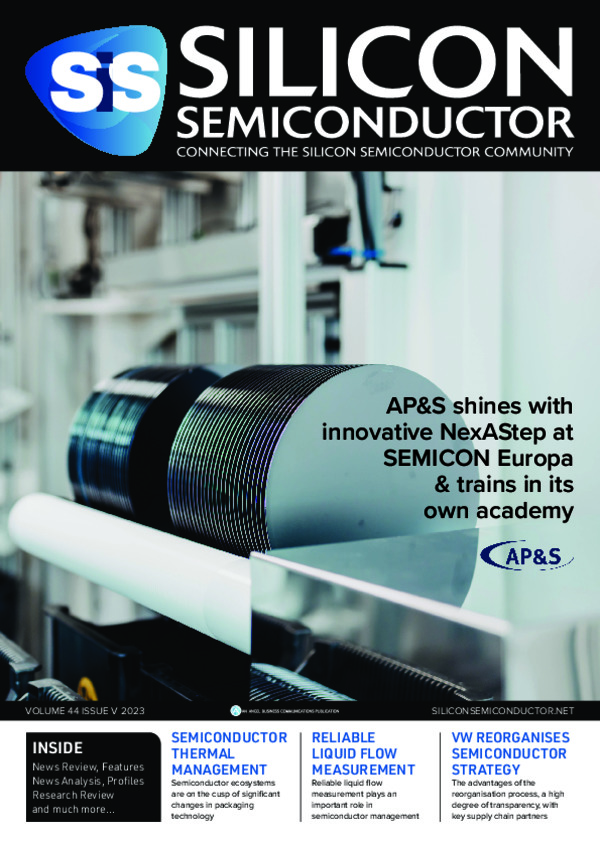
Efficient semiconductor thermal management
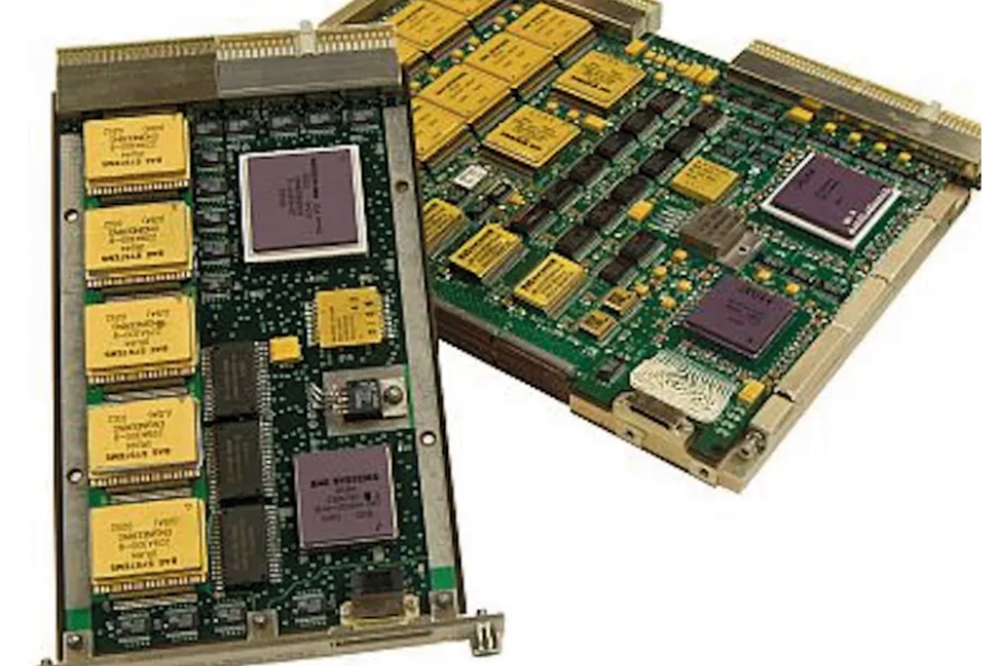
There is growing consensus in the semiconductor ecosystem that we are on
the cusp of significant changes in packaging technology. Evolving
semiconductor technologies are driven by new applications. These new
technologies call for semiconductor materials that are highly efficient,
smaller in size and highly reliable, with longer field life cycles and
the ability to operate across all climate conditions.
