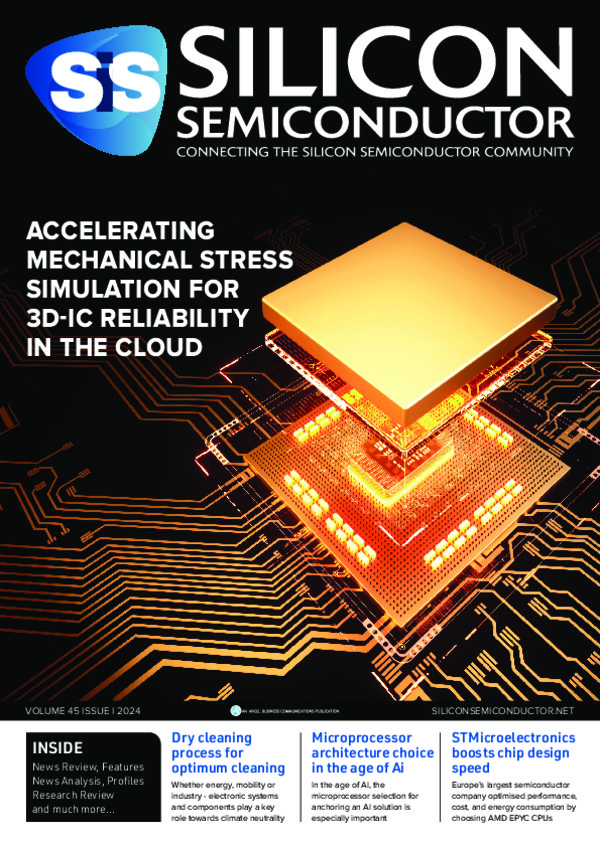
Dry cleaning process for optimum cleaning results in electronics production
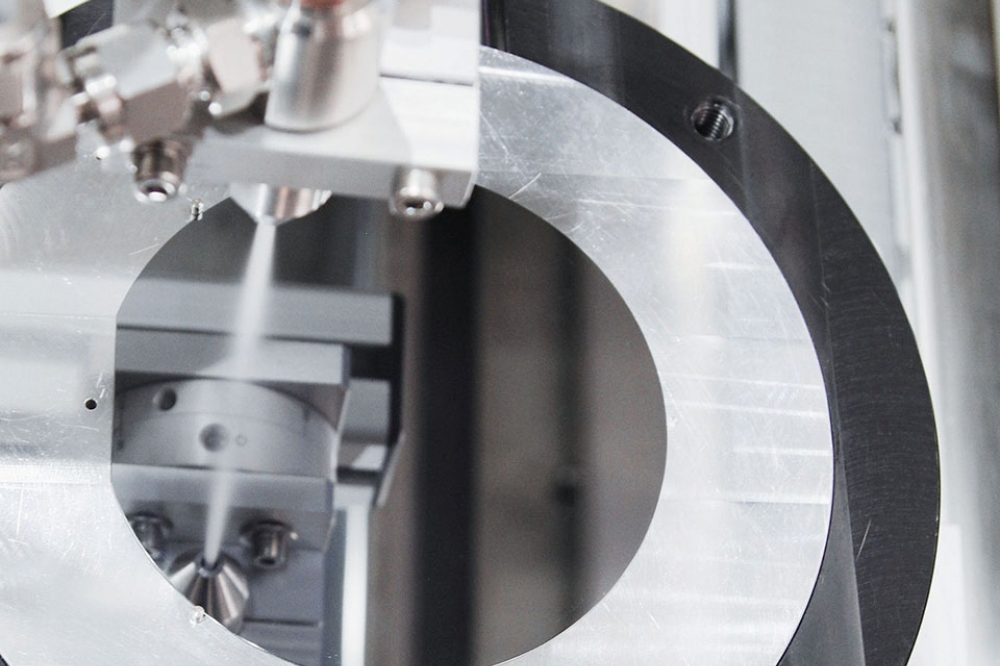
Whether energy, mobility or industry - electronic components and systems
play a key role in the transformation towards climate neutrality. Due
to higher demands on power density and reliability as well as new
solutions, the requirements for technical cleanliness during the
production of these components have increased enormously. The scalable,
cleanroom-compatible and inline-capable quattroClean snow jet technology
from ACP SYSTEMS is a dry, reliable and sustainable means of meeting
these requirements for a wide range of cleaning applications.
BY DORIS SCHULZ, FREELANCE JOURNALIST
TECHNICAL CLEANLINESS has a decisive impact on the performance, functionality, reliability and service life of electronic components and systems, from semiconductor & microsystem products, PCB joining & assembly technologies to the manufacture of battery cells & modules and the production of photovoltaics & laser-structured organic electronics.
The benchmark is the level of cleanliness defined as necessary for the downstream processes or end application, which must be achieved in a consistent and reproducible manner. To ensure compliance with the sometimes extremely high limits regarding particulate, filmic-organic and inorganic residual contamination, cleaning is usually carried out in a cleanroom. In a design adapted to the respective cleanroom class, the quattroClean snow jet technology from acp systems has established itself as a solution for such high-purity tasks.
