
High-speed, high-temperature pumps address the challenges of advanced ALD processes
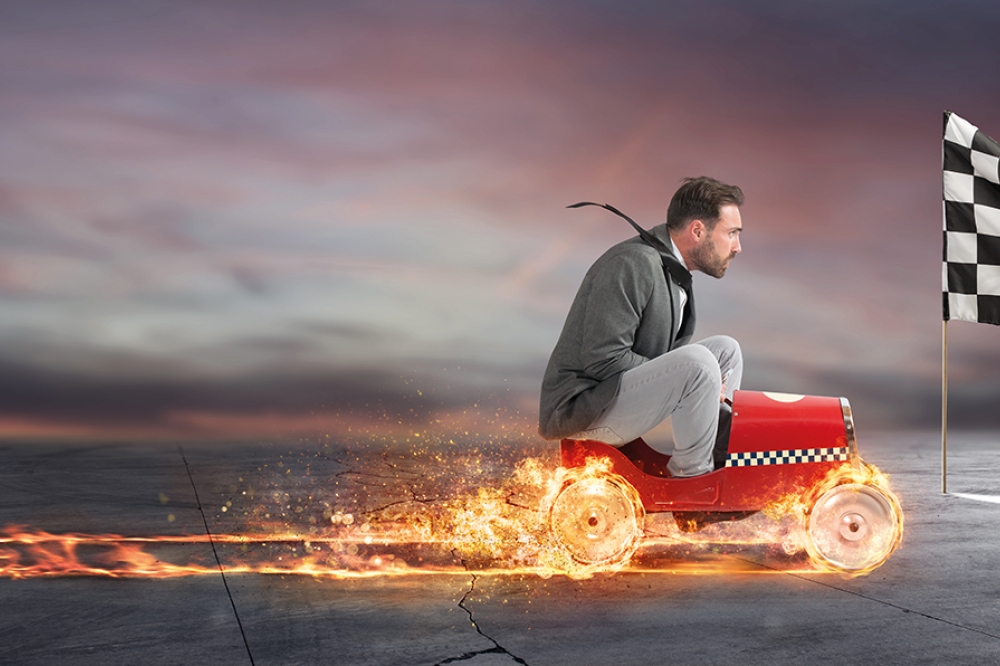
Addressing the potential problems of pump failure, process downtime and slow processing speeds when it comes to atomic layer deposition.
By Allister Watson and Young Chung, Edwards Vacuum
Semiconductor device designs are going vertical. Some of the most exciting new devices use many-layered film stacks and incorporate high aspect-ratio (HAR) features that are themselves complex multilayered structures deposited with atomic layer deposition (ALD) processes. Some ALD processes generate condensable by-products that can accumulate in vacuum pumps.
If not addressed, the deposits can lead to pump failure and process downtime. Even when managed appropriately, these accumulations require periodic maintenance that increases cost-of-ownership and reduces productivity. While ALD is exquisitely precise, it is also inherently slow, limited to a large extent by the vacuum system’s ability to cycle between precursor and reactant gases in the process chamber. Together, these considerations are driving the development of higher temperature, higher speed pumps to extend maintenance intervals and shorten ALD process cycles.
Figure 1: The tube-shaped capacitors comprise concentric cylindrical TiN plates separated by dielectric materials. ALD of TiN from TiCl4 creates NH4Cl, a condensable by-product. TiCl4 flows will increase as the capacitors grow taller and narrower. Reference: Threshold.
HAR structures
HAR features are becoming more common, and their aspect-ratios continue to increase. In some cases, such as the capacitors in DRAM, the increasing ratio results from pressure to pack more capacitors within a given footprint. In other cases, the pressure is in the vertical direction, as in 3D NAND, where increasing memory capacity means more layers and longer channels. In both cases, tall, narrow, cylindrical cavities etched in the substrate are filled by concentric layers of various materials to create the functioning device.
ALD processes
Most conventional deposition processes were developed to deposit uniform films over shallow features. The processes are relatively fast, and the deposition continues as long as the surface is exposed to the process.
The thickness of the film is thus a function of the time the deposition time. These processes are not good at maintaining uniformly thick films in the presence of significant topography, especially the extreme topography of HAR features where the deposition process has restricted access to the internal vertical walls and deeply recessed bottoms of the features.
ALD offers an elegant solution for depositing highly conformal, precisely controlled thin films on complex, deeply recessed surfaces. The deposits accumulate one atomic layer at a time as the surface is exposed to a repeating cycle of precursor and reactant gases. In the first phase, the precursor reacts with specific sites on the surface.
