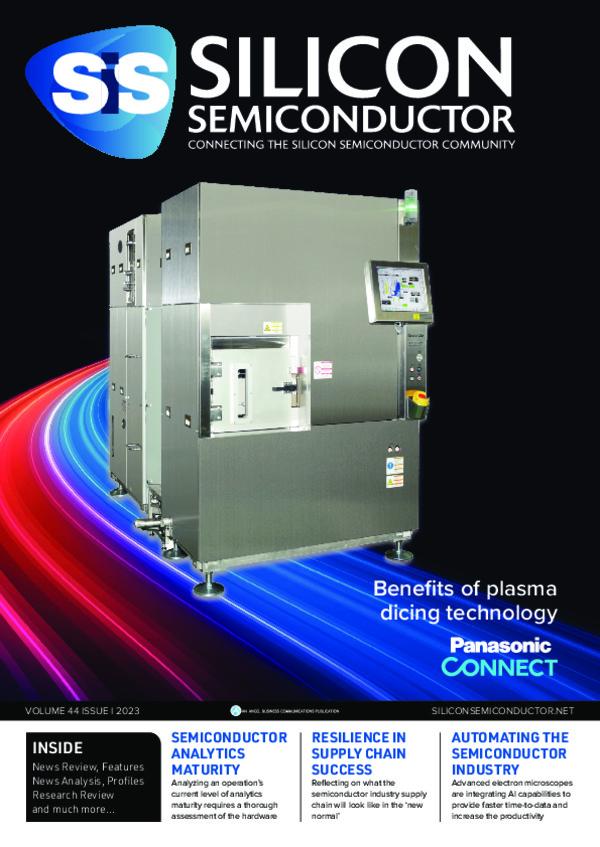
Improving yields, cycle times and overall equipment efficiency
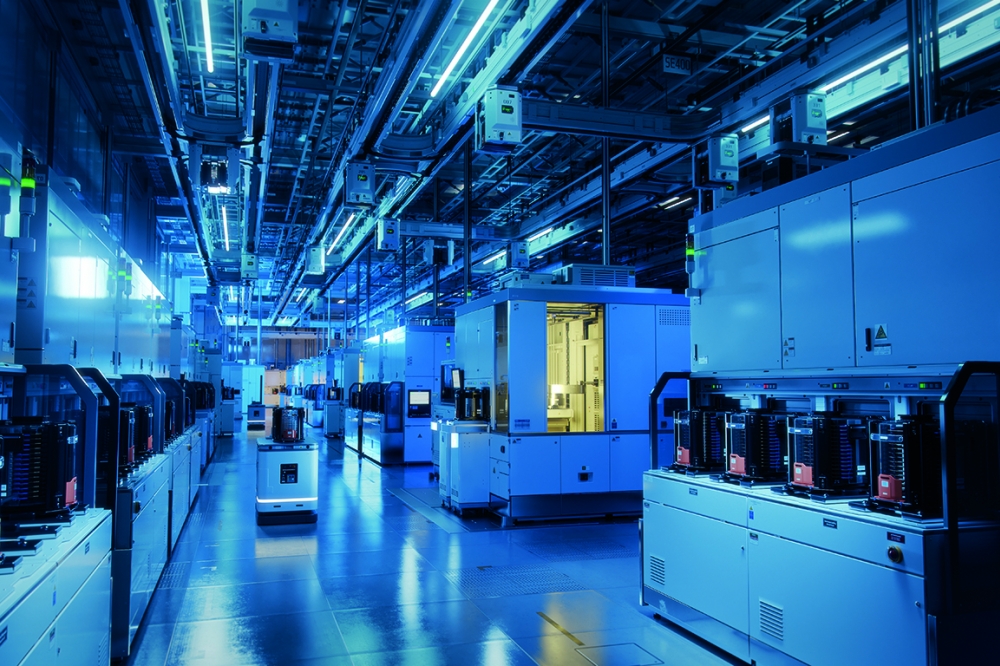
Mark Andrews, Technical Editor of Silicon Semiconductor magazine, speaks with David Meyer, Co-Founder and CEO of Lynceus. The company’s AI/ML modelling system integrates into a semiconductor foundry or IDM to analyse fab data in real-time. The resulting actionable insights help to identify manufacturing problems sooner, solve them faster, achieve process efficiency and improve operational sustainability.
MA: Perhaps we can start by considering how manufacturers work now, and how a product like the Lynceus system can be used to help them work better, more efficiently and without errors that lead to defects?
DM: Lynceus provides an accelerated “time to action” between a typical semiconductor manufacturing process and one enhanced by Lynceus. In a typical manufacturing environment, the process engineer needs to wait hours for the results of physical metrology before being able to take action.
