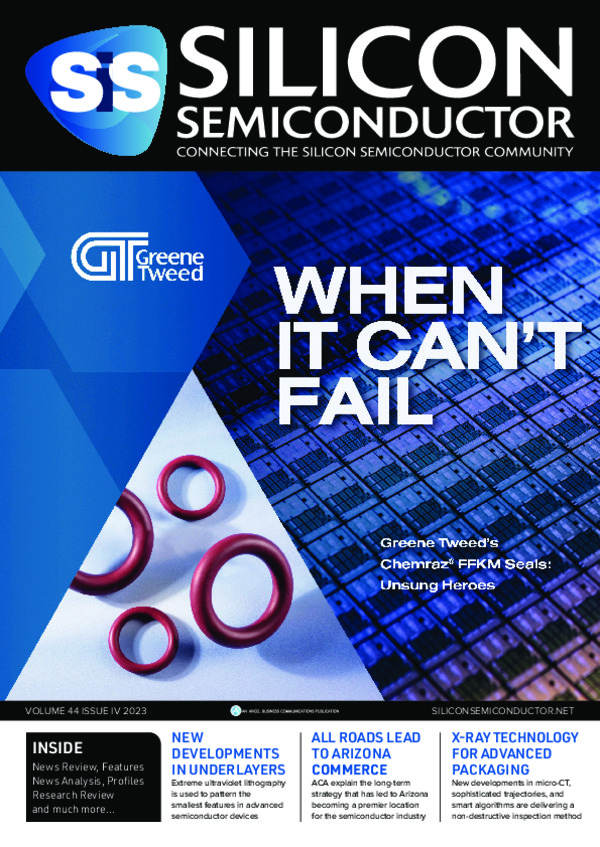
New developments in underlayers and their role in advancing EUV lithography
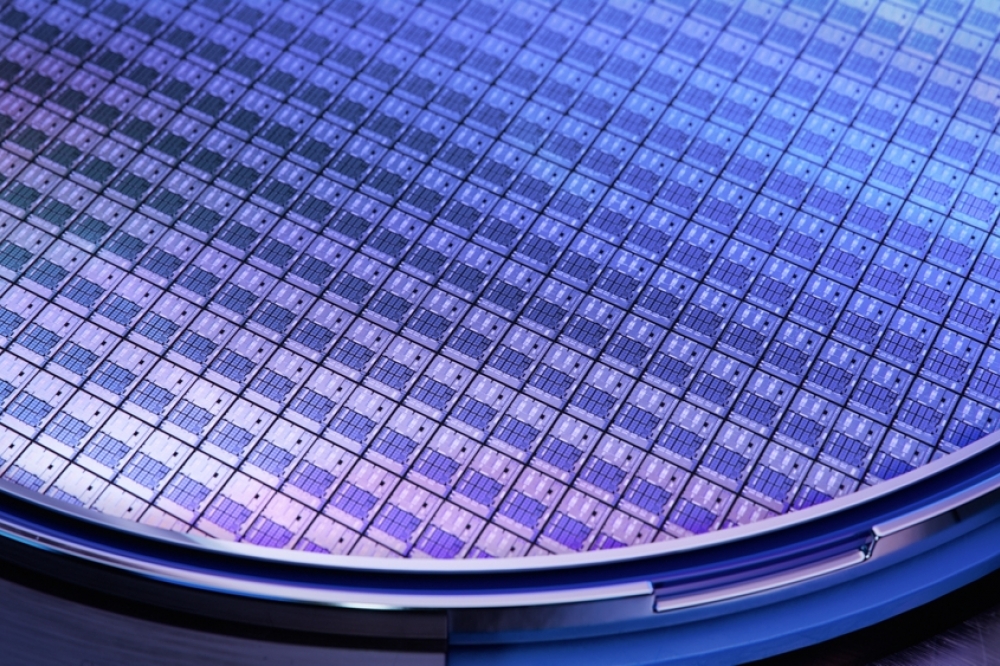
Extreme ultraviolet (EUV) lithography is used to pattern the smallest
features in advanced semiconductor devices. The demand for smaller
devices with more capabilities requires industry innovation in EUV
processes and materials.
By Joyce Lowes, Director, Emerging Materials Technology, Corporate Research and Development, Brewer Scientific.
