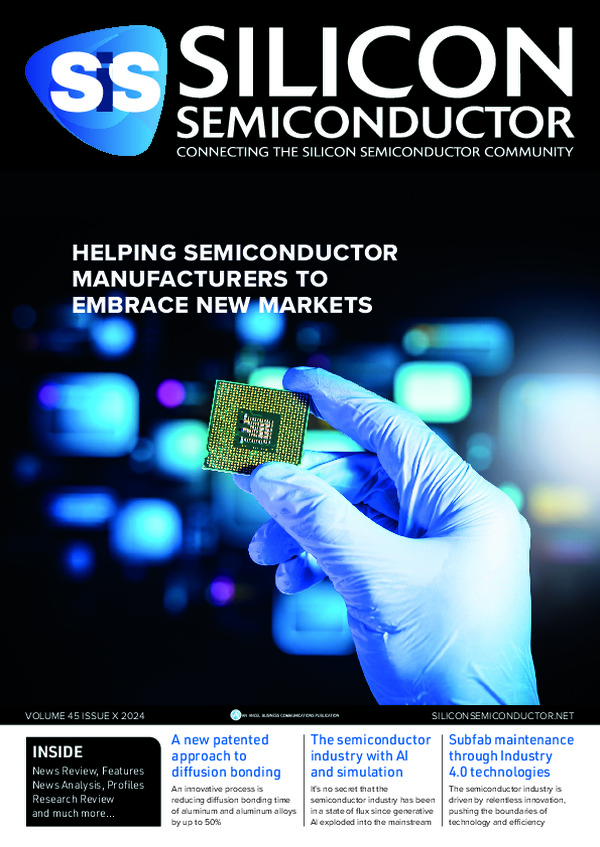
Evolving the semiconductor industry with AI and simulation
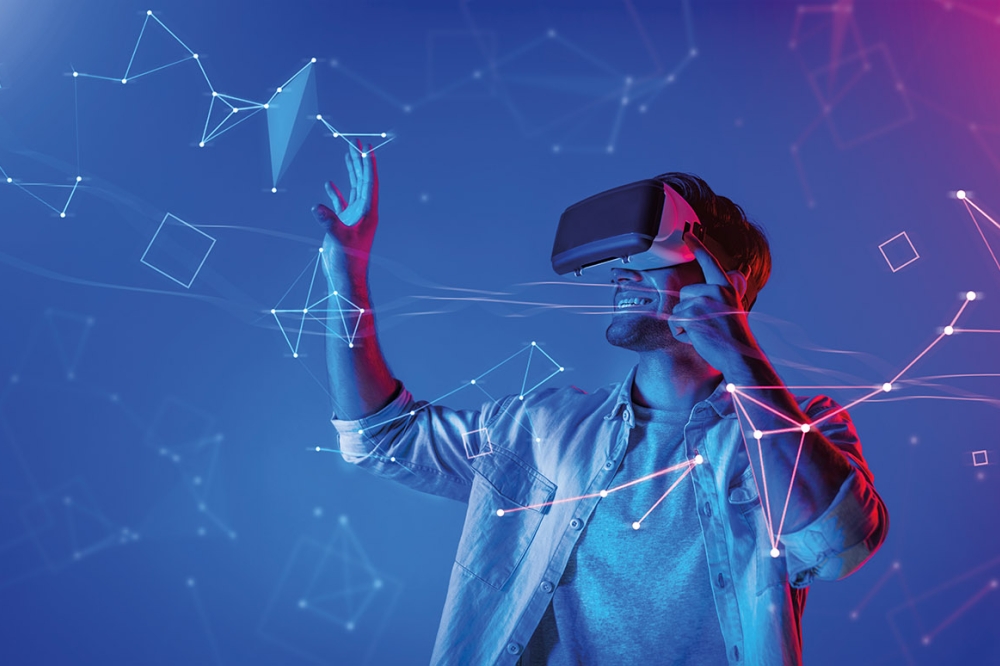
It’s no secret that the semiconductor industry has been in a
state of flux since generative AI exploded into the mainstream. And as adoption
of both AI models, and AI-powered smart products, continues to increase,
so will the already extreme demand for semiconductor chips.
By Mazen El Hout, Senior Product Marketing Manager, Ansys
The semiconductor industry is now on the front line of innovation, with Gartner predicting that global revenue will increase by 14% in 2025, totaling $717bn. Yet, the industry is scrambling to keep up with demand. Continued investment is supporting efforts; in the UK, for instance, £11.5m has been set aside to support semiconductor innovation and evolve the £10bn industry. Yet, the complexities of chip design and manufacturing, and skyrocketing demand following a global shortage, require increasingly sophisticated technologies.
Naturally, chip manufacturers are turning to tools like simulation and generative AI to overcome these challenges. By doing so, they can evolve intricate processes that traditionally consume vast amounts of time, money, and engineering resources. They can also explore how to support sustainable semiconductor manufacturing, without compromising on innovation. And beyond the semiconductors themselves, manufacturers can develop fabrication plants, or fabs, to drive development at scale.
