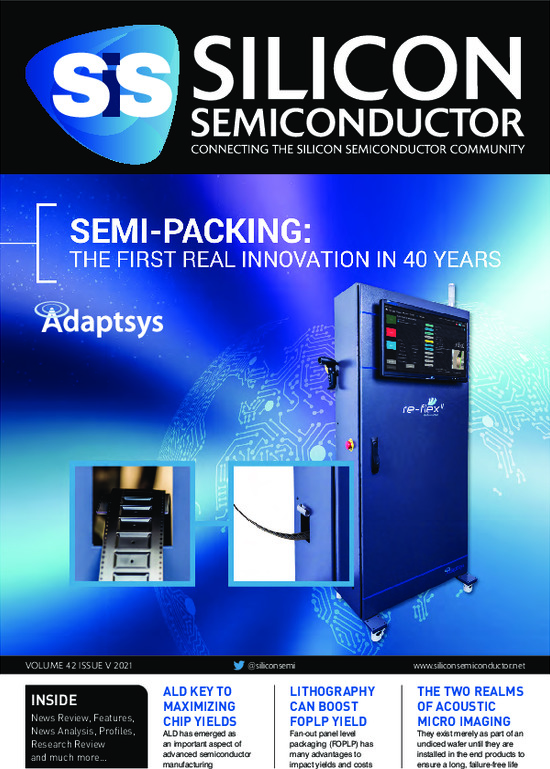
Make, Don’t Buy, for Freedom and Flexibility
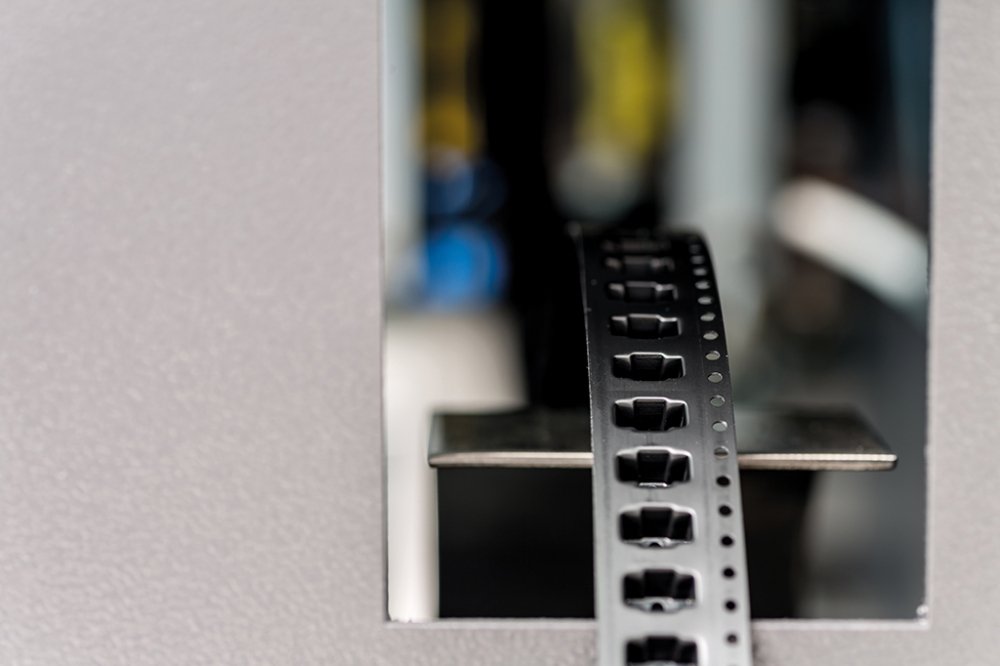
Taping components for delivery to customers? Owning the entire process,
from pocket forming to taping, can drive out supply-chain risks, reduce
costs, and shorten turnaround time
BY JAMES CAWKELL, TECHNICAL DIRECTOR, ADAPTSYS
TAPE-AND-REEL is the expected delivery packaging for a wide variety of components, to provide protection during transit and present parts efficiently to automated placement machines.
Component manufacturers and many distributors operate taping capabilities in house. The pocketed tape, however, is often purchased pre-formed from external suppliers. Various tape widths, pocket sizes, and designs are needed to provide suitable protection for the wide variety of ICs, discrete, and passive components currently being used throughout the industry.
Tape Supply Risks
Orders cannot be fulfilled if suitable tape is not available. Component suppliers are therefore challenged to ensure that the right types of tape are always in stock. As an alternative, producing the required pocketed tape in-house, as and when needed, could help overcome this challenge. Owning the pocket-forming process lets component suppliers buy raw, unformed tape and create the packaging they need on demand. It prevents running out of the right type of tape while also simplifying inventory, reducing expenditure, and saving storage space.
