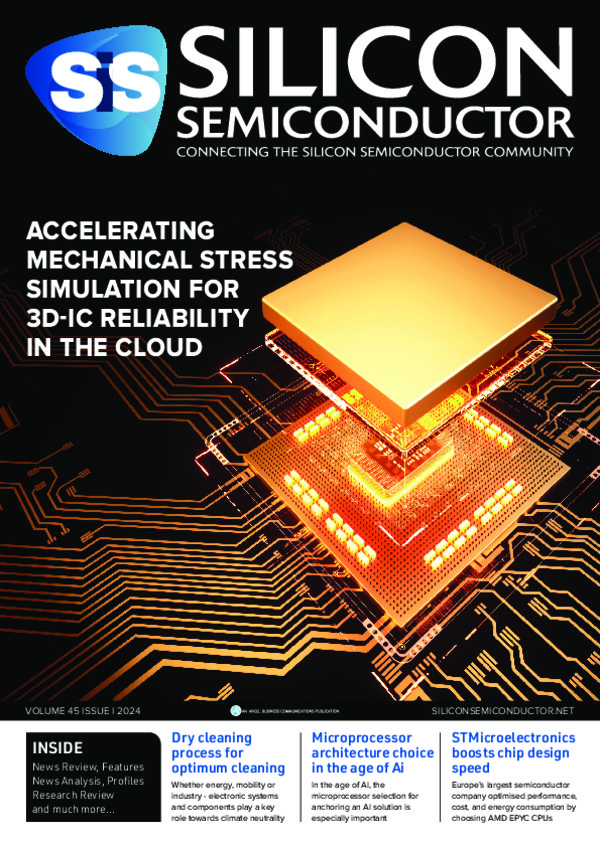
Filling the metrology void
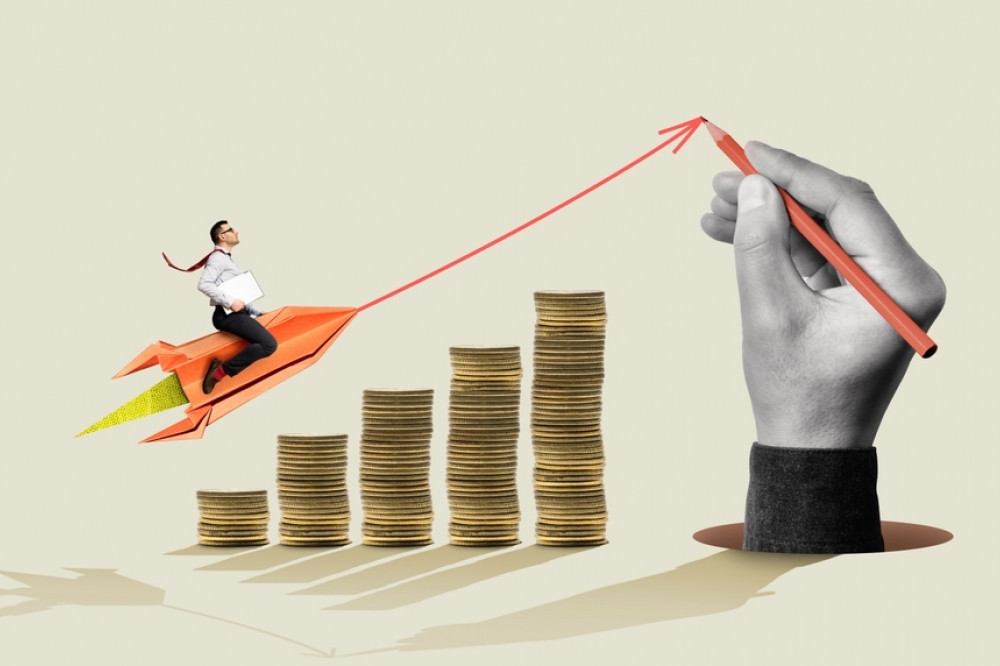
Nearfield Instruments B.V. recently launched AUDIRA – said to be the
industry’s first and only in-line, non-destructive subsurface metrology
system for advanced semiconductor manufacturing.