EUV plays a critical role in the evolution of technology and enables the continuous advancement of the semiconductor roadmap, as it provides the capabilities of higher processing power while using less energy and providing higher performance. However, one of the biggest challenges facing EUV lithography is material requirements, recognizing the critical role underlayers play in the patterning of EUV lithography.
Unlike bottom antireflective coatings (BARCs), reflectivity control is no longer the driving mechanism for underlayers. Now, underlayers are necessary to support resist performance and to enable scaling of the process. Underlayers that offer optimum adhesion while ensuring minimization of pattern defects are key. Beyond just lithography performance, in cases where the underlayers also serve a dual purpose as an etch mask, they need to offer etch resistance beyond their predecessors and at a much reduced thickness.
Brewer Science introduced our first EUV underlayer material in 2010, E2Stack® AL412 material, which serves as the standard for EUV tool qualification and resist screenings. This material delivers excellent adhesion and resist compatibility for lithography. Since then, Brewer Science has introduced a variety of material approaches that offer process and defectivity improvements for traditional EUV lithography schemes. These materials demonstrate improved process window, depth of focus, and LWR/CDU, and can be used across a variety of EUV patterning applications.
Figure 1. Comparison of underlayer properties on traditional CAR and MOR.
Underlayer Challenges for EUV
With the adoption of EUV into more layers and the introduction of high-NA tools quickly approaching, the minimum pitch as defined in DRAM and Logic roadmaps requires photoresist thickness continue scaling down, reaching as thin as 15 nm in the next few years. As expected, the underlying film stack will need to scale as well, all while maintaining existing properties and often doing more.
The industry has already moved from traditional 30 - 80 nm deep UV (248 nm or 193 nm) BARC layers down to 5 - 20 nm EUV underlayers. This thinning-down trend will continue (likely towards 1 – 10 nm) as high NA becomes a reality. Meanwhile, to be able to print ever-shrinking defect-free EUV features with the lowest possible dose while maintaining reasonable process window, more functional demands are being added to the underlayer requirement list. Just to name a few, the underlayer needs to provide enough adhesion to prevent pattern collapse but not too much to cause scum, it needs to be as thin as possible but at the same time provide the required etch selectivity uniformly across a 12-inch wafer, and it is also called on to help reduce the dose but without too much chemical exchange with the resist. Overall, an optimum EUV underlayer design needs to have at least three main challenges in mind: enhancing the lithography performance with compatibility to a wide range of resist vendors and types, thickness and chemical homogeneity control to minimize both coating defects and stochastic impact to the imaging/developing process, and the perfect etch selectivity for pattern transfer demanded by different resist types and integration schemes.
Figure 2. Thickness uniformity studies.
Obviously, lithography performance needs to be perfect. When films are at a normal thickness, bulk properties have large influence over performance. However, with thin films, those bulk properties are less significant, since there really is no bulk left and behavior at the interface is more important. All of the desired properties need to be packed at the interface. Adhesion to and interaction with the resist at the interface needs to be optimized to get the right balance. And, unlike traditional ArF or KrF resists, each EUV resist from each vendor has its own unique chemical designs and working mechanisms, so underlayers need to be adjusted for each different resist formulation. More preferably, the underlayer needs to be “universal” to be compatible with all the resists.
Reducing the thickness in itself is a critical challenge. At 5 nm, control of uniformity across the wafer is tricky, with the film sensitive to many factors in the tool, such as exhaust and hotplate uniformity. Compounding that as well are chemical effects, such as distribution of components and their effect on crosslinking rate. Even though the thin films are at very low solids content, defectivity reduction does not get easier. Tiny defects that were previously tolerable or even ignorable compared to the rest of the bulk film now become dominant and problematic at the interface. These defects now may start becoming larger than the thickness of film or CD of the features and so become more impactful. Traditional methods that were used to remove larger defects are running into a wall in the EUV era where everything shrinks in size and thickness, requiring more sophisticated filtration and other techniques to purify the materials, and more innovative metrologies to even detect the defects.
Lastly, there is pattern transfer. These ultrathin underlayer films will need to deliver at the same but more likely at a better level of etch selectivity than their much thicker precedents. This applies to both silicon- and carbon-based films. Depending on the integration scheme and etch setup, faster or slower etch rates are prescribed for the EUV underlayers, but sometime the underlayer needs to be both faster and slower (under different etching gases), all at a thickness as thin as 1 – 10 nm.
Figure 3. Primer concept and comparison of HMDS priming vs spin-on primer film.
