The complexities of onshoring chip production amidst geopolitical risks
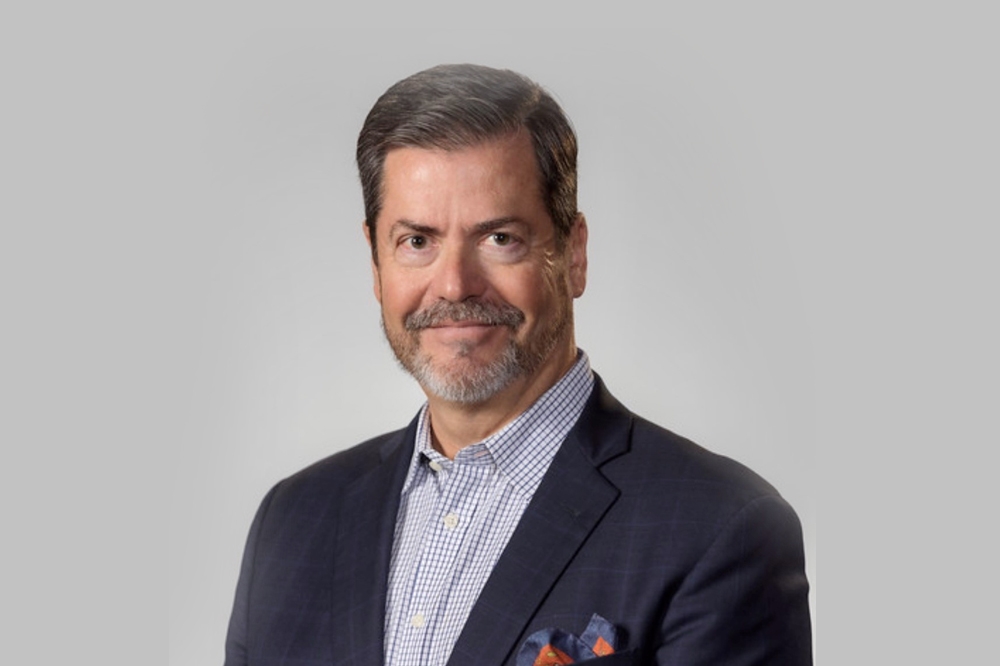
Recent developments, including the Covid-19 pandemic and catastrophic events like freezes and fires, have shed light on the disruptions caused by chip shortages and related supply chain issues. Moreover, the uncertainty created by rising geopolitical tensions has awakened the sector to impacts that exceed the balance sheet of any one firm. By George Haitsch, who leads the North American Tech + Media + Telecom Division for WTW.
Now semiconductor production and distribution are deemed critical infrastructure around the world. As public, political, and academic awareness grows, governments, the industry and end customers are exploring options to secure production from sand to chip.
In response, governments are incentivizing onshoring through policy initiatives. Significant investments are being catalyzed by legislative acts such as the US Chips and Science Act, the EU Chips Acts and China’s Integrated Circuit Industry Investment Fund. These initiatives are motivating businesses to establish new production facilities and enhance national self-sufficiency.
These efforts, aimed at bolstering national resilience against future crises, are strategically redefining global semiconductor hubs. This geographic reset will undoubtedly further disrupt the collaborative balance that has supported the industry, which has grown through a distributed supply chain business model.
What are the primary complexities?
• The semiconductor industry is truly a global ecosystem: Chip production involves multiple companies across the world - each specializing in one or more steps of the process that has created resilience and efficiency.
Technology and market trends have concentrated cutting-edge manufacturing and testing capabilities among a handful of global hotspots, including China, U.S., South Korea, Japan, Malaysia, Philippines and, most importantly, Taiwan. However, none are independent enough to sustain the whole supply chain on its own.
• Geographic centres of excellence: The U.S. currently enjoys an advantage in manufacturing capacity in areas such as intellectual property, chip design, manufacturing, and non-wafer materials. China is the key supplier of raw materials including the silicon needed for manufacturing. In areas like contract manufacturing, all are heavily dependent on Taiwan, South Korea, and Japan. Contract manufacturers, in turn, require capital equipment from a short list, the most prominent of which is located in The Netherlands.
The current trend of onshoring isn’t inexpensive or quick. Industry estimates suggest each chip factory takes a minimum of $10 billion and five years to build, from breaking ground to production of chips.
• Intellectual capital and labor are essential: While investment in new manufacturing fabrication plants is welcomed, its impact will be limited if steps are not taken to address labor shortages in an industry requiring technical expertise. Estimates in the U.S. suggest that companies across industries will face a shortfall of 300,000 engineers and 90,000 skilled technicians by 2030.
Amid intense competition, it is harder to attract and retain personnel. As semiconductors become ever more critical to product differentiation, some electronics and automotive manufacturers beginning to move chip design in-house. This is increasing competition for scarce talent and could undermine expansion plans. Additionally, chip design is becoming more complex due to the requirements of Artificial Intelligence (AI) with demand increasing for the latest and smaller chips requiring more complicated manufacturing processes.
• Supply and demand changes: In our discussions with industry leaders, we’ve learned that their concerns extend beyond current demand to potential future risks. A key question they face is; if they invest in capacity to meet shortages today, will they be selling into a glut tomorrow? While the latter is a longstanding risk for a cyclical industry, today’s supply shortfall, and the high costs needed to address it, make it imperative to chart a careful course. To mitigate this, several companies have been looking at new ways to manage product supply, including additional storage of components, raw materials and staged supply. Many companies are also re-tooling older technology / equipment for a quicker response.
Preparing for Geopolitical Complexities:
Governments and businesses must prepare for multiple scenarios by:
• Reviewing risk registers and factoring in longer time horizons to challenge assumptions around likelihood and impacts.
• Considering executive team scenario planning, preparing leadership to respond.
• Ensuring a global perspective when considering business resilience. Working closely with suppliers will help companies understand and address supply chains risk better. Leveraging diagnostic mapping, monitoring tools and analytics to visualize, quantify, and assess risks in specific locations.
• Reviewing insurance provisions to understand exactly what is and isn’t covered addressing gaps ahead of potential losses.
After several challenging years, semiconductor companies recognize the need to mitigate risks related to geopolitical and natural catastrophe exposures. Evolving to address a volatile environment, it is important to consider a wide range of strategies to avoid potential pitfalls. Partnering with experienced, strategic risk brokers and having access to cutting-edge analytical tools will help accurately assess risks and create winning solutions.