Carbon dioxide capture success
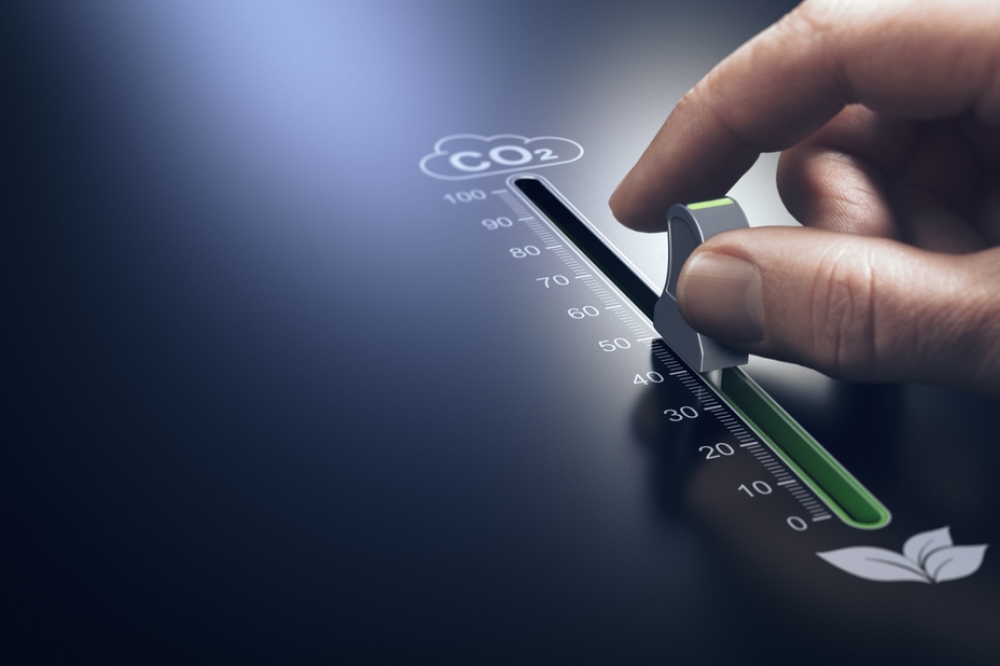
WACKER successfully tests carbon dioxide capture from the silicon production process.
WACKER has successfully captured carbon dioxide (CO2) generated from silicon production. The project, which was enabled by the technology and expertise of the SLB and Aker Carbon Capture Joint Venture (SLB-ACC JV), involved a pilot test of the capture process at WACKER’s production site in Holla, Norway, where quartz and carbon are combined to produce silicon for use in its silicone products. This reaction generates a considerable share of the CO2 emissions relevant to WACKER and its products. The newly tested capture process makes it possible to reuse or store this greenhouse gas and prevent its release into the atmosphere – a critical step on the road to net-zero chemicals production.
Holla is where WACKER manufactures roughly one-third of the silicon metal that it needs for its production. The company carried out a successful carbon-capture pilot project here. Combined with green electricity and the use of renewable charcoal, this will open the door to future climate-neutral silicon value chains (photo: WACKER)
SLB-ACC JV specializes in capturing CO2 from flue gases from large-scale industrial processes, including unavoidable CO2 such as that generated in the production of metallurgical-grade silicon. WACKER’s production plant in Holla produces this important raw material, which serves as the basis for microchips, solar modules and the full range of silicones.
SLB ACC JV’s mobile test unit (MTU) was installed at WACKER’s site in Holla. The MTU is a complete CO2 capture plant on a small scale. The waste gas generated from silicon production was piped directly into the pilot plant, where carbon dioxide was captured via a chemical process known as amine scrubbing. This makes use of an amine-containing solvent that selectively extracts CO2 from the gas mixture. In large-scale industrial processes, the CO2 is then released from the solvent by desorption before it is cooled, condensed under pressure and purified.
On the Road to Closed Carbon Cycles
For the first time, WACKER has demonstrated the amine scrubbing method for removing carbon dioxide in one of its own processes. The pilot test campaign, which was successfully concluded in late June, achieved capture rates of over 95%. The project team also thoroughly studied and validated the process parameters, delivering important information needed for large-scale implementation. At the same time, WACKER and SLB-ACC JV conducted an engineering feasibility study as well, which involved drafting a design for a plant that would capture 180,000 metric tons of CO2 annually. These calculations have now been supplemented with the data obtained in actual practice.
“The results of the pilot study are a huge success for us. We’ve shown that this technology makes it possible to remove CO2 effectively,” says WACKER CEO Christian Hartel. Capturing carbon dioxide prevents its release into the atmosphere as a greenhouse gas. It can then be put to other uses, such as creating synthetic fuels (e-fuels) or synthesizing methanol as a starting material for other chemical processes. Storing it underground (carbon capture and storage, CCS) is also an option. The project represents an important step on the road to closed carbon cycles. “What we need now are customers that will buy the CO2 from us and a regulatory framework that can help us build the business case,” Hartel goes on to say.
Net Zero by 2045
WACKER has set ambitious sustainability goals for itself. By 2030, the company’s absolute greenhouse gas emissions are to be 50% lower (compared to 2020). By 2045, WACKER intends to achieve net zero, which means it would no longer emit any net CO2 whatsoever. Silicon production in Holla is a major piece of that puzzle. The objective for this site is full CO2-neutral production. The energy-intensive manufacturing processes here began running on 100% green electricity from sources such as hydroelectric power back in 2022. And the gradual switch from bituminous coal to biogenic sources of carbon is to be complete by 2030. Green electricity, sustainable carbon and carbon capture will one day make climate-neutral silicon value chains a reality.
The amount of carbon dioxide released during silicon production is the most critical factor in the carbon footprint of silicones. The use of CO2-neutral metallurgical-grade silicon from Holla could significantly reduce the carbon footprint of the company’s silicone products.