Effective, dry and cleanroom-compatible cleaning solutions such as the quattroClean snow jet technology are a must in order to reliably meet the sometimes enormously increased requirements for technical cleanliness in the electronics industry or to clean pre-assembled components.
SCC 1 and highest filmic cleanliness levels demonstrably achieved
The technology concerns a dry process which is used for full-surface or selective parts cleaning. The cleaning medium is liquid carbon dioxide recycled from chemical production processes and the generation of energy from biomass. The carbon dioxide is guided through a wear-free, two-substance ring nozzle and expands on exiting to form fine snow crystals. These are bundled by a separate jacket jet of compressed air and accelerated to supersonic speed. When the easily-focused jet of snow and compressed air impacts on the surface to be cleaned, a combination of thermal, mechanical, solvent and sublimation effects occur, which is the basis of the cleaning action. The crystalline carbon dioxide sublimates completely during the process, leaving the treated surfaces completely dry. The detached contaminants are then extracted together with the process gas, thus preventing re-contamination of the parts or contamination of the surroundings. Time-consuming and energy-intensive rinsing and drying processes are no longer necessary.
Extensive tests have shown that the quattroClean snow jet technology consistently meets the requirements of surface cleanliness class (SCC) 1 according to VDI 2083, Sheet 9.1:2006 with regard to residual particulate contamination. In addition, particulate cleanliness corresponding to SCC 0.1 can be achieved with repeat accuracy for components that have been cleaned beforehand in an ultra-fine wet-chemical process. In the case of film residues, cleaning results are comparable to those of other ultra-fine cleaning processes such as wet chemical and plasma cleaning or vacuum bake-out.
The process is designed in the company’s own cleanroom test facility. Optimum process parameters are also defined here. The process media - carbon dioxide and compressed air - are prepared in such a way so as to ensure the air quality required by the semiconductor industry, for example.
Sustainable cleaning with Green Screen certified medium
In combination with process gas from Linde, the effective quattroClean process has been awarded the Green Screen Certificate for Cleaners & Degreasers from Clean Production Action. The independent, non-profit organization has thus created a benchmark specifically for cleaning media that are used as process chemicals in manufacturing, especially in the electronics industry. The certificate confirms that the process gas does not contain any chemical substances which are harmful to humans or the environment.
Cleanroom-compatible cleaning solutions for every application
To optimally tailor the cleaning solution to the respective requirements and production situation, acp systems offers a range of machines based on standardized modules as well as individually planned systems. The design and features of the solutions, which are made entirely of stainless steel, are adapted to the cleanroom class concerned. This ensures a cleanliness of 99.995 percent for the liquid carbon dioxide when it is prepared and a quality of 1.2.1. according to ISO 8573-1:2010 for the compressed air. If necessary, a gas scrubber can be integrated into the ultra-clean compressed air supply (XCDA) to filter out any traces of organic substances. The quality of the air generated meets semiconductor production requirements, for instance.
One of the solutions offered by acp systems is the compact JetCell with rotating nozzles. The flexible plug & play cleaning cell was developed for automated cleaning applications and is easily integrated into an interlinked manufacturing environment, e.g. immediately downstream of a punching or injection molding machine. Alternatively, it can be operated as a stand-alone solution. It boasts a high cleaning performance with an extremely low media consumption. During surface cleaning, which can be performed simultaneously from above and below, seamless process monitoring & control ensure that each part is treated with the previously validated process parameters. Integrated interfaces enable the digitally-controllable cleaning system to be connected to a higher-level host computer.
Cleanroom test facility for process design and validation
acp systems has its own cleanroom test facility for process design. This allows cleaning tests to be carried out in a validated ISO Class 7 cleanroom with zones up to Class 5 according to ISO 14644-1. All process parameters, such as the volume flows for compressed air and carbon dioxide, the number of nozzles, the area to be cleaned and the duration of the jet, are precisely tailored to the respective application, while also taking the material properties, type of contamination and required level of cleanliness into account. The values determined can be stored as part-specific cleaning programs in the system’s control unit.
Thanks to the dry quattroClean snow jet technology, a cleaning solution is available that can be used to perform a wide range of cleaning tasks in the electronics industry reliably and efficiently. The process not only ensures the required cleanliness of electronic, mechanical, optical and sensor components but also saves energy and resources at the same time.
The compact, stainless steel JetCell cleaning cell with rotating nozzles was developed for automated cleaning applications and is capable of cleaning large areas in a short time. It can be easily integrated into an interlinked manufacturing environment or operated as a stand-alone device
Main image: The dry quattroClean snow jet technology ensures that particulate cleanliness in accordance with SCC 1 is consistently achieved. In the case of filmy residues, cleaning results correspond to those attained with other ultra-fine cleaning processes.Photo credit: ACP Systems