By Niranjan Saikumar; Co-authors: Nelda Antonovaité, Irene Battisti, Taras Piskunov, Mehdi Soozande
THE AUDIRA SYSTEM is aimed at providing highly accurate and precise nanometer-level measurements of buried features and defects, such as voids, in advanced memory and logic devices. With AUDIRA, Nearfield Instruments targets the introduction of complementary subsurface process control measurements to transmission electron microscopy (TEM) and critical dimension-scanning electron microscopy (CD-SEM).
Nearfield Instruments’ proven in-line surface metrology solution, QUADRA, features an innovative architecture based on multi miniaturized atomic force microscopes (termed MAFM), enabling high-speed, non-destructive, on-device topography measurements. The very high speed MAFM head technology combined with the multi MAFM approach that allows for parallel imaging across the wafer results in throughputs more than 100x higher than existing state-of-the-art automated AFM systems, enabling the use of QUADRA as in-line tool in HVM fabs. QUADRA’s unique architecture also ensures excellent precision and dynamic stability during measurements of CMP application layers as well as high-aspect ratio (HAR) structures and high-NA EUV (Numerical aperture Extreme Ultra Violet) applications. The proprietary advanced imaging mode uniquely places QUADRA as the only AFM tool capable of 3D measurements of critical HAR structures. Coupled with custom CD extraction algorithms and tip wear detection mechanisms for automatic probe exchange, QUADRA provides excellent in-line process monitoring capabilities for CMP process as needed with hybrid bonding, HAR structures after etching and EUV resist CD metrology.
The AUDIRA subsurface metrology tool will be based on the QUADRA architecture retaining the benefits of a unique multi-MAFM system architecture and the proprietary atomic force microscopy (AFM) technology aimed at high-throughput for in-line process control. In AUDIRA, Nearfield Instruments introduces two new acoustic microscopy techniques addressing the need for subsurface metrology at two different depth ranges. With both technologies, the AFM probe is used as a waveguide for sending and then “listening” to sound waves from the wafer layers.
Applications
AUDIRA is targeting both the metrology and inspection markets specifically for measuring nanometer-range subsurface structures through opaque layers.
For metrology, the principal application is overlay accuracy, which is the misalignment of patterns on different layers. Currently, many traditional optical overlay metrology techniques are limited to measuring large optical targets that are ten times larger than the dimensions of the device itself.
For the 5 nm node, the overlay tolerance is in the order of a few nm, with most leading memory and logic manufacturers achieving overlay in the order of 2 nm, and expected to shrink further. With shrinking dimensions, direct on-device overlay measurements will be required to remove the possible error from metrology to the device (MTD) calibration and guarantee the performance of the device.
The need for an on-device overlay metrology solution is also driven by the increasing stochastics effects in the EUV lithography process due to interaction between EUV light and resist. Stochastic effects lead to increased CD non-uniformity (line-edge and line-width roughness) which eats up a significant part of edge placement error (EPE), which is below 5 nm for the 5 nm node, leaving even less budget for overlay error.
This strict overlay control places a challenge to the accuracy and precision of metrology tools into sub-nanometer range. While e-beam imaging can detect very local on-product alignment errors, including stochastics, it has limited penetration depth and is damaging to sensitive photoresists, limiting its applications. Furthermore, the memory market shows an increase in overlay metrology after etching while logic customers choose after development inspection due to large variation of feature dimensions, which points to the need for diverse overlay metrology capabilities. For example, multi-layer measurements are required both for transparent as well as opaque layers.
The inspection and review market application target for AUDIRA is primarily, but not limited to voids. Void formation in layers can be tracked at the device level to at least one critical process where the sacrificial silicon nitride is removed and replaced with conductive metal resulting in shallow voids buried 10s to 100s of nm deep.
While this issue is particularly exacerbated in 3D NAND structures with the trend towards densely packed large holes with reduced hole-spacing, this is also seen with interconnects due to the scaling down of metal line cross-sections. The increased current density due to scaling is further stressed in the presence of voids and can lead to device failure.