The fact is, simulation alone can be immensely beneficial for chip manufacturers; generative AI just takes its capabilities a step further. But how exactly does this two-pronged approach work? With this in mind, let’s explore how simulation is already supporting chip manufacturing, and how AI can evolve design and development to push the boundaries of innovation and meet global demand.
The overarching benefits of leveraging simulation and
generative AI
In the case of semiconductors, simulation can help engineers
validate characteristics that would otherwise be difficult, time-consuming, and
costly to physically test. And since simulation can identify critical design
flaws before a semiconductor is built – be it a single chip or a giant factory
– it can accelerate the overall development cycle and reduce time to market, a
crucial objective for manufacturers.
But whilst simulation does play a vital role across semiconductor manufacturing, its benefits can be further enhanced through the power of generative AI. When a model is trained on specific data, it can produce accurate predictions in minutes, drastically cutting down computing time. As such, engineers can quickly adjust design parameters and receive immediate feedback through real-time simulations. Ultimately, this creates a loop; the more data the simulations generate, the more efficient and accurate the AI model will be. And in, for instance, the design process, this approach can be the difference success and failure.
Supporting reliability assessments in chip design
Chip design is neither swift, nor simple. Manufacturers
usually have to deal with nonlinear, unexpected behaviour, and need to take
electrical, thermal, and structural characteristics into account; even the
slightest modifications or error can impact other components. Additionally,
engineers can struggle with successfully mapping spatial distribution
uncertainty and variations in chip parameters, including die size and heat
transfer coefficient (HTC) values. Whilst simulation as a standalone tool can
support here, engineers risk spending unnecessary time simulating, modifying,
and re-simulating a single chip, and the overall complexities of the design
process mean that scalability is limited.
Again, complementing simulation with generative AI can add additional benefits, alleviating these challenges. Take a thermal analysis as one example; if an AI model is trained on datasets generated from thermal simulations, it can quickly generate a temperature distribution map and accurately pinpoint thermal critical locations. This empowers engineers to make the right design modifications that can ultimately optimise thermal performance, manage temperature fluctuations, and mitigate overheating issues. But reliability assessments are just one piece of the puzzle. To meet global demand, chip manufacturers need to be able to experiment with more innovative and sustainable design choices.
Powering sustainable semiconductor innovation
Sustainability is influencing product design across every
sector; the semiconductor industry is no exception, thanks to its significant
environmental output. For instance, fabrication plants require significant
amounts of water and energy to manufacture chips, whilst a complex global
supply chain – including the extracting of large amounts of raw materials, and
worldwide distribution – contribute to greenhouse gas emissions. In conjunction
with this, many consumer products that rely on semiconductors, like smartphones
and laptops, are designed with planned obsolescence in mind. This means that
more chips are being discarded, keeping demand up and generating material
waste.
Improving sustainability in the semiconductor industry calls for a collective effort. But there are steps manufacturers can already take here, like combating waste reduction in chip design. Simulation can be of use here; for instance, it can identify areas of excessive power consumption and optimise energy efficiency. Simulation also calls for fewer physical prototypes are made, so less waste is created. So where does AI fit in? The technology allows engineers to gain insights into the material process-property relationship through AI-based material selection. Essentially, a manufacturer’s material data is used to predict how different materials can impact product design and performance, which enables better decision-making for sustainable design. Evidently, giving manufacturers next-generation tools and technologies can open the door to new innovations in the chips themselves. But how can AI-infused simulation support the industry on a larger scale?
Overcoming fabrication plant challenges to enable innovation
at scale
Chip design isn’t the only focus for manufacturers. To
sustain the global supply chain, fabrication plants need to evolve their
capabilities, but this comes with its own challenges. As fabs strive to keep up
with the pace of demand for chips, equipment can run continuously for weeks or
even months at a time, increasing the chance of machinery fatigue and running
the risk of costly and time-consuming maintenance. And if failures do
unexpectedly occur, organisations must decide between halting production immediately,
or waiting for a scheduled maintenance window. Since a single tool failure can
have an impact on the entire manufacturing process, organisations can’t afford
to gamble on the health of their operational equipment.
Manufacturers must mitigate fatigue and failures to avoid disrupting these highly interconnected processes. And to do so, they can look to AI-powered digital twins. These connect data from physical semiconductor manufacturing assets to their simulated counterparts, allowing engineers to monitor equipment health in real-time, and predict issues before they occur. Moreover, if the AI model is lacking data on specific defects, it can create a synthetic dataset to incorporate this and train the digital twin. By working in tandem, AI and simulation will allow semiconductor manufacturers to maintain operational efficiency, avoid production downtime and better anticipate maintenance.
The future of semiconductor manufacturing
For semiconductor firms, the demand for chips isn’t slowing
down. But the right tools can be crucial in helping bolster supply and maintain
a competitive edge – and, naturally, AI is the common thread. AI-accelerated
solvers, AI-powered digital twins, and AI-based material selection are just
three examples of how technology can evolve processes, underpin advances in
design, and keep operations running smoothly. And the organisations that invest
in these capabilities now will be better positioned to dominate the supply
chain and pave the way for the future of the semiconductor manufacturing.