BY RAMESH KOTHANDAPANI, TECHNICAL DIRECTOR, MICROELECTRONIC PACKAGING, MATERION CORPORATION
Eletronics components have necessarily evolved since the late 1990s, yielding complex and compact designs with efficient performance for their intended applications. Companies are engaging in more research activities to develop new alloys and composite materials, ways to prolong the life of semiconductors, and suitable environments for semiconductor performance. Industry is capturing these developments in the technology roadmap.
Modern electronics pose several challenges during the design stage. One example is space constraints, which relate to the microelectronic packaging design process. The number of electrical connectors, the material selected, electrical resistances, weight and cost are just some of the factors that drive new technology.
Many devices within a microelectronic package may be operating simultaneously, which leads to thermal accumulation. This collected thermal energy or heat cause the semiconductor to perform inefficiently, or even to malfunction. Thermal energy is a constant threat to semiconductors, especially in critical applications. In past years, fins and cooling fans were often the first line of defense against high temperatures.
Today, advanced thermal interface materials with special features – such as wavy 3D surfaces, smaller heat sinks and unique enclosure designs – are playing a greater role in thermal management for advanced electronics.
Following is a partial list of sectors or industries in which advanced thermal management materials are required for reliable operation:
Telecommunications devices risk poor signal management and decreased efficiency without proper thermal management.
Space: Understandably, the space sector has no room for failure. The technology road map for space must support planetary exploration, space tourism, space mineral mining for new materials and probes and vehicles to travel vast distances. Semiconductor material used here must be able to tolerate harsh environmental challenges while performing critical operations.
Aerospace, low-altitude mobility: There can also be no failure with any type of flying vehicle. From passenger planes to war planes and even forthcoming low-altitude flying taxis, efficient electronics will be required for maximum performance. A future human-transporting drone must be equipped with sophisticated semiconductor chips. These chips must support uninterrupted communications, air current sensing and emergency landing. Thermal management is crucial to these semiconductors.
Uninterrupted communications: Smoother communication is always expected despite various types of noise and disturbances. The electronics and their respective packaging must enable the semiconductor to serve its designed function.
Radio wave-based telecommunications: Base station systems contain semiconductor devices operating within a multitude of different environmental conditions. They experience constant thermal management issues that can lead to interruption of communications. Inefficient electronics causes poor signal management and the need for frequent maintenance. The evolution of telecommunications has now reached its fifth generation, with ongoing changes in design and device size. Each generation demands incrementally better thermal management of electronic packaging. Microelectronics are especially challenging in this regard, as these semiconductors experience enormous loads that require efficient thermal management material. From military communication and airliners to consumer mobile devices and smart home and office systems, these applications all require the highest-quality communication.
Automobiles and autonomous travel: Increasingly, automobiles are combining telecommunication electronics with safety and optical sensing devices. Environmental concerns over the use of petroleum products have led to the development of temporary energy storage or battery products. Efficiently managing power adds a layer of design complexity, with additional electronic modules being integrated into a single semiconductor. As multiple applications operate simultaneously, loads on these semiconductor units generate high levels of thermal energy. These batteries also charge and discharge frequently, putting a strain on the electronics governing their operation. Electric vehicles contain an estimated four to six times more electronic components than conventional vehicles.
Human-wearable systems with efficient heat management materials: Human-wearable devices are challenging as a result of their small size, safety requirements and weight. Much like battery-operated devices, they are prone to heat generation that must be highly managed through material selection.
Designers must balance the thermal conductivity and weight of materials used in their systems.
