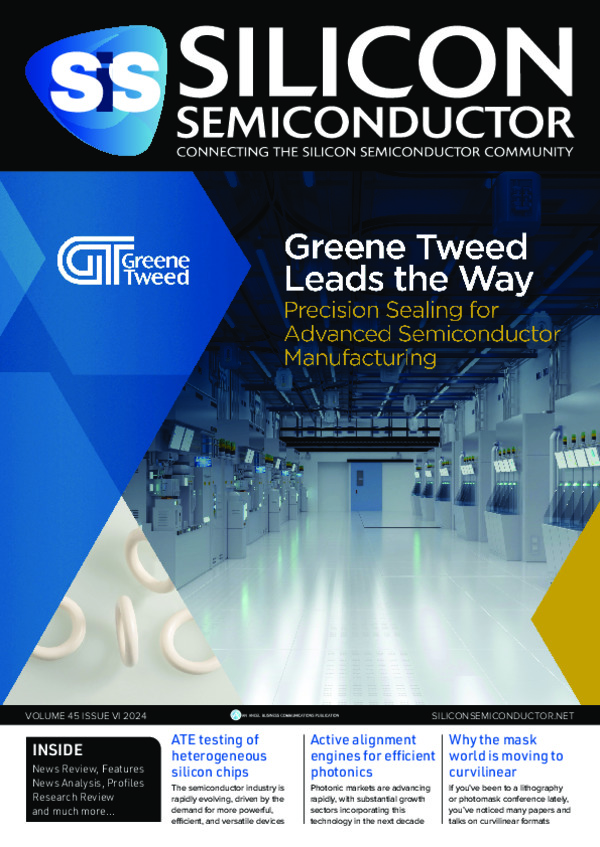
Precision sealing for advanced semiconductor manufacturing: Greene Tweed leads the way
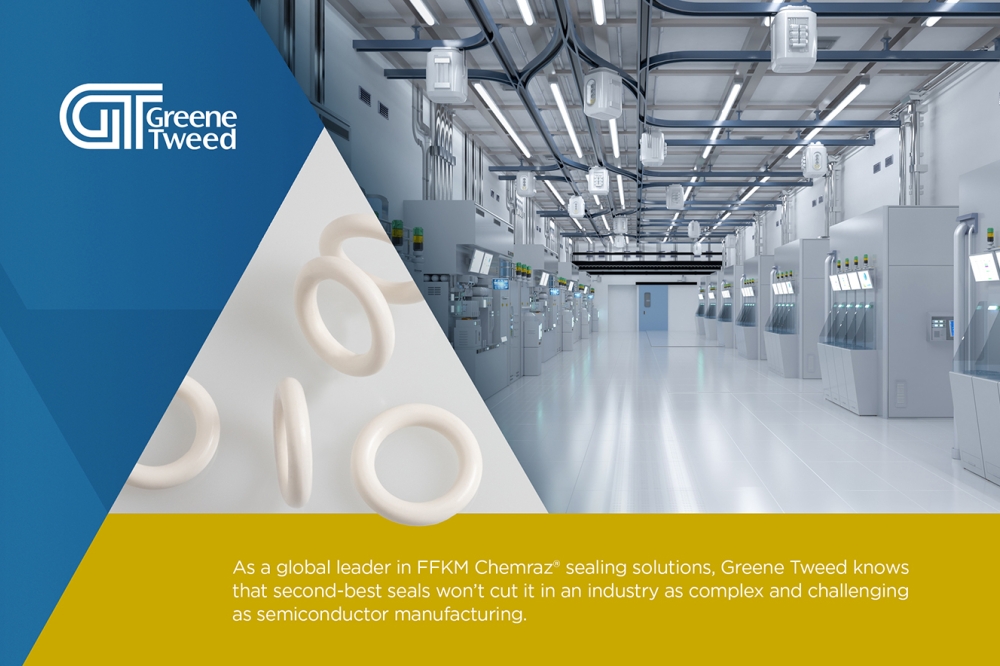
The semiconductor industry is poised to double to $1 trillion in six years, putting pressure on manufacturers to scale up. As a global leader in FFKM Chemraz® sealing solutions, Greene Tweed knows that second-best seals won’t cut it in an industry as complex and challenging as semiconductor manufacturing. Discover how the company is stepping up its game to ensure that chipmakers have everything they need to thrive in this era of unprecedented growth.
Historians could call the 2020s the ‘new Roaring 20s’ — the decade of artificial intelligence (AI). The AI boom started when the world woke up to the promise of generative AI. Momentum is building as 2024 is promising to be the year of adoption for several AI applications. McKinsey research shows that the trend will continue, and generative AI could enable automation of up to 70 percent of business activities by 2030, adding trillions of dollars in value to the global economy.