Underlayer Effects on CAR and MOR
In figure 1, two examples illustrating the role the underlayers play in EUV with a traditional chemically amplified resist (CAR) and metal oxide resist (MOR) are shown. With CAR, one factor at play for performance is surface energy. With this combination, as seen on the left, underlayers with various polarities were screened. As the underlayer became more polar, this change leads to less scumming/cleaner profiles. At lower polarity, scumming became more evident, likely due to too much interaction of the exposed resist and the underlayer. But, too much of a good thing is sometimes bad, so there needs to be a balance to avoid too little adhesion and causing collapse.
With the MOR, surface energy is important, and the collapse/adhesion trends are similar to CAR. Some impact on thickness versus dose has been seen, which was not observed with CAR. When the underlayer became thinner, the resist required higher dose, which could be explained through some chemical interactions.
Figure 4. Comparison of primer versus traditional crosslinked film.
Tackling Thickness Issues for Extreme Uniformity
Coating uniformity at EUV dimensions requires extreme uniformity. At a normal thickness, for an ArF underlayer, thickness variation targets can be as low as 5 angstroms. At 5 nm, that same variation is still expected. Unfortunately, it’s not as simple as repurposing a 30-nm film by diluting it and have it perform the same. Striations as seen in Figure 2 with the radial striations in the haze image from an SP5 on the left, and thickness deviation from center to edge are common problems that occur when the film is thinned, causing process window errors, CD mis-uniformity and other issues. To eliminate striations or to reduce thickness uniformity down to target, careful optimization of the formulation is necessary. And since all underlayers are not created equal, when the formulation changes for better adhesion, slower etch rate, or the need to replace or remove PFAS components such as surfactants, each material will need to go through another optimization step to fine tune its uniformity.
Figure 5. Primer on top of problematic underlayers.
Underlayers for Adhesion – How Thin Can We Go?
As films get thinner, a question arose: how thin can a traditional spin-on film actually coat before it starts to fail? Does a spin-coated polymer film actually coat consistently across the wafer when thinned down? Is there enough polymer for adequate coverage? A few methods can be used to characterize the film and coverage across the wafer. Of course, thickness , but also density, roughness via AFM, contact angle and surface energy are used. Using this data, it was found that high quality films can be obtained down to 4 nm and likely even thinner.
With those same thin films, evaluation with both CAR and MOR was conducted at 28-nm pitch. With CAR, no change in dose or best focus and CD were seen as thickness was decreased. Roughness values varied a little bit, but overall performance was very similar. But again, overall, thin films were proven to work as well as their thicker counterparts.
Figure 6. Silicon loading content studies.
Going Ultrathin – Spin-on Primer
So how much thinner can we go? If 4 nm works, why not 2 nm or even1 nm? One concept that has been borrowed from other areas may be a path to get the properties needed for performance but alleviate those issues seen with traditional crosslinked films. This spin-on primer concept can be used to functionalize a variety of surfaces including other spin-on films or CVD-deposited layers through just a simple grafting process. These types of materials have the ability to tune or adjust adhesive properties while allowing for truly ultrathin films.
With this ultrathin film, it is important to verify that it is indeed uniform. In addition to just thickness uniformity, using those same characterization methods as before, including surface roughness and surface energy across the wafer, is is possible to ensure the film is consistent across the entire wafer surface.
Here are a few examples of how ultrathin layers will work with different film stacks. First, since this is a primer, it can be compared to the traditional HMDS primer applied on silicon. With the HMDS priming, lines will print with this resist, but adhesion is poor and collapse shows up early. Looking at cross-sections, the resist has quite a bit of top loss. With the spin-on primer applied onto silicon, no collapse is observed across dose and resist top loss is minimized.
Figure 4 demonstrates a comparison of a spin-on primer to a traditional crosslinked film at 5 nm. While the crosslinked film does perform well, replacing that layer with the thinner equivalent can lead to wider defect-free depth of focus window and better roughness. Less scumming and top loss is also observed.
Figure 7. CAR pattern transfer flow process.