The reaction is self-limiting – once all sites have been occupied by a precursor molecule, the reaction stops. Next, the precursor gas is removed, and a reactant gas is introduced. The reactant interacts with the previously deposited precursor, again in a self-limited way, to complete the deposition and recreate the original surface chemistry. The newly deposited monolayer is ready for another ALD cycle.
Because both reactions are self-limiting, film thickness is a function of the number of cycles, not exposure time. This gives process engineers the luxury of allowing each cycle of the process to continue as long as needed to be sure all surfaces are completely and uniformly covered.
The biggest drawback of ALD is its slow speed. It is best suited to the deposition of very thin films that require fewer deposition cycles. Wafer throughput is determined primarily by the time it takes to remove one gas from the process chamber and replace it with the other, which puts a premium on high pumping speed in the vacuum system.
Condensable Process Gases and By-Products
Some process gases and by-products condense on cooler surfaces. In extreme cases, accumulations can completely block vacuum lines and cause pumps to seize. Avoiding unwanted deposition is most critical in the pump itself where rapidly rotating parts must maintain very tight mechanical tolerances. Condensation can be reduced or prevented by maintaining sufficiently high temperatures within the vacuum system. The challenge is best addressed by specially designed high-temperature pumps and by heating the foreline and exhaust line.
DRAM capacitors (Fig 1) are getting taller and thinner to increase their aerial density. The half-pitch of the capacitor array is projected to decrease by half over the next decade. Inside each capacitor, concentric tubular plates are separated by a complex structure of layered dielectric materials. ALD is essential for depositing the TiN electrodes of the capacitors. It is produced by the reaction of TiCl4 and NH3.
The reaction deposits TiN but generates NH4Cl, a condensable by-product. A carefully controlled, high-temperature profile throughout the vacuum system, but especially in the pump, reduces unwanted deposition and the risk of pump seizure. As aspect ratios increase, so will TiCl4 flows.
Figure 2. The number of layers in 3D NAND memory is predicted to double or more by 2031, requiring longer, higher aspect ratio channels. The ONON sandwich that lines each channel is deposited with ALD from HCDS. The nitride phase of the deposition creates condensable NH4Cl. The HCDS can also condense to a polymeric gel. (Source: Threshold Systems 2021)
Current generation 3D NAND devices have nearly 200 pairs of alternating oxide/nitride dielectric layers. Vertical memory strings are created along channels that penetrate these layers. The number of layers determines the number of memory cells along each channel and thus the memory density and capacity of the device.
The number of layers for multi-tiered devices will likely increase to 500 or more this decade. To create the memory cells, the channels are lined with an oxide/nitride (ONON) sandwich. The nitride layers become the charge traps that store information. The outermost oxide layer is needed to block a subsequent nitride etch that removes nitride from between the oxide layers of the original ONON stack.
ALD processes are used to deposit the ONON sandwich within the channels. Both the oxide (SiO2) and the nitride (SiN) are generated from hexachlorodisilane (HCDS). For nitride layers, HCDS + NH3 deposits SiN but also generates condensable NH4Cl as a by-product, requiring a hot pump to prevent unwanted condensation within the pump.
For oxide layers, HCDS + oxidant deposits the oxide without creating the NH4Cl by-product. However, the HCDS molecule itself may polymerize to form a condensable gel. Thus, a hot pump is needed to prevent NH4Cl in the nitride case and HCDS gel condensation in both cases. As the number of layers increases, so will the flows of HCDS and the need for hotter pumps.
The pump
Edwards’ latest generation of high-speed, high-temperature pump (iXH6520HTXS+) was developed in collaboration with major semiconductor equipment suppliers to address the challenges presented by advanced ALD process. It incorporates several new critical high-temperature technologies that allow it to operate at surface temperatures as high as 260°C. High-temperature operation reduces by-product condensation on critical pump surfaces, significantly extending recommended service intervals. Compared to its predecessor this new pump also benefits from a 30% increase in peak pumping speed, up to 96,000 l/min; a 34% lowering in power consumption; and better achievable ultimate vacuum pressure performance (important for high cleanliness between ALD steps).
For advanced ALD processes where condensable by-products are a concern then less frequent maintenance, faster process cycles, and lower power consumption can offer substantial bottom-line returns by lowering cost of ownership and increasing productivity.
Table 2. 3D NAND Layers, tiers and storage density will all increase substantially over the next ten years.
(Source: IRDS 2022)