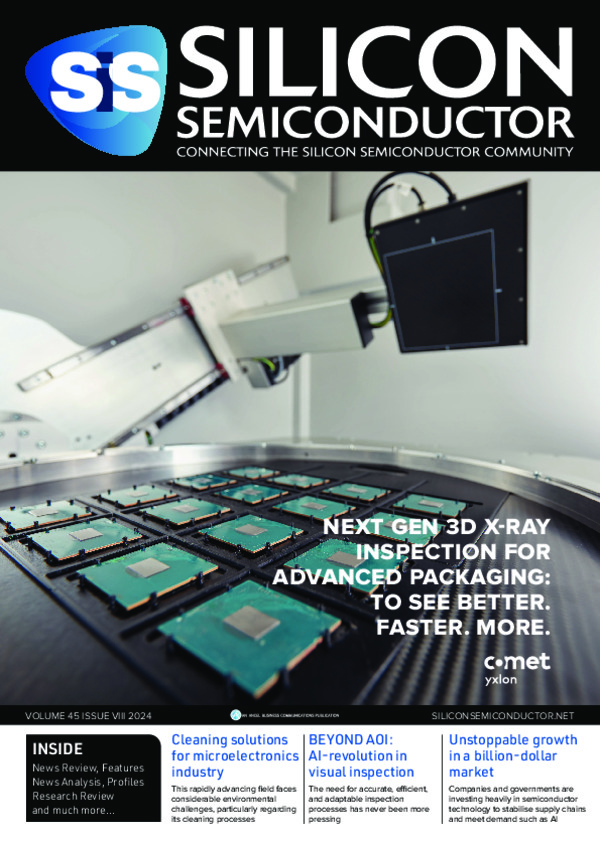
Beyond AOI: An AI-driven revolution in visual inspection
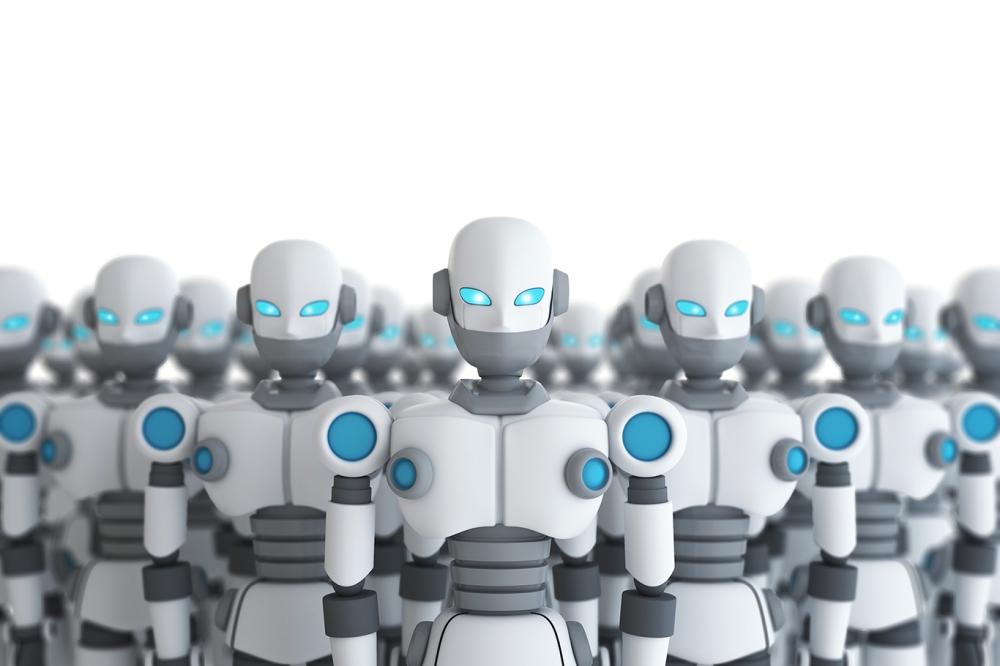
In the relentless pursuit of quality and yield in manufacturing, visual inspection plays a crucial role. As industries strive to produce flawless products, the need for accurate, efficient, and adaptable inspection processes has never been more pressing. In response to this challenge, Averroes.ai seeks to redefine visual inspection in manufacturing, which will ultimately replace outdated AOI inspection methods.
