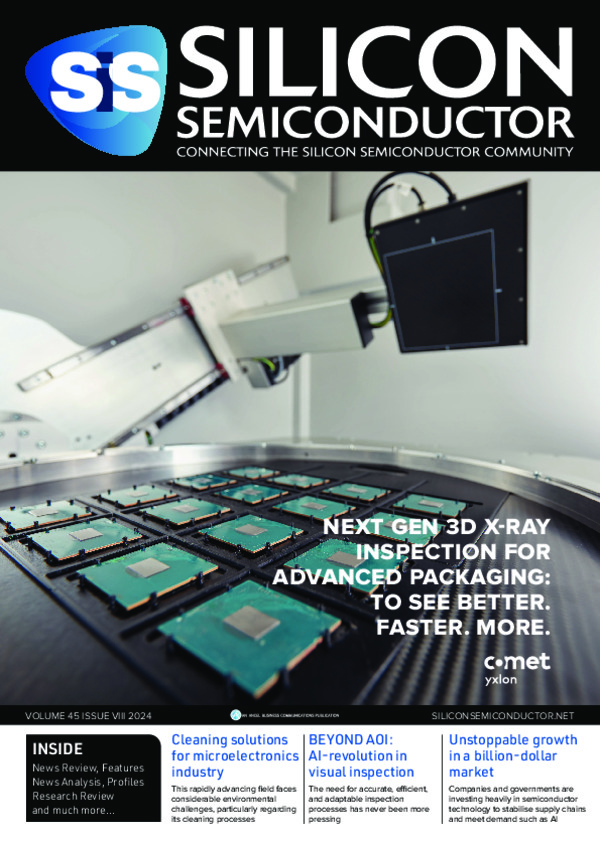
Sustainable cleaning solutions for a greener microelectronics industry
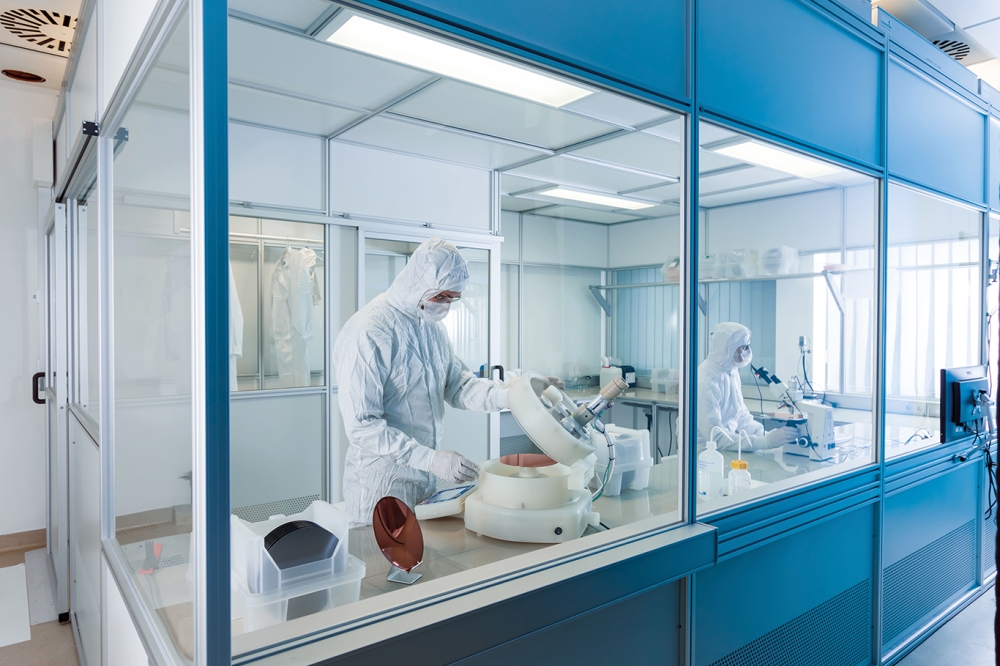
The microelectronics industry powers the devices that define modern
life, from smartphones and computers to vehicles and medical equipment.
However, this rapidly advancing field also faces considerable
environmental challenges, particularly regarding its cleaning processes.
Each year, the industry uses around 500 million liters of chemical
cleaning agents, many of which are petroleum-based solvents like
N-Methyl-2-pyrrolidone (NMP). While effective, these chemicals pose
significant environmental and health risks.
By Christian Römlein, CEO at Intelligent Fluids
Fortunately, sustainable alternatives that offer a great substitute for traditional chemical solutions are emerging. Water-based cleaning agents are both effective and eco-friendly, offering a viable replacement for conventional solvents. Yet, despite their benefits, these alternatives still remain underutilized in the microelectronics sector. Now is the time for the industry to reconsider its reliance on aggressive chemicals and embrace greener solutions that meet both technical and environmental standards.
In this article, we will explore the unique cleaning challenges of the microelectronics industry, examine the harmful effects of traditional solvents, and highlight the promise of water-based alternatives.
