Wisconsin Oven ships horizontal quench systems
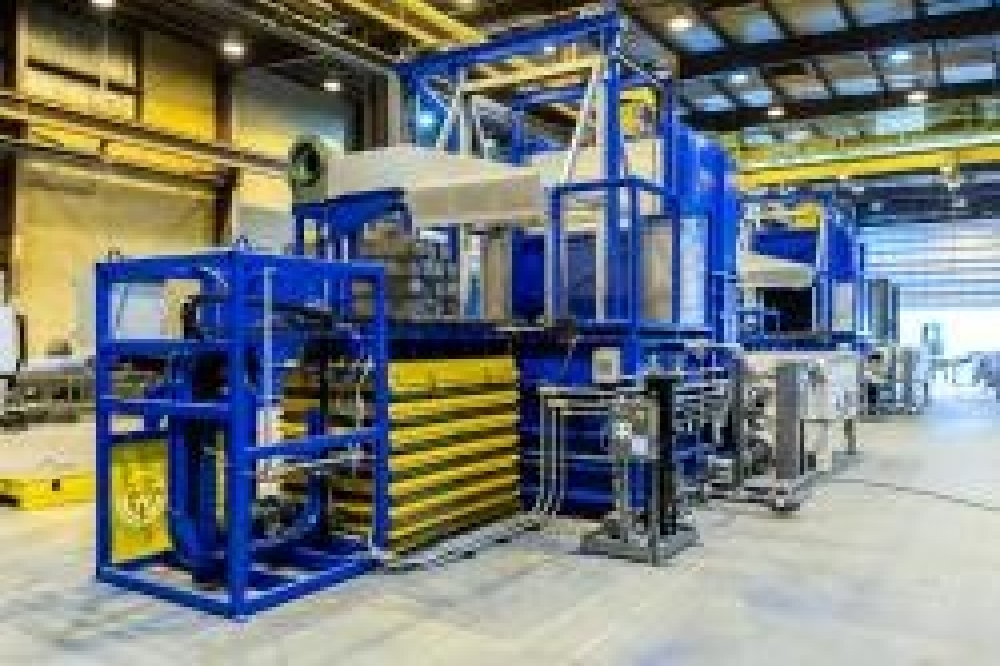
Wisconsin Oven has shipped two Electrically Heated Horizontal Quench Systems to the Semiconductor industry.
The systems will be used for the annealing and rapid cooling of various high purity alloy parts.
The operating procedure for each horizontal quench system includes loading the product on a work grid located on the loading platform. Once the load is lifted into place, a pusher/extractor mechanism located at the front of the quench tank moves the load onto the quench lift platform, then the furnace pusher/extractor mechanism pulls the load into the furnace for annealing. After completing the heating cycle, the vertical lift door opens, the furnace pusher/extractor transfers the load onto the quench lift platform, and the load is lowered into the water quench tank. After the load has sufficiently cooled, the quench lift is raised, and the front mounted pusher/extractor mechanism pulls the load back onto the scissor lift. While the load is pulled onto the scissor lift, a blow off system removes the majority of the water from the load. Click on this link to watch a video of this system in operation.
Each horizontal quench furnace has a maximum temperature of 1,250°F, and capacity to heat and support a 4,500 pound gross load. This type of equipment routinely achieves temperature uniformity of +/-10°F. This customer requested a uniformity tolerance of ±20°F performed at 500°F, 900°F, and 1200°F. The uniformity was documented for each system with a nine (9) point profile test conducted in an empty oven chamber under static operating conditions.
“At Wisconsin Oven, we work closely with customers to find the right solution for their specific process. This customer sought to make their previous manual quenching process more efficient and increase production capability, while providing a safer work environment for their operators- we exceeded their expectations on all three requests with these systems.”
– Doug Christiansen, Senior Application Engineer
Unique features of these horizontal quench furnaces include:
• Two (2) separate powered pusher/extractors; one for charging the load onto and off of the quench tank lift, and the other for pulling the load into the furnace and pushing the load out onto the quench lift
• Hydraulically actuated scissor lift load table
• Guaranteed temperature uniformity of +/-20°F at 500°F, 900°F, and 1200°F
• 15,000 CFM @ 15 HP plug-mounted recirculation blower
• Furnace and sequence control performed by PLC with 10” Color HMI located in an articulating arm (to allow best field of view for operators)
• Programmable temperature controller with Ethernet capabilities
• High limit instruments provided for product and furnace over temperature protection
• Combination style airflow to maximize heating rates
• Hydraulically actuated quench lift mechanism
• Blow off system to remove the majority of water from the load after the cooling/quenching process (to minimize water spilling onto the floor around operators)
• UPS battery backup system included for PLC and controls
• Remote manual lubrication lines for roof mounted bearings (located at operator level for ease of maintenance)
• Chiller system to cool the quench tank water between load quenches