•The Quality Imperative: Quality control isn’t merely a buzzword; it’s a financial imperative.
According to a study by the American Society of Quality, the cost of poor quality in manufacturing organizations amounts to a staggering 15-20% of total sales revenue. This statistic underscores the critical importance of effective inspection processes across various manufacturing sectors, including electronics, semiconductors, and automotive industries. The impact of poor quality on a company’s bottom line highlights the need for advanced inspection techniques that can significantly reduce defects and improve overall product quality.
The evolution of visual inspection
Visual inspection has come a long way from its humble beginnings, but the rapid pace of technological advancement has outstripped traditional inspection methods.
Manual Inspection: The Beginning
Initially, manufacturers relied heavily on manual inspection processes, where human workers visually examined each product for defects. While this method allowed for detailed inspection, it was time-consuming and prone to human error, especially over long periods of repetitive work.
Semi-Automated Inspection: A Hybrid Approach
As technology advanced, semi-automated inspection methods were introduced. These provided workers with specialized tools to make more informed decisions and accelerate the inspection process. This hybrid approach combined the discernment of human inspectors with the efficiency of technological aids.
Automated Optical Inspection (AOI)
The next significant leap came with the introduction of Automated Optical Inspection (AOI) systems in the early 2000s. These fully automated systems use cameras and algorithms to detect defects without human intervention. AOI represented a major step forward in terms of speed and consistency, allowing for high-volume inspection in industries where manual methods were no longer feasible due to the scale and complexity of production.
The limitations of traditional AOI in modern manufacturing
However, the manufacturing landscape has changed since AOI was first introduced. Products are becoming increasingly smaller, more compact, and more complex. Defects are now harder to catch and often more subtle. The AOI systems designed for the technology of the early 2000s are struggling to keep up with these changes. What worked two decades ago is no longer sufficient for today’s manufacturing challenges.
The Need for a New Paradigm
As everything in manufacturing gets smaller and more intricate, the limitations of traditional AOI become more apparent. Complex defects that were once rare are now common, and the systems built for earlier technologies are proving inadequate.
This gap between inspection capabilities and manufacturing realities is driving the need for a new approach to visual inspection – one that can adapt to the increasing complexity and miniaturization of modern products.
How Does AOI Systems Work?
Traditional AOI systems typically consist of three key elements: the camera, the algorithm, and the actuator. While each component is crucial, the algorithm stands out as the most critical element, serving as the brain of the system.
Why traditional AOI Falls short in today’s manufacturing landscape
Accuracy: One of the primary issues with traditional AOI systems is accuracy. These systems often produce a high rate of false positives, flagging defects where none exist. This oversensitivity can significantly lower production yield, as perfectly good products may be unnecessarily rejected or subjected to additional inspection. The problem of false positives not only impacts efficiency but can also lead to increased costs and reduced overall productivity.
Flexibility: Adapting the algorithm to accommodate new product designs or detect new types of defects often requires a complete overhaul of the system.
This inflexibility can be a major drawback in industries where product designs evolve rapidly or where new types of defects may emerge due to changes in manufacturing processes.
Changes in the inspection environment: Changes in the inspection environment, such as variations in brightness or increased noise levels, can severely impact the algorithm’s effectiveness.
Even small changes in product design or positioning can lead to unreliable results, necessitating frequent recalibration and adjustment of the system.
Domain expertise required & resource intensive:
Implementing and maintaining traditional AOI systems is a resource-intensive process requiring significant domain expertise. Unlike AI-based systems, traditional AOI relies on programmed rules and parameters that need to be manually set and calibrated for each specific inspection task.
This process demands:
• Extensive knowledge of the manufacturing process and potential defects.
• Programming skills to create and adjust detection algorithms.
•Time-consuming calibration to ensure accurate detection.
• Ongoing adjustments to account for even minor changes in products or production processes.
The time-intensive nature of setup and recalibration can lead to production delays and increased costs, especially in industries with rapidly evolving products or frequent changes in manufacturing processes.