Again, these are only a few examples illustrating emerging thermal management demands on semiconductor materials. To date, silicon-based materials have been most widely used because of their efficient operation and wide availability. Silicon’s cost, integration into established design and process flow, and favorable chemical and electronic properties also contribute to its popularity for semiconductor applications.
In new devices bundling multiple applications, however, the question arises whether existing semiconductor materials can deliver needed output. Newly developed and enhanced materials are rapidly coming onto the scene. These include gallium nitride, gallium arsenide and silicon carbide, each of which has its own pros and cons as designers continually balance cost, weight and other factors in their material selection.
These designers must consider several factors, including the reality that the lower thermal conductivity of new materials often increases cost while traditional materials, which do not tend to enhance semiconductor efficiency, offer undeniable cost benefits.
As mentioned earlier, the electronic module has shrunk considerably and now contains many more components than it did previously. During operation, it is natural for these devices to generate heat that gets transferred to other assemblies. Bonding materials used to assemble the semiconductors are constantly challenged by poor heat transfer. If heat is not transferred quickly, the semiconductor cannot perform its role efficiently, leading to device or system failures. In certain applications, high humidity combines with heat to create even more severe failures.
The effect of temperature on semiconductor efficiency is dependent on
the materials being employed and their specific physical properties.
An efficiently designed semiconductor electronic system requires a good thermal management material to dissipate heat. Frequency switching, voltage handling capabilities and operating temperature are important considerations for future semiconductor materials. Gallium nitride (GaN) placed on silicon and silicon carbide are examples of materials gradually replacing silicon for this purpose.
Thermal overstress is an important point to consider during the design stage. A good electronic design team will consider the thermal transfer processes that add weight to the design and enlarge electronic architectures accordingly. Design teams should introduce longer-term reliability test simulations and good bonding materials that are able to tolerate high levels of heat.
Figure 4 clearly illustrates the effect of temperature on semiconductor efficiency. The standard GaN on Si measures 189 degrees Celsius with 1% of the active device on silicon. The undesired heat transfer will be passed onto semiconductor bonding materials – which could be any eutectic die bond material or solders – causing a catastrophic failure over time. GaN on SiC is significantly better, reducing heat by more than 50% to 77 degrees Celsius. The illustration of GaN on diamond refers to a diamond composite material that manages the heat transfer process extremely well. It yields a reduction of about 50% compared with GaN on SiC and four times lower than GaN on Si.
Thermal conductivity of various materials, as measured in watts per meter Kelvin (W/mK).
Thermal transfer material selection is also crucial to packaging components. Silver particles and small diamond particles are combined to produce a diamond composite substrate that enables excellent heat transfer for any of the available semiconductor materials. In addition to the diamond composite, there are several other heat transfer materials from which to select. Thermal conductivity is measured in watts per meter Kelvin (W/mK). Materials with high thermal conductivity can transfer heat quickly, while materials with low thermal conductivity will insulate heat well. The larger the value, the better the performance. Not all materials with higher thermal conductivity values are useful substrate, however, because of the potential for greater expansion. One example is copper, which offers good thermal conductivity but also tends to expand significantly. Figure 5 illustrates thermal conductivity values for several materials. It is important to match this value with Figure 6 listing CTE values.
The coefficient of thermal expansion (CTE) is a measure of how much a material expands or contracts when its temperature changes from a colder zone to a hotter zone. It is usually expressed as a fractional change in length or volume per unit temperature change. Unlike TC, CTE values must be lower for efficient thermal management. Apart from TC and CTE, inefficient heat transfer must be managed well with an appropriate material to dissipate heat. The illustration below is an example of the next-generation Laterally Diffused Metal Oxide (LDMOS) RF device GenPack®, which is constructed with a base capable of efficiently dissipating heat. An interface material with foil contacts could be added to enhance thermal transfer even further. These thin foils (MiM) offer more contacts to connect the base and substrates.
Coefficient of thermal expansion (CTE) for various materials (in ppm/K).