At the wafer/die level during advanced packaging step using hybrid bonding, surface defects on the Cu pad can create a void as large as 10 times the defect size after the bonding step with these large voids buried microns deep below opaque layers. With the size of the Cu pads shrinking to well below a micron and dense Cu pads for bonding moving towards the norm, defect sensitivity with resolution of 100s of nm or better is needed.
Defects in bonding material/process can also lead to a different type of defect which is delamination. While this is seen with hybrid bonding at the wafer level, with the device fabrication roadmap leading to 2D FET, delamination of the channel layer is a major concern for yield at the device level. In both cases, these defects result in electrical or mechanical failures.
Measurement technology
AUDIRA brings forth two different complementary subsurface metrology technologies, where comparatively the trade-off is on the side of penetration depth of imaging and lateral resolution capability. From a technical standpoint, the two technologies differ in terms of the acoustic frequency range of operation and the underlying physics used in the measurement with frequencies in the MHz range used to measure shallow structures going up to 10um in depth based on the difference in the material properties, and GHz range used to measure deeper structures or structures with comparable material properties buried shallow below the surface.
Sensing viscoelastic variations
The first technology is based on sensing the viscoelastic variations of the materials, and it is suited for measuring shallow and fine features or relatively large features buried deep going down to a few ums. Lateral resolution of nm or sub-nm level can be obtained depending on the application. Every material shows a characteristic resonance frequency when sensed by a scanning probe, referred to as contact resonance (CR) (See Figure 1). The change in contact resonance can also be caused by material changes buried under the surface, like in the case of voids/delaminations or subsurface alignment markers (See Figure 2).
In literature, CR-AFM for both surface characterization as well as subsurface imaging is typically being done with the source of the acoustic wave and the sensing of the CR being separated. The acoustic wave is generally applied at the bottom of the wafer transferring acoustic energy to the full wafer, while the scanning probe on the top senses the CR at specific locations. In AUDIRA, a shift from the traditional way of working is modified by combining source and detection at the probe. The probe is used as a waveguide to introduce acoustic waves at the carrier frequency fc in MHz range which is then modulated at a frequency fm. The nonlinear tip-wafer interaction causes a downmixed signal at fm which is amplified by the cantilever response. This is used to detect the CR changes with this measurement mode referred to as Subsurface ultrasonic resonance force microscopy (SSURFM).
The penetration depth in terms of sensitivity is determined by the feature size as well as the mechanical stiffness variation of the different materials involved. AUDIRA innovates this technique further by enhancing the resolution and the sensitivity to buried material through custom cantilever and tip designs aimed at subsurface measurements.
Wave propagation scheme
The sensitivity of the viscoelastic variation sensing drops with depth: at depths larger than 10um, it can only detect large features with significant material property variation. To address the needs at depths larger than 10um, the second technology employed by AUDIRA utilizes injection of acoustic waves in the order of GHz where the target resolution is in the range of a few nm or tens of nm depending on the target depth.
The physics utilized with this technology shifts to a wave propagation scheme wherein the transmitted wave interacts with the wafer at all the surface transitions within the device and reflects back. This reflected acoustic wave contains information linked to the strength and time of arrival which is then used to reconstruct the 3D subsurface structure image.
Two primary technology directions are considered for imaging using this scheme: the Piezoelectric Transducer (PZT) approach and Photothermal Acoustic Imaging (PTAI) with AUDIRA capable of accommodating both within the same architecture. In the PZT technique, advanced electronics are utilized to efficiently launch and detect GHz acoustic waves. The rapid switching between emission and detection enabled by these electronics allows precise control of the acoustic wavelength. This level of control plays a pivotal role in determining both the depth resolution and the signal-to-noise ratio of the measurements.