Averroes.ai: A paradigm shift in visual inspection
Averroes.ai has developed a deep learning engine to address these challenges. Their platform is designed as a no-code, no-technology-required solution that seamlessly integrates advanced AI into existing manufacturing processes. This innovative approach allows manufacturers to leverage the power of cutting-edge AI without the need for extensive technical knowledge or significant changes to their existing hardware
setup.
Integration with Existing Systems: The Averroes.ai solution operates as a software layer on top of existing hardware, utilizing images from current cameras to enable better-automated decisions. This software-based enhancement means that manufacturers can improve their inspection processes without the need for costly hardware upgrades or replacements.
The system takes in images from existing cameras and processes them through advanced AI models, displaying the results in a user-friendly graphical interface for review and analysis.
Exceptional Accuracy and Continuous Improvement
One of the standout features of Averroes.ai’s platform is its ability to produce custom-built AI applications tailored to each customer’s specific use case, achieving high accuracy with very little data. In one case study, the platform increased inspection accuracy from 63% (with the client’s previous tool) to an impressive 97%. This dramatic improvement in accuracy translates directly to higher production yields, fewer false rejections, and ultimately, better quality products reaching the end consumer.
The system’s ability to continuously improve sets it apart from traditional AOI solutions. Through active learning, the model suggests interesting images for human feedback, allowing it to evolve and further improve its accuracy over time. This means that the longer the system is in use, the more accurate and efficient it becomes. Starting with a model that may have 95% accuracy, the system can grow to 98%, then 99%, and eventually approach near-perfect accuracy through this iterative learning process.
Advanced defect detection and environmental adaptability: Another key advantage of Averroes.ai’s solution is its ability to detect anomalies and new defect types. The advanced AI models can identify previously unseen defect types - a capability that is particularly valuable in industries where new types of defects may emerge due to changes in materials, processes, or product designs.
When the system encounters a new type of defect, it can flag it as an anomaly, allowing human operators to review and classify it. Once classified, the system immediately learns from this input and begins to identify similar defects in future inspections.
Environmental adaptability is another strength of the Averroes.ai platform. Unlike traditional AOI systems that may struggle with variations in lighting or product positioning, this solution maintains high accuracy despite changes in the inspection environment. Differences in brightness or placement do not significantly impact the system’s performance, ensuring consistent results across various manufacturing conditions.
The engine behind the innovation
At the heart of Averroes.ai’s capabilities is its proprietary engine, a sophisticated deep learning algorithm that designs and creates models tailored to specific use cases. This engine, boosted by the company’s in-house DefectGPT model, can auto-generate complex models within hours while ensuring top-quality results.
The use of advanced AI in model creation allows for rapid deployment and adaptation to new inspection requirements, a crucial advantage in fast-paced manufacturing environments.
The Four-Step Process: Averroes.ai’s approach to transforming datasets into high-performance AOI models follows a straightforward four-step process.
The journey begins with data collection, where a small sample of images (preferably 10 or more per defect type) is gathered from the client. This initial dataset forms the foundation upon which the AI model will be built.
Next comes the model generation phase, where Averroes.ai’s proprietary engine utilizes this data to create high-quality AI models within hours. This rapid turnaround time is a significant advantage, allowing for quick deployment and testing of new inspection models.
Once the model is trained, it moves to the deployment phase, where it is integrated into the client’s inspection process. This integration is designed to be seamless, working with existing AOI equipment to minimize disruption to ongoing operations.
The final step in the process is continuous improvement. Leveraging human-based feedback, the model continues to learn and adapt, driving towards 100% accuracy. This ongoing refinement ensures that the inspection system remains effective and up-to-date, even as manufacturing processes or product designs evolve.
Flexible Integration Options: Understanding that different manufacturers have varying needs and constraints, Averroes.ai offers flexible integration options for its solution. The platform is designed to work seamlessly with existing AOI equipment, offering both cloud and on-premises deployment options to suit different operational requirements and security protocols.
Cloud Solutions: For clients seeking rapid deployment with minimal hardware requirements, cloud solutions provide an ideal option. These are compatible with major cloud platforms including Azure, AWS, GCS, and Apple Cloud, allowing for easy integration with existing cloud infrastructure. Cloud deployment offers the advantages of scalability, accessibility, and reduced on-site IT requirements.