Selecting semiconductor attachment or bonding material is also very important. The semiconductor or die is usually attached to its base using epoxies with higher melting temperatures that require curing before final hermetic or semi-hermetic packaging. Eutectic die attach solder materials such as gold-germanium (88Au/12Ge) alloy, which has a melting temperature of 361 degrees Celsius, or gold-tin alloy (80Au/20Sn), which has a melting temperature of 280 degrees Celsius, may also be considered. These are purely organic-free materials for the die bond process.
Conductive epoxies are very widely used for die attachment in silicon semiconductors. As mentioned, if these conductive epoxies contain organic material, it can lead to outgassing, which reduces die performance. Using gold-tin (80Au/20Sn) or gold-germanium (88Au/12Ge) as die attach materials eliminates organic content and reduces outgassing, thus enhancing the performance of the die. The package may then undergo hermetic sealing with either gold-tin or gold-germanium combined with a plated lid.
Exploded schematic view of the next-generation Laterally Diffused Metal Oxide (LDMOS) RF device GenPack®
Again, it’s important to emphasize that conductive epoxy-based die attach materials may release gases that become trapped during application and circulate within the hermetically sealed package. These gases are harmful to the semiconductor and can cause it to operate inefficiently. This leads to high heat generation, which in turn may cause further complications. Under these circumstances, additional materials (such as a getter material) must be included in the package to manage outgassing. Hermetic packaging with the Combo Lid® is a critical process step that prolongs the life of semiconductor materials in the package and facilitates operation free of environmental pollutants such as moisture or gases like hydrogen and oxygen.
Copper and molybdenum laminates are among the materials that lend themselves to efficient thermal management.
After the package is well sealed, units should be subjected to a series of reliability tests. Gross leak, fine leak, electrical performance, aging and other tests can confirm whether selected materials will truly enhance field performance. Electrical and temperature cycle assessments can be time consuming processes, so designers often employ accelerated tests that simulate the life of the package. Survival in these harsh test environments validates proper selection of materials for efficient thermal management. In summary, the following items should be considered during the electronic design stage:
1. TC and CTE values for various selected materials a. Higher TC and lower CTE values
2.Substrate or base material selection
a. Diamond composite
b. Copper-moly laminates
c. Copper-moly alloys
d. Silicon nitride substrates
e. Ceramic materials
f. Copper tungsten alloys
3. Die attach materials
a. Silver epoxy
b. AuGe
c. AuSn
4. Hermetic lids
a. Determine the seal cover
b. What solder type to be used?
5. Post-die attach process to cure epoxies
a. Curing temperature
b. Any test to confirm effectiveness?
6. Outgassing
a. Source of gases
b. Containing them
c. Correlate with electrical tests
7. Post-packaging reliability tests
a. Gross leak (nondestructive)
b. Fine leak (nondestructive)
c. Temperature cycle tests (destructive)
d. Electrical test (nondestructive)
8. Thermal interface materials
a. Silver preforms with 3D surfaces for higher
surface contacts
b. Indium-based materials
Material selection and package design are both vital in creating reliable systems. It’s also important to develop a plan to handle mass production. Cost roadmaps and manufacturing processes are reviewed in parallel at an early stage. Materials with affordable CTE and TC values may offer high levels of performance for specific applications. Adding special layers of materials with VIAS and pedestal mimics high-end packaging. The point, of course, is to prepare for volume production with a highly developed process.
Schematic view of thermally managed package for a GaN semiconductor device.
Thermal expansion plays an increasingly important role in newer applications. The evolving challenge is to combine different materials to form a consolidated package housing. Many materials exhibit promising thermal management properties that put them on the designer’s short list. Additional features could be added to materials to enhance operation. For example, improved heat dissipation can be achieved through braze alloys or copper.
Over time, this process will be explored in both organic and various amorphous materials such as glass substrates. Such materials may serve as both heat absorbers and as substrates for multiple chips. As substrates, they could be further enhanced with thermal interface materials to yield a larger contact area. The thermal interface material also contributes to greater electrical contact.