The unique cleaning challenges of microelectronics
The microelectronics industry operates on an incredibly small scale, with manufacturers working on components measured in micrometers and nanometers. This extreme miniaturization – seen most notably in the billions of transistors packed into a single microchip – requires equally precise cleaning processes. Any contamination left on these components can degrade performance or cause total product failure, making cleanliness a top priority.
Microchips undergo hundreds of individual processing steps, each of which may leave behind residues that must be removed before the next step.
A single computer chip, for example, can require up to 500 processing steps, with cleaning required after almost every stage. The complexity of these cleaning tasks increases as chips become smaller and more advanced, leading the industry to traditionally rely on chemical solvents that are believed to offer the most effective results.
However, this reliance on aggressive solvents comes at a significant cost – not only to the environment but also to human health.
The environmental and health costs of petroleum-based solvents
Petroleum-based solvents such as NMP, DMSO, and acetone have long been favored in the microelectronics industry due to their ability to efficiently dissolve contaminants. Yet, their extensive use carries serious consequences.
Once chemicals like NMP make their way into the environment, they can cause long-lasting harm, particularly to aquatic ecosystems. Acetone belongs to the group of volatile organic compounds (VOCs), which contribute to air pollution and can leach into soil and water sources if the disposal isn’t properly taken care of.
In addition to environmental concerns, petroleum-based solvents pose significant risks to workers who handle them. Studies show that prolonged exposure to solvents like NMP cause a variety of health problems, including neurological disorders, respiratory issues, and skin irritation. Some chemicals are also known to cause reproductive health issues, with women exposed to them facing a higher risk of birth defects.
Despite the risks, the general opinion still holds on to the belief that only strong, traditional chemicals can deliver the necessary precision in cleaning microelectronics. However, this assumption is increasingly being challenged by the development of green alternatives that are both effective and safe.
A green alternative: water-based cleaning agents
Water-based cleaning agents are emerging as a promising, eco-friendly alternative to petroleum-based solvents. Companies like the German deep-tech firm intelligent fluids are leading the way in developing these solutions, offering products that can replace conventional solvents without compromising on cleaning performance.
These water-based agents use microemulsions, which are stable mixtures of water, oil, and surfactants. Microemulsions operate through physical mechanisms rather than chemical reactions, with micelles – tiny, net-like structures – forming to lift off dirt and residues from surfaces. This physical removal process makes the cleaning action both effective and gentle.
A key innovation of companies like intelligent fluids lies in their ability to stabilize these microemulsions for industrial use. Their proprietary formulations maintain the effectiveness of these water-based solutions across a wide range of temperatures and storage conditions, addressing some of the limitations that have historically hindered the implementation of water-based cleaners.
A typical intelligent fluids formulation consists of water, oil, surfactants, and small amounts of additives like activators, or fragrances. The careful balance of components allows the water-based cleaner to achieve similar results to aggressive solvents but with a significantly lower environmental and health impact.
Applications in microelectronics: photoresist stripping and metal lift-off
Water-based cleaning agents are being tested and applied in various stages of semiconductor manufacturing, with two key applications standing out: photoresist stripping and metal lift-off.
In the production of semiconductors, photoresist materials are applied to a substrate and then exposed to light to create precise patterns. After the desired pattern is formed, the remaining photoresist must be thoroughly removed to ensure a clean surface for subsequent processing steps. Any leftover residue can compromise the chip’s functionality.
Traditional solvents chemically break down photoresist materials to remove them. In contrast, water-based agents developed by intelligent fluids physically lift off the photoresist using their phase fluid technology. This results in effective cleaning without the health and environmental risks associated with traditional solvents.
Similarly, in the metal lift-off process, metal which layers over a patterned photoresist must be removed. Water-based agents can break down the underlying resist, allowing the metal layer to be removed cleanly and without harmful chemicals. This method reduces the risk of chemical damage to both the delicate components and the environment.
The path to a greener future for microelectronics
The microelectronics industry is now at a turning point. While petroleum-based solvents have long been the default choice for cleaning, the environmental and health consequences of their use can no longer be ignored. Water-based cleaning agents present a viable, sustainable alternative that meets the rigorous standards of precision demanded by the industry.
Real-world applications have demonstrated that these green alternatives can deliver results on par with traditional solvents while significantly reducing the associated risks. As companies and regulators become more aware of these innovations, the adoption of sustainable cleaning solutions is inevitable. For the microelectronics sector, embracing water-based cleaners is not only a responsible choice but also a practical one. The technology is ready and available, and with it comes the opportunity to significantly reduce the environmental footprint of one of the world’s most essential industries.
The shift towards sustainable cleaning in the microelectronics industry is not just about compliance – it’s about leading the charge toward a greener, healthier future. By adopting water-based solutions, the industry can continue to innovate while safeguarding both human health and the planet.
Water-based cleaning agents can be applied for photoresist stripping and metal lift-off.