised schedule. The results below are from one toolset in a live production environment, with an internal reticle library, where reticles can be moved individually between tools and cabinets.
Renesas case study
Timelink constraints are one of the most complex issues to handle in fab scheduling. They define the maximum allowed time between steps in the production of a wafer. Correct scheduling of timelinks is critical to helping minimise the risks of oxidation or contamination. This can happen when a wafer is queuing outside of a tool for too long, resulting in scrappage or rework that damages profitability. Renesas Electronics asked Flexciton to see if its intelligent scheduling software could improve this aspect of scheduling in the diffusion area of its wafer fab.
Figure 3: The results gathered from live deployment onto a Seagate
photo-lithography toolset, with 9.4% increase in throughput despite
reducing reticle moves by 5.3% and queue time by 4.3%.
What makes timelink constraints very hard to schedule is their interdependence. For example, by moving from step one to step two, the wafer enters the first timelink. When moving from step two, the wafer enters a second timelink which lasts until step 4. However, there can also be a third timelink constraint – known as a nested timelink – between step three and step four which overlaps the second timelink constraint (see Fig. 4). Therefore, step three has to be scheduled in a way that allows for both the second and third timelink constraints to be adhered. This example discussed is just for a few steps but, in reality, there could be hundreds of steps and many overlapping time constraints that need to be continually considered. This creates one of the most complex scheduling problems seen in a wafer fab, and any violation of the timelinks has a negative financial impact.
The software was run in a simulation environment that replicated the way that Flexciton’s scheduler would have run live at the Renesas fab. The results showed that a significant improvement in reducing timelink violations of 29% could be achieved. Additional improvements would be possible of a 22% reduction in the number of batches and an 11% reduction in queue time despite these two KPIs being conflicting (see Fig. 5). This is because decreasing the number of batches naturally means increasing the number of wafers in each batch, but this increases the queue times for each batch as operators wait for new wafers to arrive at the tool before processing them together. Currently, most fabs have no knowledge of the arrival times for future lots so operators can sometimes wait unnecessarily to maximise a batch size, causing more wafers to queue and damaging productivity. Uniquely, the Flexciton scheduler can see how lots are moving in time and can thus optimise the trade-off between number of batches and queue time to achieve the impressive gains seen on these conflicted KPIs.
Figure 4: This diagram shows an example timelink system between four
consecutive steps. The overlapping timelinks mean that after completing
step 3, the lot begins a new timelink (3) whilst still transitioning an
existing timelink (2).
Figure 5: The KPI improvements for timelink violations, number of
batches, and queue time against the baseline results at Renesas
Electronics.
Case study: a wafer fab in the EU
The fab was struggling to achieve efficiencies at clean and furnace due to complex timelink constraints. A similar off-line approach of a simulation environment was used to run Flexciton’s scheduling software. The customer was so impressed that the software is now on live deployment in the fab.
Jamie Potter, Flexciton’s Co-Founder and CEO, explains, “The key differentiator of our approach is that our software has the intelligence to predict what may happen in the future based on the current state of a fab (or WIP in a fab). It searches for the best solution amongst billions of possible solutions to continuously keep finding the optimal schedule that meets the KPIs to maximise a fab’s productivity and profitability. Humans and heuristics just can’t do that.”
Figure 6: The results gathered across the clean and furnace area at a fab in Europe.