And lastly, what does this layer look like when it is added on top of other layers? Can the primer be used to ‘fix’ an existing underlayer? In Figure 5 (top row), there is a traditional silicon hardmask that was not optimized for EUV use. Looking at the focus/exposure matrix, dose in the x-direction and focus in the y-direction, it can be seen that with this underlayer, the resist has significant collapse and line breaks as shown in blue, and possibly only one good die as shown in white, but it is probably questionable, too. Take that same layer, graft a spin-on primer with the right resist compatibility, and adhesion is fixed. Figure 5, (bottom row) shows what happens when a traditional spin-on carbon film is modified with the primer film. Original performance is not too bad, but there is a bit of bridging and scumming in the low dose region seen in orange. But with the spin-on primer, the bridging and subsequently the defect-free window is improved in that area.
Addressing Pattern Transfer – Silicon Hardmask
As the film stack gets thinner, maintaining adequate etch resistance is another main challenge. When films are not optimized, some familiar pattern transfer defects that crop up are missing holes, line breaks, wiggling and others. These could be caused by several things, including poor adhesion or scumming, but in this case it is important to review how inadequate etch resistance of the silicon hardmask causes problems.
How much silicon is ideal? Not all silicon hardmasks are alike and not all pattern transfer needs are the same. As seen in the line/space example in Figure 6, the low-silicon hardmask obviously fails, but a medium-silicon hardmask looks good. However, when using the same materials for contact holes, failure is seen with medium-silicon hardmask, indicating that better performance is needed.
Figure 8. ADI and AEI results with CAR resist and HT-SOC.
As the move to even thinner silicon hardmasks proceeds, how much silicon is really needed, especially approaching 5-nm-thick films? The performance is all tied to etch rate. The higher the silicon, the slower the etch rate in oxygen, and consequently, the longer the hardmask lasts during the carbon etch. Traditional silicon materials typically range in the medium to high level of silicon, which would allow for use between 7-10 nm in most cases. However, getting to higher silicon has been difficult for multiple reasons, including chemistry and defectivity, but new materials are now able to get to levels that will enable 5-nm etch equivalence and maybe even beyond.
Addressing Pattern Transfer – Carbon Hardmask
With silicon taken care of, how about the carbon hardmask? The most logical way to provide a carbon underlayer has been to use alpha carbon or other films, but in certain applications, there may be limitations to what those films can do, such as planarization, gap-fill, optimized resist adhesion, or reworkability, so the use of a spin-on option with optimized etch rates may be needed.
To check the effect of variations in the carbon layer, a standard pattern transfer flow using a CAR and EUV lithography is used. In Figure 9, a simplified stack and flow for checking the pattern transfer capability into a carbon layer using EUV patterning in shown. In this example, a standard silicon layer is coupled with different carbon films, and the lithography and etch steps are performed before checking for wiggling and other failures. After lithography, both alpha carbon and a high-temperature spin-on carbon (HT-SOC) films have good almost identical lithography performance. Dose and process window is similar. This is not unexpected since there should be minimal
impact from a layer buried beneath the silicon hardmask.
Figure 9. Pattern transfer data (ADI) for MOR plus SOC layer.
Moving on to the next step, after etch is the key to checking for differences. This is where line wiggling is typically apparent. With some older generation films with lower carbon content, it can be very difficult to obtain patterns at EUV wavelengths. But, with high-temperature carbon materials, like OptiStack® SOC450, that were designed with higher carbon content, there is enough etch resistance to perform similarly to an alpha carbon film, as shown in Figure 10.
Pattern transfer with CAR is well known, but MOR is different and the stacks used will vary from a typical CAR. In this example, the carbon film is directly under the resist, so planarization or other properties might not be needed, but it still serves two functions, adhesion and etch resistance. In Figure 8, a traditional spin-on carbon is compared to a high-temperature/high-carbon film. As discussed previously, litho performance is highly dependent on resist interaction, so those differences in the changes in process window and exposure latitude are apparent, but not terrible and the process can proceed to etch. After pattern transfer, the impact of carbon film composition on performance with MOR is apparent.
Figure 10. SOC etch rate and lithography comparison (AEI) for MOR.
In Figure 10, a comparison of etch rates shows that a traditional SOC is faster than the higher-carbon/high-temperature alternative. With that faster-etch-rate material, the CD delta changes significantly, as shown on the bottom chart in red, reducing the process window as seen on the left. With the slower material (high-temperature carbon), there is still some slight CD change, but far less and the overlapping process window is much better..
Finally, it is necessary to analyze how these materials perform for roughness and subsequent overlay. Under the MOR, LWR and LER for the high-carbon spin-on film are comparable to alpha carbon.
Figure 11. Alpha carbon vs HT-SOC (AEI) with MOR.