Aqua Membranes collaborates with Micron Technology
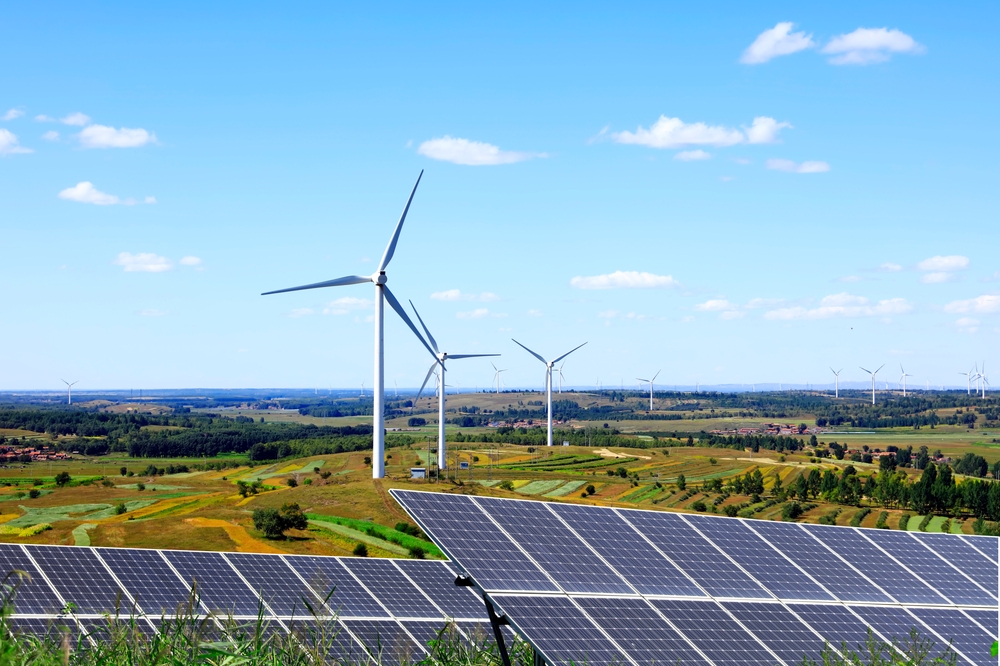
Semiconductor pilot shows 20 percent energy savings and four-times lower water fouling for piloted membranes.
Aqua Membranes, a water technology company specializing in sustainable reuse, is sharing preliminary results of an ongoing pilot project with memory chip giant, Micron Technology, Inc. Pilot implementation included a head-to-head comparison between Aqua Membranes’ Printed Spacer Technology® and a standard reverse osmosis (RO) with traditional mesh element architecture at Micron’s Boise, Idaho fabrication plant, with the base RO membrane type being the same for both cases. With the Printed Spacer Technology, the teams observed a 20 percent drop in overall system energy consumption after four months of continuous operation of the pilot. The feed to reject pressure drop (dP), a measurement used to gauge water fouling in RO applications, also significantly improved, averaging 6.03 pounds per square inch (PSI) with mesh versus 0.6 PSI with printed spacers.
In 2021, Micron invested in Aqua Membranes to help accelerate the development of their Printed Spacer Technology in microelectronics applications. Micron plans to continue testing Printed Spacer Technology in different RO applications and evaluate performance against other commercially available membranes for its full-scale systems.
“Utilizing Aqua Membranes’ components in our RO water treatment systems to reduce energy consumption and the associated emissions supports Micron’s ongoing commitment to sustainability improvements, while maintaining our stringent quality standards,” said Elizabeth Elroy, vice president of Global EHS and Sustainability at Micron. “Through two years of continuous development, we are thrilled to see our collective efforts and hard work paying off, and we’re grateful for our collaboration with Aqua Membranes to help us move towards this goal.”
The pilot system is comprised of two identical units running in parallel, which allows the Printed Spacer Technology to run in direct comparison with mesh spacers employed in the same RO skid. Variable frequency drives (VFD) are used to adjust primary pressure on each system and maintain a constant 63 gallons per minute (GPM) of product water at a recovery rate of 65 percent from the 16 element systems. Banking was 3:1 with four vessels total and four elements per vessel.
A slower rate of fouling allows for longer intervals between cleaning, which results in lower maintenance costs and extends the longevity of the membrane life. This, combined with the lower energy consumption, means Aqua Membranes’ Printed Spacer Technology elements show potential to significantly lower the cost of RO membrane operation. With the success of the Boise pilot, Micron is exploring usage of Aqua Membranes’ Printed Spacer Technology elements in its high volume fabs, including at its planned facility in Clay, New York.