Nanometrics Introduce Analysis Software to maximize fab productivity
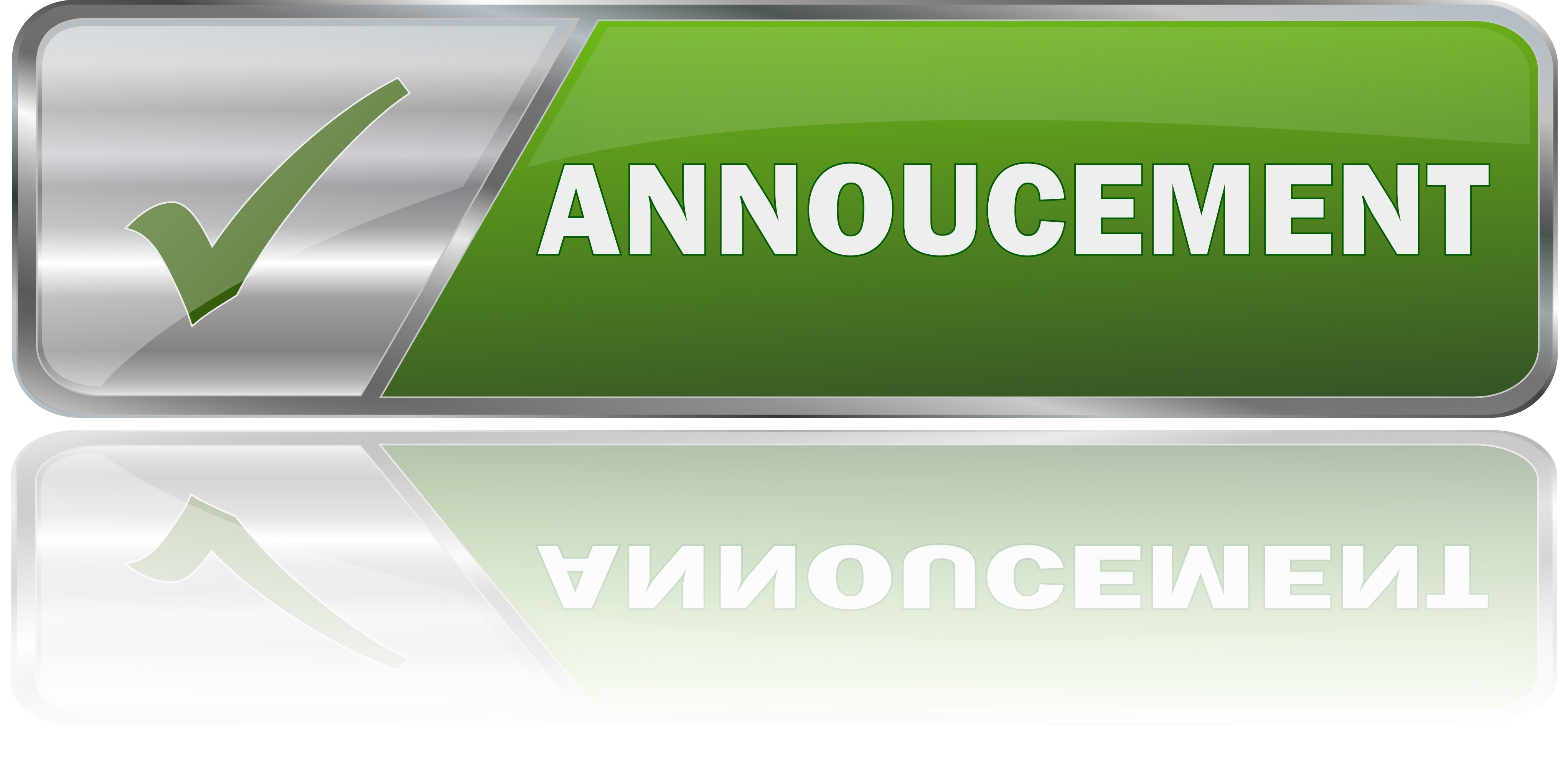
Nanometrics, a provider of advanced process control systems, has announced the introduction of SpectraProbe, a new software-based process control solution designed to provide advanced data analytics to maximize fab productivity. Complementing the high-fidelity modeling capabilities of NanoDiffract for optical critical dimension (OCD) metrology, SpectraProbe analyzes data generated by a customer's fleet of Nanometrics Atlas, IMPULSE and T3 metrology systems, providing real-time excursion monitoring, rapid model-less OCD recipe analysis and tracking of other process parameters.
When combined with patented Atlas full Mueller matrix data set and SpectraProbe machine learning algorithms, a unique model-less recipe mode has been developed for 3D-NAND channel hole etch tilt measurement. "Not only are we be able to reduce time to solution from days to minutes, SpectraProbe measurements can be done in-die. Furthermore, our tilt measurement mode provides customers with the ability to discover excursions quickly and determine when process tools, such as etchers, require maintenance, generating a significant cost savings in preventative maintenance cycles and meaningful improvement in edge of wafer die yield," said Adrian Wilson, vice president and general manager of the software & data analytics business unit at Nanometrics.
SpectraProbe expands Nanometrics software process control metrology suite which includes model-based NanoDiffract OCD measurement and fleet management tools for the Atlas, IMPULSE and T3 family of metrology systems. "We are engaged with multiple customers in advanced 3D-NAND development that are working to resolve new manufacturing challenges as they ramp their processes. SpectraProbe provides our customers with expanded analysis capabilities, reduced time to solution and new insights into process tool performance," continued Wilson. "Our machine learning algorithms can stream process health in real-time to a user dashboard, a factory host or directly to the fab's big data analytics system, providing customers with even more data and insight to control manufacturing processes".