These AI applications and their insatiable demand for data heavily rely on semiconductors for processing and storage. Unsurprisingly, McKinsey expects the global semiconductor market to double to $1 trillion by 2030, raising the stakes for manufacturers who need to scale up to keep up with the demand. On top of that, the growth in AI is also pushing them toward more powerful smaller processor nodes so that they can fit more increasingly complex transistors on a single chip, resulting in more intricate designs.
This complexity translates to more advanced manufacturing processes with harsher conditions. Manufacturing processes often require extremely high temperatures and aggressive chemicals and harsh plasmas, posing significant risks to materials and components in the equipment. The entire operation occurs in cleanrooms where even microscopic particles of dust or slight chemical contaminant can cause defects and compromise the performance and reliability of the chip being made.
When it can’t fail
In this dizzying race to build new fabs, semiconductor manufacturers are not only exploring advancement in chip design, materials, and architectures but also need a steady supply of several inconspicuous yet indispensable components, such as Greene Tweed’s Chemraz® seals, critical for manufacturing new advanced chips.
Greene Tweed, a global leader in Perfluoroelastomer (FFKM) Chemraz® sealing solutions, is leading the way in this rise with its own multi-million-dollar investments in facilities and several new products and manufacturing automation technologies.
“Several prominent chipmakers depend on Chemraz® seals to fabricate their most powerful chips and second-best seals aren’t good enough for their challenging manufacturing environments,” says Shawn McCloskey, Chief Commercial Officer of Greene Tweed. “We are fully committed to supporting our customers and ensuring that they have the sealing solutions they need to meet the soaring needs for semiconductors.”
This criticality of Chemraz® sealing solutions is growing as chipmakers turn to more demanding processes. Thyag Sadasiwan, General Manager of Chemraz® at Greene Tweed explains why, “Our Chemraz® o-rings and sealing solutions meet the critical demands of modern chip fabrication by preventing contamination while withstanding aggressive chemicals and extremely high temperatures. As a result, these sealing solutions outperform and outlast in the world’s harshest semiconductor manufacturing applications.”
Another factor making Chemraz® seals indispensable is the increased need for ultraclean processing in the more advanced manufacturing applications. Being the first sealing solutions company to use cleanroom manufacturing in the US, Greene Tweed fully understands the significance of ultraclean operations in the semiconductor industry and ensures that our seals control particle excursions that could cause contamination while improving uptime and boosting wafer yield.
Rising to the challenge
Scaling up to provide chipmakers the solutions they will need during the anticipated boom won’t be easy. But the recent industry-wide supply crunch gripping the FFKM materials that coincided with a global surge in demand for chips gave us valuable insights into how to meet the burgeoning demand and minimize the impact of possible disruptions.
Building on the insights, Greene Tweed is rolling out six major initiatives to ensure that we are able to promptly deliver their high-performing Chemraz® sealing solutions, as the customer needs evolve to meet the growing demand for semiconductors:
1. New manufacturing facility in Korea
Greene Tweed is investing to expand its global manufacturing capacity and capabilities for the semiconductor market. An excellent example is the newly constructed 70,000 square feet (6,500 sq m) facility in Ochang, Cheongju-si, Chungcheongbuk-do, Korea. This factory is equipped with end-to-end manufacturing process capabilities – from initial extrusion of raw materials to warehousing of the finished products. We have started producing samples and will transition to commercial production later this year.
Featuring cleanroom space to maintain a pristine environment vital for components supporting chip fabrication, the facility will initially focus on Greene Tweed’s flagship Chemraz® product line known for its superior performance in demanding semiconductor applications. It doesn’t just increase the global capacity but also underscores the company’s commitment to supporting customers based in Korea and the surrounding region, including notable semiconductor leaders. It will help improve lead times, build stronger co-development strategies with key customers, and enhance business continuity plans, implementing a healthier global supply chain.
The state-of-the-art plant is equipped with advanced manufacturing technology as well as solar panels and greywater recycling facilities to mitigate environmental impact.
What’s more, the new facility is designed with scalability in mind and offers ample room for growth, enabling us to expand our production capabilities as demand increases. We will be implementing a phased rollout of new production lines. In the next few years, we will increase capacity and add automated equipment to enhance our production processes and reduce lead times. In the next phase, we will focus on further expansion, including an additional cleanroom, and integrating cutting-edge manufacturing technologies and processes.
This long-term strategy ensures that we remain agile and responsive to our customers’ evolving needs as the demand for semiconductors grows over the rest of the decade and beyond.
2. New innovations designed for harsh conditions and expansion
As a global leader in FFKM seals, Greene Tweed knows that Chemraz® seals are critical for the most advanced semiconductor fabrication processes. To support our customers’ growing needs, Greene Tweed has introduced two new high-performing, price-competitive products – Chemraz® G38 and G57.
“With an unwavering focus on performance and supply chain resiliency, we are developing several new Chemraz® products to meet the evolving needs of various plasma applications while being highly price competitive and delivering world-class lead times. The additions demonstrate our commitment to continuously innovating and responding to the demands of the market, ensuring that our customers have the best solutions at their disposal,” says Thyag Sadasiwan.
