Optimising predictive maintenance
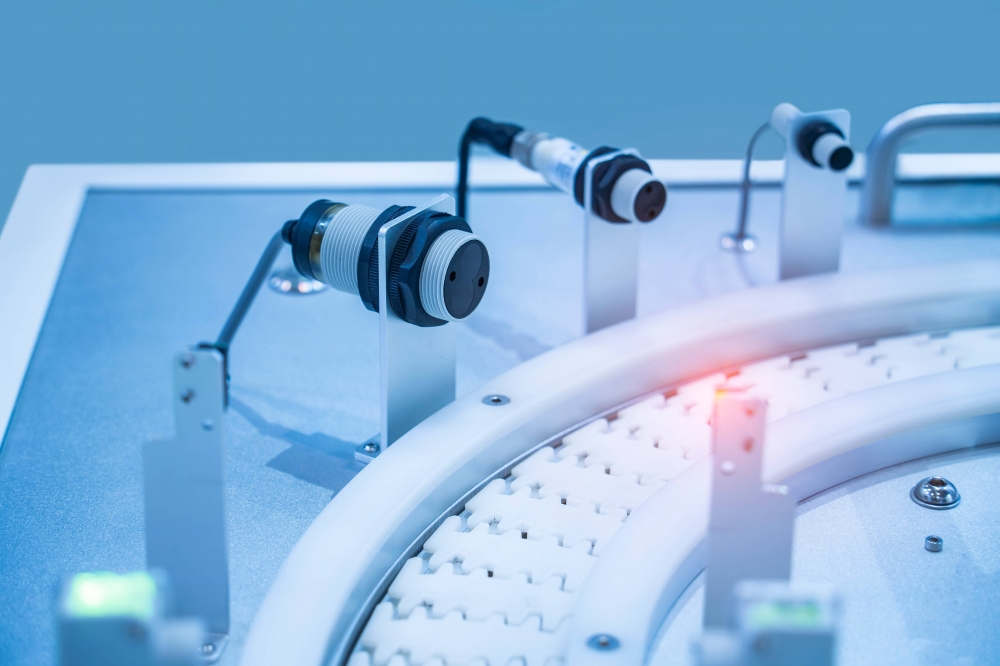
The benefits of predictive maintenance (PdM) are already well established. Improved productivity, lowered maintenance cost and a reduction in unplanned downtime by up to 50 per cent are just a few of the advantages offered. But how do you achieve a truly optimised sensor system? Here, Ross Turnbull, Director of Business Development and Product Engineering at ASIC design and supply company Swindon Silicon Systems explains.
Most predictive maintenance systems are fairly simple in construction. The data collection is performed by one or more smart sensors, placed strategically throughout the plant to gather data on individual machinery or processes. The sensors then communicate this data to a central control system for analysis by specialist software, to quickly find potential issues and identify actionable insights before problems have chance to occur.
Sensor selection
To make the most out of a predictive maintenance system, we need to begin with the initial collected data. Choosing the right sensor type for the application in ensuring that faults are picked up quickly and accurately, with ample notice given for proper repair.
One common choice of sensor for PdM applications is the accelerometer. Able to determine acceleration in one or more axes, these sensors can provide tilt and inclination measurements as well as impact recognition functionalities. Conversion of the acceleration data into vibrational information offers additional insights — in fact, vibration changes are often considered as one of the earliest indicators of a potential fault.
By comparing near real-time vibrational information with historical data, it’s easy for the sensor system to identify a potential issue and flag it up for investigation. This, combined with the relative low cost and compact size of a MEMS accelerometer, makes it an ideal choice for PdM systems.
But there are times when a vibration sensor alone may be unable to register the fault. In this case, it may be preferable to use another sensor type, either in conjunction with an accelerometer or as a complete replacement.
Temperature sensors, for example, could be an appropriate sensor type to use to detect any temperature changes — typically an increase — caused by excessive loads or start/stop procedures. Where bearings have become worn or damaged, friction is likely to increase, which again can cause a detectable temperature change. Left unchecked, this can cause additional damage to equipment and can lead to more inefficient processes.
Optimising electronics
Once a suitable sensor type has been selected, there’s still more than can be done to deliver a sensing system that is truly a cut above the competition. This can be done through the optimisation of the electronics at the very core of the sensor.
Many traditional sensor types will collect analogue values. Before these can be communicated to other equipment in the sensor system for analysis, they must first be converted into a compatible digital format. These processes of signal conversion and communication may be performed by one or more standard ICs. But what if your require a more optimised predictive maintenance sensor?
Manufacturers should instead look to an application specific IC, or ASIC. This chip has been designed exclusively for an individual customer or application, allowing it to offer far more functionality than a standard off-the-shelf chip.
Within the predictive maintenance context, this could look like a chip with sensor-specific processes and conditioning, allowing for more accurate signal conversion with reduced noise. And the flexibility of custom design allows for the removal of additional unneeded components, allowing for investment into performance where it matters. As a result, the ASIC can offer more precise sensor data, often within a smaller footprint.
As the manufacturing industry seeks to implement more advanced technologies, it’s crucial that sensor technology continues to evolve. Optimising sensor systems right from chip level guarantees a predictive maintenance system that offers the very latest in sensing capabilities, and its users with all the benefits of a more efficient, proactive maintenance system.