On-Premise Solutions: On the other hand, on-premises solutions are available for clients that prioritize data security and in-house control. These can connect directly to local cameras or file systems, ensuring that sensitive manufacturing data never leaves the client’s facility. This option is particularly appealing for industries dealing with proprietary designs or those subject to strict data protection regulations.
Real-World impact: A case study
The effectiveness of Averroes.ai’s solution is perhaps best illustrated through a real-world application.
In one instance, a client’s existing inspection tool was missing 50% of defects, yielding only 63% accuracy. This level of performance was significantly impacting product quality and production efficiency.
By simply connecting Averroes.ai’s solution to the existing tool’s camera, the process was automated and enhanced, resulting in a remarkable improvement to over 97% accuracy.
This dramatic increase in accuracy demonstrates the transformative potential of AI-enhanced AOI. Not only does it lead to better defect detection, but it also reduces false positives, improves production yield, and ultimately contributes to higher-quality products.
The Averroes.ai platform: A closer look
The Averroes.ai platform offers a user-friendly, project-based approach to visual inspection. Each project serves as a container for related tasks, including data, models, monitors, and connectors. This organizational structure allows for easy management of multiple inspection processes or product lines within a single interface.
Team Collaboration Features: Team collaboration features are built into the platform, allowing project owners to invite collaborators and assign roles with varying levels of access. This facilitates seamless cooperation between different departments or team members involved in the inspection process, from quality control specialists to process engineers.
Versatile Dataset Creation: The platform supports versatile dataset creation, accommodating various task types including classification, object detection, and segmentation.
This flexibility allows the system to be adapted to a wide range of inspection requirements, from simple pass/fail assessments to complex defect localization and characterization.
Intuitive Labeling Tools: An intuitive labeling tool is provided for easy annotation of images. Users can resize bounding boxes, change labels, and enhance image properties such as brightness, contrast, and saturation. These features make it easier to label defects accurately, especially in cases where defects may be subtle or difficult to discern.
Advanced Model Training Options: When initiating model training, users have access to advanced options that can significantly enhance model performance.
These include active learning, which allows the model to identify and request feedback on the most informative images; anomaly detection (referred to as Watchdog), which enables the identification of new defect types; and smart augmentation, which uses AI to generate additional training samples based on existing labeled images.
Model performance and monitoring
Comprehensive Analytics Tools: The Averroes.ai platform provides comprehensive tools for monitoring and analyzing model performance. Users can view detailed accuracy metrics, track training progress over time, and access type-specific information such as the number of defects, true positives, false positives, and false negatives. This wealth of information allows for continuous assessment and improvement of the inspection process.
Flexible Deployment Options: Deployment options are flexible, with models able to be connected to cameras for real-time streaming or to cloud/local storage for automated predictions on newly uploaded images. This versatility ensures that the system can be integrated into various production environments and workflows.
API Integration for Custom Pipelines: For seamless integration with existing systems, the platform generates API keys for custom prediction pipelines. This feature allows manufacturers to incorporate Averroes.ai’s advanced inspection capabilities into their broader manufacturing execution systems or quality management processes.
Batch Prediction Capabilities: The platform also supports batch prediction, enabling users to manually upload large sets of images for analysis. This capability is particularly useful for large-scale testing and validation, allowing quality control teams to assess the model’s performance across a wide range of scenarios or product variations.
Conclusion
As manufacturing pushes the boundaries of precision and complexity, traditional AOI systems are proving inadequate for modern challenges. Designed for early 2000s technology, these systems struggle with today’s smaller, more complex products and defects.
Averroes.ai is not just enhancing visual inspection – it’s revolutionizing it. By leveraging advanced AI and deep learning, Averroes.ai aims to replace outdated AOI methods with a more powerful and adaptable solution. The company’s innovative approach, combining custom-built AI applications with high accuracy from limited data, positions it at the forefront of next-generation quality control.
As manufacturers strive to minimize defects and maximize yield in an increasingly demanding market, Averroes.ai’s technology promises to be crucial in shaping the future of manufacturing quality assurance, enabling higher quality, greater efficiency, and increased competitiveness.