42 Technology partners with INFICON
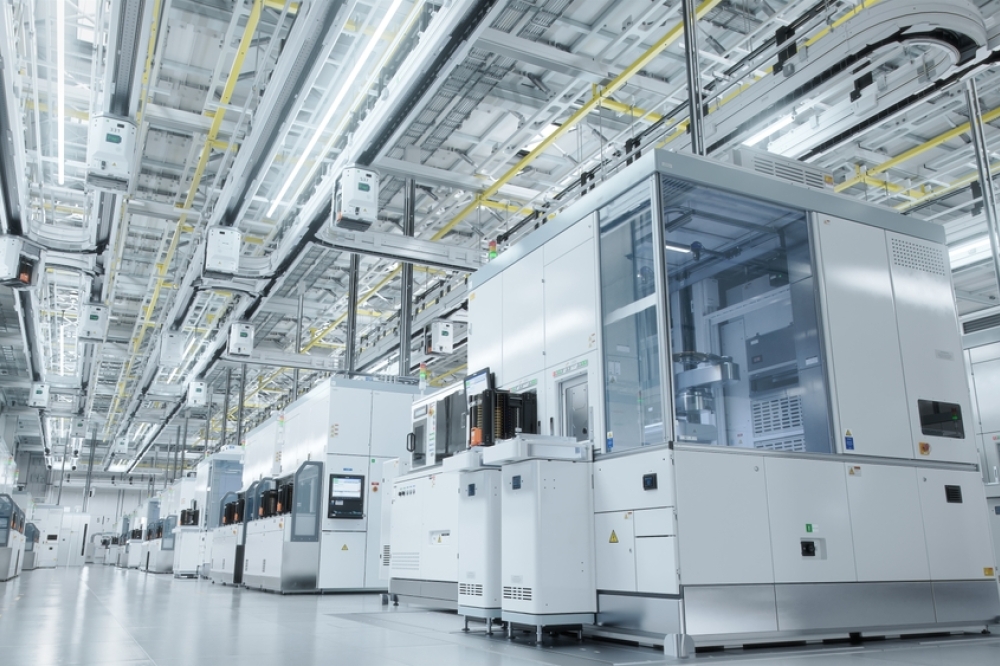
Plan is to 'revolutionise' leak detection in semiconductor manufacturing.
42 Technology (42T) has helped INFICON AG – one of the world’s leading manufacturers of leak testing devices and instruments – to develop a smart helium microdispensing tool for use in vacuum leak testing within the semiconductor sector.
The new handheld tool, called SMART-Spray, works with INFICON’s existing UL1000, 3000, 5000 and 6000 fab series leak detectors that are widely used within semiconductor, solar cell and flat panel display manufacturing plants.
SMART-Spray has been specifically designed to eliminate all the challenges engineers currently face with traditional helium spray guns, and to help them more easily pinpoint leaks when checking the integrity of sealed systems and process equipment. The new tool integrates a precision gas microdispenser with a remote display function for the leak detector into a single handheld device. This innovative design allows engineers to fully operate the system with one hand, leaving the other free for tasks such as gripping a ladder.
The new handheld helium microdispenser delivers a precisely-controlled microdose of helium and has its own refillable helium cartridge. It is also paired via Bluetooth to the leak detector, allowing it to display live leak rates on its own built-in screen.
“42 Technology has been instrumental in helping develop the world’s first handheld smart helium microdispenser for use in routine maintenance within semiconductor fabrication plants. SMART-Spray will simplify and speed up vacuum and leak detection processes that are critical for ensuring system performance, safety and environmental compliance,” said Markus Schwambera, strategic product manager for leak detection tools at INFICON.
42T has worked closely with INFICON on all aspects of SMART-Spray’s design and engineering: from the initial design concept and proof-of-principle testing through to manufacturing prototypes for customer trials and developing the final design for production. This has included industrial design, mechanical design, design for manufacture and assembly, electronics engineering, GUI and firmware development, and verification testing.
… more
Traditional helium spray guns are known for being particularly cumbersome and difficult to use. They need to be connected via tubing to a helium cylinder, and they rely on a hand-operated trigger valve making it difficult to dispense a small consistent volume of gas.
At the same time, test engineers typically have to hold a wired or wireless remote control in their other hand to operate the leak detector system. This makes it particularly difficult when engineers have restricted access to parts of the system and no hand free to support themselves.
Spraying a large, uncontrolled burst of helium, rather than dispensing a small microdose as SMART-Spray does, can lead to significant amounts of helium being dispersed into the atmosphere within the manufacturing plant too. This is unnecessarily wasteful but also results in higher background levels of helium, making it more difficult and time-consuming to detect leaks within the system being tested.