Adaptsys introduced the industry-changing Re-flex II tape-forming system as a cost-effective and usable solution to this challenge. Unique because it produces carrier tape “on demand”, Re-flex II was originally created to fulfil Adaptsys’ own need for pocketed tape. The resulting system proved so easy to use and versatile that the concept was readily commercialised. Adaptsys is now supporting multiple systems in operation with customers worldwide.
Some businesses may view making their own tape as a “non-core” activity that demands time, resources, and floor space that is better devoted to other materials and processes. But they are as vulnerable as any of their competitors if an important order needs to be fulfilled immediately and there simply is not enough tape on the premises. Waiting for tape to be delivered could translate into a lost opportunity. Re-flex II can provide emergency taping capability that requires no particular expertise and hence can be used on an ad hoc basis.
In this way, Re-flex II can be used in a backup role to mitigate tape-supply risks and provide the flexibility to turn unexpected orders around quickly. However, the system is equally suited to intensive use, fulfilling a company’s entire tape requirements.
Speed and Efficiency
With the latest upgrades, Re-flex II can form pockets at a tape-throughput rate up to four metres per minute. This is faster than typical component-taping equipment, so users have the option to feed freshly pocketed tape directly into their component-packaging process for optimum efficiency. It saves the overheads associated with storing and retrieving lengths of pocketed tape. Storing a supply of flat tape on standard sized reels can save up to 95% of the space usually needed to keep various types of pre-formed tape.
Feeding the tape straight into component-packaging equipment also reduces the stoppage time taken to change reels during component taping. The Re-flex II supply reel can contain up to 1000 metres of flat tape. If the taping process operates at 2 metres per minute, this allows up to eight hours of continuous operation before the input reel needs to be changed.
A similar reel of pre-formed pocketed tape can contain only about 40 metres, assuming a pocket depth of 6mm. Hence the reel needs to be changed every 20 minutes. In this way, Re-flex II significantly reduces operator intervention, raising productivity and enabling faster fulfilment of customer orders.
Return on Investment
The up-front investment needed to start making tape in house can be surprisingly low. Companies can recoup their investment in Re-flex II within 12 months, depending on usage. Its compact footprint, measuring just 75cm x 35cm occupies minimal real-estate in a factory or packing area and the system requires only a standard AC supply and compressed air.
The system can handle tapes up to 88mm wide and gives users the flexibility to create pockets in standardised or custom dimensions simply by changing the tooling. Quality inspection and traceability are provided for each formed pocket. The pockets may be simple shapes, such as a square, rectangular, or rounded recess, or may be specifically shaped to fit a particular component or provide certain functions such as protecting vulnerable pins or protrusions. Adaptsys can help customers create custom tooling where required and has successfully developed solutions for various special components such as small electronic modules and electrical connectors.
Re-flex II can produce intricate pocket designs suitable for protecting large semiconductor components, which are often supplied in other types of packaging such as trays, as well as smaller ICs, discretes, and passives that are typically supplied on tape and reel. It is also suited to creating pocketed tape for small engineering components such as stamped metal shields or miniature springs.
Changing the tooling to a different tape design in a production setting requires no special skills and takes just a few minutes, enabling users to produce pocket designs in almost any quantity from low and medium volumes to high volume.
Re-flex II can be used with any standard-size input and output reels up to 22” (560mm) in diameter, taking unformed tape from the input reel and delivering formed tape to the output reel.
Efficiency-Boosting Option
Now, Adaptsys has introduced a new option that enables tape/reel storage and transport to become even more space efficient without compromising reliability and ease of use. While Re-flex II is intended primarily for feeding pocketed tape directly into a component taper, the new Crosswinder option now enhances owners’ flexibility to produce tape onto reels to be stored for later use.
Similar to the development of the Re-flex II system itself, Adaptsys created the Crosswinder initially to meet an internal requirement for an ultra-efficient way to produce and store pocketed tape in extended lengths. It is now available commercially, ready to further boost the return on customers’ investment in Re-flex II. The Crosswinder neatly winds tape of a standard width, say 12 mm, across a 100 mm-wide reel to increase the storage capacity by a factor of 8 compared to an ordinary 12 mm reel. Also, a crosswound reel can supply significantly more parts to a high-speed component taper before needing to be replaced, thereby reducing changeovers. Crosswinder ensures the tape is neatly ordered to unwind smoothly, which helps avoid problems that may otherwise require the taper to stop. Crosswound reels are available in various widths to provide high maximum capacity.
Conclusion
Pocketed tape is an established medium for transporting electronic components and feeding automated high-speed assembly equipment. Many component suppliers have in-house parts-taping capabilities yet lack a suitable solution for producing the required pockets. However, the ability to form pockets in flat tape, on demand, can greatly increase flexibility and provide protection against supply-chain risks.
The Re-flex II pocket-forming equipment combines high throughput with ease of use and permits both standard and custom pocket designs. Changing the setup and tooling to create pockets of any required design takes only minutes and requires minimal training. Every component manufacturer should have one.