Japan Semiconductor Facility Eradicates Oxygen With Membrana Degassing Systems
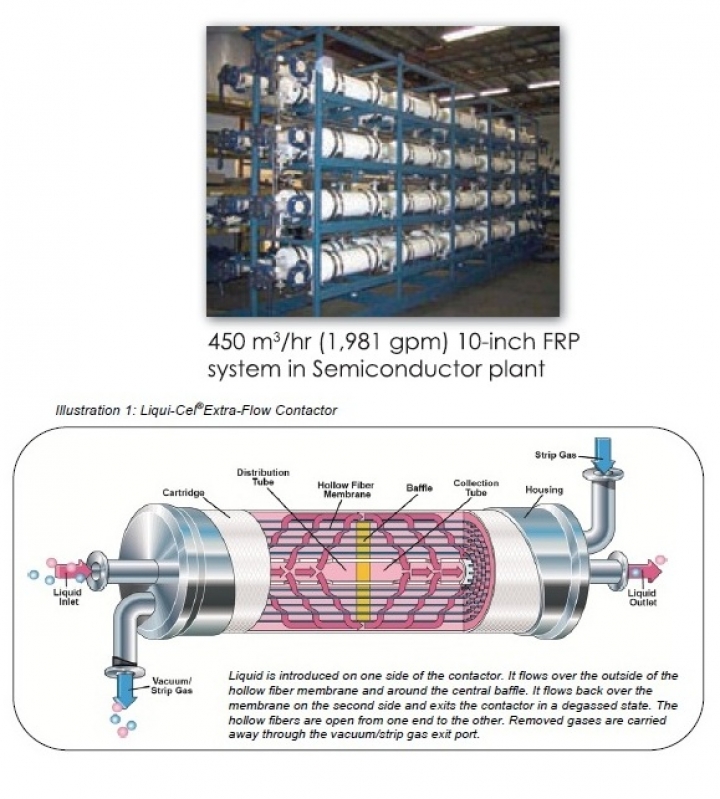
Membrana-Charlotte, a Division of Celgard, LLC, has recently
installed Liqui-Cel 10 x 28-inch Membrane Contactors at a Semiconductor plant
in Japan to deoxygenate process water.
The degassing system is designed to process 264 m3/hour (1,162 gpm) of water and is configured to run with fourteen membrane contactors in parallel by one in series. Using a combination of vacuum and nitrogen as a sweep gas, dissolved oxygen levels are targeted to reach less than 1ppb at the outlet. System start-up began in April 2012.
Liquid degassing is required by semiconductor and microelectronics
manufacturers. Oxygen gas negatively impacts many processes; it is corrosive
and can oxidise water treatment system components. In the semiconductor market,
high levels of dissolved gases can reduce wafer yields and hamper process
speeds.
Membrana boasts its Liqui-Cel Membrane Contactor degassing technology is clean and requires a much smaller footprint compared to other technologies and has low operating costs. What's more, chemical usage required to achieve low dissolved gas levels may also be reduced.
Liqui-Cel Membrane Contactors are replacing older deaeration technologies in many industries including microelectronics and power. These devices are currently processing over 620,000 m3/hr (2.7 million gpm) of liquids worldwide and have been operating in a variety of applications for over twenty years.
Liqui-Cel Membrane Contactors utilise thousands of Celgard Microporous Hollow Fibres to add or remove oxygen, carbon dioxide, nitrogen and other gases to or from various liquids. The Extra-Flow design incorporates a baffle in the middle of the contactor, which directs the liquid radially across the array.
A strip gas or vacuum, either separately or in combination, is applied on the lumenside of the hollow fibers. Due to its hydrophobic nature, the membrane acts as an inert support to allow direct contact between a gas and liquid phase without dispersion. The dissolved gas in the liquid travels through the pore by applying a higher pressure to the liquid stream relative to the gas stream.