In the PTAI method ultrashort laser pulses are used to initiate acoustic waves, detect the reflections, and reconstruct acoustic echoes, operating within a pump-probe scheme. Unlike the PZT technique, PTAI places less stringent demands on the electronics component. However, while PTAI offers the advantage of simplified electronics, the echoes it reconstructs are inherently indirect measurements when compared to the direct measurements achievable through the PZT method.
The sample is scanned using an ultrasound piezoelectric transducer (in PZT technique) or using an ultrashort laser pulse (in pump-probe PTAI method). Ultrasound waves generated at the surface of the sample propagate through its depth, reflect on the buried structures, and create mechanical deformation of the surface which is registered as an ultrasound echo. The array of echoes is processed to reconstruct the buried structure. 2D scan of the surface allows to generate a full 3D image of the subsurface, which can be used to generate different cross-sections, for example the B-scan (side-view of the sample) shown on the top-right image.
From an application perspective, the two technologies provide a trade-off in the penetration depth due to the acoustic frequency that can be employed as the depth is directly dependent on the wavelength of the acoustic excitation. The PZT technique is limited by the thickness of the piezo material which can be consistently fabricated translating to lower frequencies in the range of a few GHz going up to 10 GHz, while PTAI can act as a high frequency source going all the way up to 100 GHz.
Signal processing plays a vital role to obtain a comprehensive reconstruction of the full 3D structures for both the techniques. AUDIRA deploys a customized ultrasound beamforming technique (See figure 4). Such technique is a well-known post-processing approach used in non-destructive inspections. This method involves processing the array of echoes collected by the scanning probe during the imaging, mimicking acoustic lenses used for focusing ultrasonic beams at a point of a solid object or structure. This processing forms the backbone of the method’s ability to produce high-fidelity representations of subsurface features and enables the extraction of detailed structural information.
Image Processing in AUDIRA
Nearfield Instruments recognizes the critical role played by data processing algorithms linked either to overlay extraction or defect identification. For overlay extraction, while existing algorithms for optical techniques are applicable to some extent, the unique per pixel capture of information requires special attention. To this end, Nearfield Instruments with AUDIRA also introduces custom algorithms aimed at enhancing the contrast of subsurface images and importantly improving the accuracy of the extracted overlay. Additionally, since overlay extraction through multiple opaque layers with their own respective alignment markers is needed, algorithms for resolving interfering structures and simultaneous overlay extraction are employed.
Nearfield Instruments is also working with customers for alignment markers customized for AUDIRA based measurement with a view towards improving throughput and precision.
On the side of defect identification and classification, Nearfield Instruments is developing traditional algorithms, but is also in addition to traditional methods has been developing machine learning based classification algorithms which can be deployed in the fab. The machine learning route is especially needed for defect detection after hybrid bonding since the back-end process with wafer-edge trimming, wafer grinding and dicing creates artifacts related to the surface roughness and also renders low contrast images.
Platform and link to M&I roadmap
Nearfield Instruments works with customers to develop a recipe and choosing for which applications local elasticity measurements are best, and when to switch to wave propagation schemes. With both MHz viscoelastic sensing and GHz ultrasound imaging technologies, the AFM head scans across the die by capturing information from the wafer with as small as a tenth of a nanometre step. The data captured at each step is then combined and translated into a comprehensive pattern of the underlying layers.
The elasticity and wave propagation schemes have been developed so far mainly through the transmission of the acoustic waves from the bottom of the sample for the former and from the top for latter. This is severely restricting in capabilities and does not allow a single tool to handle both modalities. The bottom actuated approach for elasticity is also possible for small samples and practically impossible for large samples like a 300 mm wafer. Nearfield Instruments has been successfully able to combine these technologies to allow for the scan head to use the AFM probe as the waveguide for the acoustic waves.
As a result, AUDIRA can utilize the proven multi-head architecture of QUADRA enabling faster adaptation in the fab. The multi-head architecture allows for AUDIRA to be simultaneously used for measuring at different depths on a wafer and additionally work as a defect inspection and review tool with different scan heads performing different functions. Enabling such a functionality in the scan head allows AUDIRA to function as a hybrid metrology tool in the fab and is a critical breakthrough.