Feature: 5 Tips for Selecting and Optimising Wet Processing Equipment
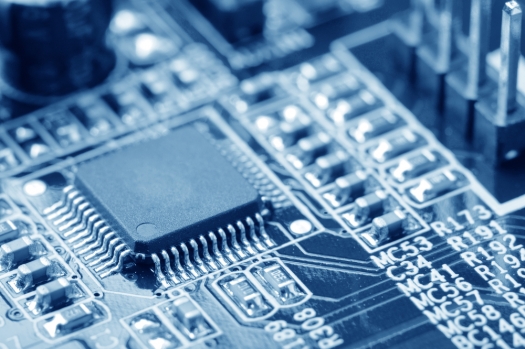
Microfabrication operations such as metal lift-off, stripping, etching, plating/coating, cleaning, and de-bonding are typically wet processing procedures. Yet, selecting the equipment to perform those procedures most efficiently and cost-effectively is often not a simple matter. In most cases, the users of wet processing equipment "“ whether for semiconductor, MEMS, biotech or other applications - can benefit substantially from having industry design experts review and evaluate the entire process and then recommend specific equipment solutions.
Even among research and educational applications where off-the-shelf, manual wet benches may be presumed as standard solutions, such applications can gain valuable flexibility, quality or safety though relatively inexpensive customization of the apparatus design by the equipment manufacturer.
Here are five tips that can help users to select wet processing systems that can optimize their processes by making them more flexible, efficient and productive.
Don't reinvent the wheel
"So many wet processing equipment designs/fabrications have been standard for some time and are usually a variation of one of these standards. " says Louise Bertagnolli, president of JST Manufacturing. "The l design process is a matter of choosing the most appropriate solution and then tailoring it to meet the customer's specific application requirements."
A nationwide manufacturer of manual and automated wet processing equipment, JST's mechanical, electrical, and chemical engineers have many years of experience in industries including semiconductors, both silicon and compound , MEMS, photovoltaics, LEDs, Flat Panel Displays , and sensors.
Bertagnolli says that to optimize quality and throughput for a wet processing solution, it is advisable to consider the process involved so that a qualified, objective recommendation "“ including the tools and accessories - will be proposed. The equipment manufacturer should have the research and development engineers, facilities and experience to propose appropriate manual or automated process equipment plus necessary auxiliary equipment such as chemical handling, automation and product fixturing.
Take a close look at fixturing
In addition to determining how a customer's process will be finalised, one of the most important elements to consider is the customer's fixturing "“ the devices that will hold or position the products being processed," says Bertagnolli.
She adds that most customers are mostly concerned about the temperatures and concentrations of chemicals "“ things that are going to materially affect their processes - and how they are going to control those.
"But at the design stage, there are also more fundamental decisions to be made, such as how the product in process should be transported to and from the wet processing tools and fixturing most efficiently in the process baths," Bertagnolli explains. "In some cases the products may be too heavy for workers to handle, so appropriate manual or automated transporting equipment must be selected. Additionally, the wet processing chemistry must be determined: How does the chemistry arrive at the tool, and how is the chemistry extracted safely?"
Fine-tune processes in the "application lab"
Before finalizing a wet processing solution, visit an equipment manufacturer that has a well-equipped laboratory so that the process can be fine-tuned and tested on-site. This can ensure that the best solution is proven, and that equipment overkill is avoided.
"Advanced application labs should be equipped with metrology [advanced measurement] equipment offering real-time testing results that provide the data and technologies needed to optimize the process," explains Bertagnolli.
The applications lab also enables users to control the optimization of multiple processes, and can minimize the amount of chemicals required and/or determine the tool features they need for their applications. This can save the customer money by eliminating features they do not need.
Bertagnolli suggests that by utilizing 3_D modeling software such as SOLIDWORKS facilitates making modifications to best suit an application in a timely and cost effective manner. For automated wet processing, the equipment manufacturer's control software should be able to interface with a customer's host system when required in order to be able to remotely operate the tool.
"Also, many customers forget to determine how they are going to accommodate the new equipment in their clean room; how it will enter the facility, how much space it will occupy, how much power, water, chemicals and gases it will require, and so forth," explains Bertagnolli. "So, the equipment design engineers will need to plan for all those factors."
Consider evolving application requirements
Like other manufacturing processes, wet processes such as cleaning and etching often evolve over time. The upgrading or expansion of equipment to meet future requirements can be unnecessarily expensive and time-consuming unless the requirements are integrated into the original equipment design.
"If tools are designed to be modular, there is not usually any problem in reconfiguring or expanding them," Bertagnolli advises. "But the engineers that design the tool need to be aware of the customers' future plans to upgrade their operations for reasons such as added throughput. All sorts of process expansions are possible, but it is very important for the design engineers to be aware of future plans at the initial design phase."
In some cases the customer's initial wet processing equipment is semi-automated because production volume does not mandate a fully automated system. But over time the volume may increase to the point when a fully automated system is warranted in order to optimize production.
"It is not unusual for a customer to come to us with a requirement, new process, new technology or something they have been doing manually and now their volume requirements have increased to the point where they need to automate because of a higher throughput requirement," says Bertagnolli.
Ensure that safety is built into the solution
Although production throughput and product quality may be the highest priorities of many users of wet processing equipment, operator safety of both manual and automated equipment should also be a paramount concern, particularly when processes involve the use of dangerous chemicals.
The potential for fires from electrical problems is a great concern within processing laboratory environments. For that reason, explosion-proof motors and a variety of safety mechanisms are required when wet processing chemicals warrant such measures.
With most designers and fabricators, both manual and automated systems must meet the safety standards set forth by organizations such as NFPA (National Fire Protection Association), SEMI (Semiconductor Equipment and Materials International) and NEC (National Electric Code).
In some cases a low-throughput research facility will automate wet processing simply for safety purposes because they don't want employees to be exposed to potential hazards. In other instances, design engineers may advise customers against choosing a certain process or configuration, recommending a safer way to perform the operation.
In Bertagnolli's opinion safety comes first. "As far as JST is concerned: If there is a hazard, we strive to eliminate it," she says.