With Lynceus Argo and our predictive ML models, the engineers are notified of any excursions in real time, and can take action immediately instead of hours later. In addition, unlike physical metrology, Lynceus ML predictive models run on every wafer manufactured, not just on a sample of wafers produced, so manufacturing visibility is increased to 100%. So, manufacturing defects that may not be present in a sampled wafer, but are present in a non-sampled wafer, would be detected by Lynceus but missed by traditional physical metrology.
MA: How does the Lynceus system differ from what’s currently available? In other words, would you compare how a ‘standard’ MES operates and what it can do to reduce or help eliminate defects, and what the Lynceus system can do in comparison?
DM: Manufacturers currently use two main tools to control their processes: Physical metrology: measurements of known outcome parameters influencing yield (CDs, etc) which are accurate but operationally disruptive. This means they can only be performed after the fact on a sample of production and therefore provide limited visibility to the process engineer
Statistical Process Control (including more sophisticated but essentially similar tools such as Fault Detection and Classification): application of control limits on known critical process parameters (temperature, pressure, etc) can help detect major deviations in how the process runs but only indirectly correlate with the outcome parameters. This means SPC often fails to flag defects related to more subtle process deviations
Lynceus bridges the gap in quality control by predicting the value outcome parameters for every wafer produced, in effect providing real-time visibility to process engineers over 100% of their production.
In addition, Lynceus includes a diagnosis module that explains every prediction (by identifying which variations in process parameters influenced the model), thereby helping engineers identify root cause much quicker. Lynceus real-time process control therefore helps manufacturers detect failures earlier, optimize physical metrology and accelerate the resolution of issues.
MA: I guess an obvious follow-up would be to ask why should the semiconductor industry in particular invest in a Lynceus solution as opposed to an alternative one?
DM: The Lynceus solution is specifically designed for high value manufacturing environments such as semiconductor fabs, while existing solutions are generally horizontal and unadapted to the constraints associated with those environments.
Concretely, Lynceus prioritizes the actionability of its solution over anything else - which boils down to 2 key elements:
- Robust predictive performance
- Actionable signalFor a model to be predictive in production conditions, it needs to remain accurate across a variety of different product and tool types, and over time (retrain a model every hour is not realistic). This means it needs to be able to generalize well from limited, highly unbalanced data which is a difficult task. Lynceus uses patented, proprietary modeling techniques in order to build and deploy the most robust models on the market.
This being said, even an accurate model is useless if it is not acted upon. Predictions need to be integrated into an actionable signal able to support production decisions. The objective is to make the life of the process engineer easier, which means the model output must include the context necessary for the process engineer to trust and interpret its predictions, as well as interface with existing out of control action plans. Lynceus combines AI expertise with experience of high value manufacturing environments to deliver a ready to use solution.
MA: And has Lynceus already secured any business in the semiconductor sector – helping to solve a real-world problem?
DM: We have been working with a top tier manufacturer of automotive chips to deploy our solution on an etching process, with the objective of providing real-time visibility over the key physical attributes of the isolation trench.
In order to control this process, our customer relied on physical metrology measurements performed on a fraction (c.5%) of production. In addition, given the necessary time to measure those attributes and the associated operational challenges, our customer only measured wafers every few days which essentially means that it took them a few days to detect process deviations. Given that they are producing 24/7, this lack of visibility means every process deviation impacts a significant share of production, resulting in high level of scraps.
Deploying Lynceus enabled them to reduce the time necessary to detect process deviations from days to hours, while gaining visibility on key isolation trench attributes for every wafer. Our customer wass therefore able to decrease the metrology measurement frequency by 4x, thus improving both cycle times and the overall equipment efficiency of their etching tools.
MA: So, the customer has seen great value in the Lynceus solution? And are there any other benefits that the system has provided this customer, or in more general terms?
DM: We saw how Lynceus helps manufacturers improve yield, cycle times and overall equipment efficiency at the scale of the single process step in the fab through real-time process control.
Deployed at scale, ie over all the critical processing steps in the fab, Lynceus can deliver additional benefits:
Metrology scale down: Lynceus helps decrease metrology sampling frequency at the scale of the single process. At the scale of the entire fab, this could enable manufacturers to reduce their fleet of metrology tools, both reducing the associated CAPEX spend and increasing the floorspace available for revenue-generating equipment. For reference, metrology makes up 15-20% of the processing steps in a fab so the potential savings are very material
Electrical test prediction: Covering all critical processing steps in a fab means providing real-time feedback on the performance of the most important contributor to the device’s electrical performance, measured at the very end of the manufacturing process. This means that Lynceus could in theory use data from every major contributing process to provide real-time feedback on the probability of success / failure at electrical test. A wafer typically takes several months to arrive to electrical test, going through hundreds of highly costly processing steps along the way - spotting failures early would represent a step change versus current process control capabilities.
David Meyer, Co-Founder and CEO of Lynceus