Custom-engineered to meet the demands of aggressive dry plasma systems, Chemraz® G57 provides improved plasma resistance and minimizes contamination, resulting in less downtime and higher wafer processing yields in both static and dynamic oxide etch wafer processing applications. It offers excellent chemical resistance and can withstand temperatures up to 572°F (300°C) and is ideal for several applications, such as endpoint windows, window seals, slit valve seals, bell jar seals, isolator valve seals, chamber seals, valve seals, lid seals, KF fitting seals, and gas inlet seals.
Chemraz® G38 is developed for high-density plasma systems where seal reliability and minimal contamination are essential. It provides excellent chemical compatibility and withstands a variety of aggressive chemicals. Recommended for bonded gate seals and chamber seals, it delivers exceptional value in applications such as deposition, remote plasma cleans, oxidations, diffusion, ion implant, implant anneal, and rapid thermal processing.
This journey of innovation continues, and another Chemraz® sealing solution is ready to roll out in the next six to 12 months. In addition, our existing sealing solutions, including Chemraz® and Fusion® F07 fluoroelastomer, are being adopted by customers to meet the increasing needs of semiconductor fabrication and subfab plants being built around the world.
3. Next-Gen manufacturing to accelerate growth
Greene Tweed is committing significant resources to automate manufacturing processes to scale capacity and quickly meet the growing needs of semiconductor customers as they evolve.
By supplementing core manufacturing processes with robotics and digital solutions, the company is supporting production floor employees to eliminate process bottlenecks and enable shorter lead times.
The largest investments have been made for high-impact process steps, like compression molding, inspection, and packaging, to maximize efficiency and productivity gains. For compression molding, operators are currently responsible for moving and servicing molds between every cycle.
An automated solution has been developed that uses a 6-axis robot to move molds, allowing the operator to focus only on the value-added activities and service more molding presses. Similarly, for current packaging operations, operators are responsible for bagging and labeling parts individually which is slow and tedious.
An automated solution has been developed that utilizes multiple SCARA robots and an automatic bagging machine to improve throughput and standardize bagging quality. Additionally, digital twins are being built and utilized to proactively evaluate the new innovative technologies and how to best introduce them into existing manufacturing facilities.
These technologies and dedicated technical resources are transforming production lines, making them more adaptable, and allowing us to scale up quickly to meet our customers’ needs without compromising on excellence.
4. Secured resources
Expanding manufacturing capacity is just one prong of the multifaceted strategy to prepare for an upturn in a market as cyclical as semiconductors. To support world-class lead times, Greene Tweed has secured a reliable supply of raw materials from multiple suppliers to cover the anticipated ramp over the next two years.
Running four factories with balanced workloads, the company has significantly increased the workforce to stabilize the production process and bolstered manufacturing capabilities with multiple new equipment in the Korea, Taiwan, and Selma plants. These strategic moves are designed to not just keep up with growth, but also enhance production capabilities, minimize delays, and excel in delivery times.
5. Fortified supply chain resiliency
As Greene Tweed works to secure a steady supply of raw materials, the company is proactively reducing reliance on a single vendor or a market. Here’s why: The industry-wide FFKM supply crunch during the pandemic-led surge in demand for semiconductors taught us the significance of diversifying and strengthening the supply chain. That’s why Greene Tweed has carefully selected multiple sources of raw materials located in separate regions.
Proactively identifying and mitigating potential risks ranging from geo-political to regulatory and climate change events, Greene Tweed has built a comprehensive supply chain resiliency and business continuity plan and shared it with customers to ensure transparency.
By securing raw material and building supply chain resiliency, Greene Tweed enables its customers to reduce downtime and meet the incredibly tight production schedules needed to meet the fast-increasing demand during the anticipated boom. That can be critical in the semiconductor industry, where missing a time-to-market window can shrink revenues considerably.
6. Ready for the new design at tool OEMs
Major semiconductor capital equipment manufacturers are upgrading their tools to move to smaller processor nodes and the resultant complex processes. Whether it’s the latest innovations in lithography or etching, they are creating an increased demand for wafer equipment seals and Greene Tweed is taking proactive steps to keep up with this growth. Greene Tweed’s patented LF10 coating has allowed equipment manufacturers to meet the stringent performance of the next-generation semiconductor nodes.
At the same time, our bonded slit valves, lip seal, seals for electroplating solutions, vacuum line solutions, cryogenic seals and many other sealing solutions continue to be widely adopted by equipment makers. Most recently, our Xyfluor® materials were qualified in electrostatic chuck solutions requiring temperatures below - 40C.
Ready for growth
Building cutting-edge semiconductor chips is a challenging and cost-intensive process that hinges on small yet essential components such as Chemraz® sealing solutions.
Working closely with its customers and partners, Greene Tweed is ready to address the burgeoning need for its Chemraz® sealing solutions from chipmakers, ensuring the scalability and sustainability of their operations for the rest of the decade and beyond.