Precision Drying: A Critical Step in Wet Process Cleaning
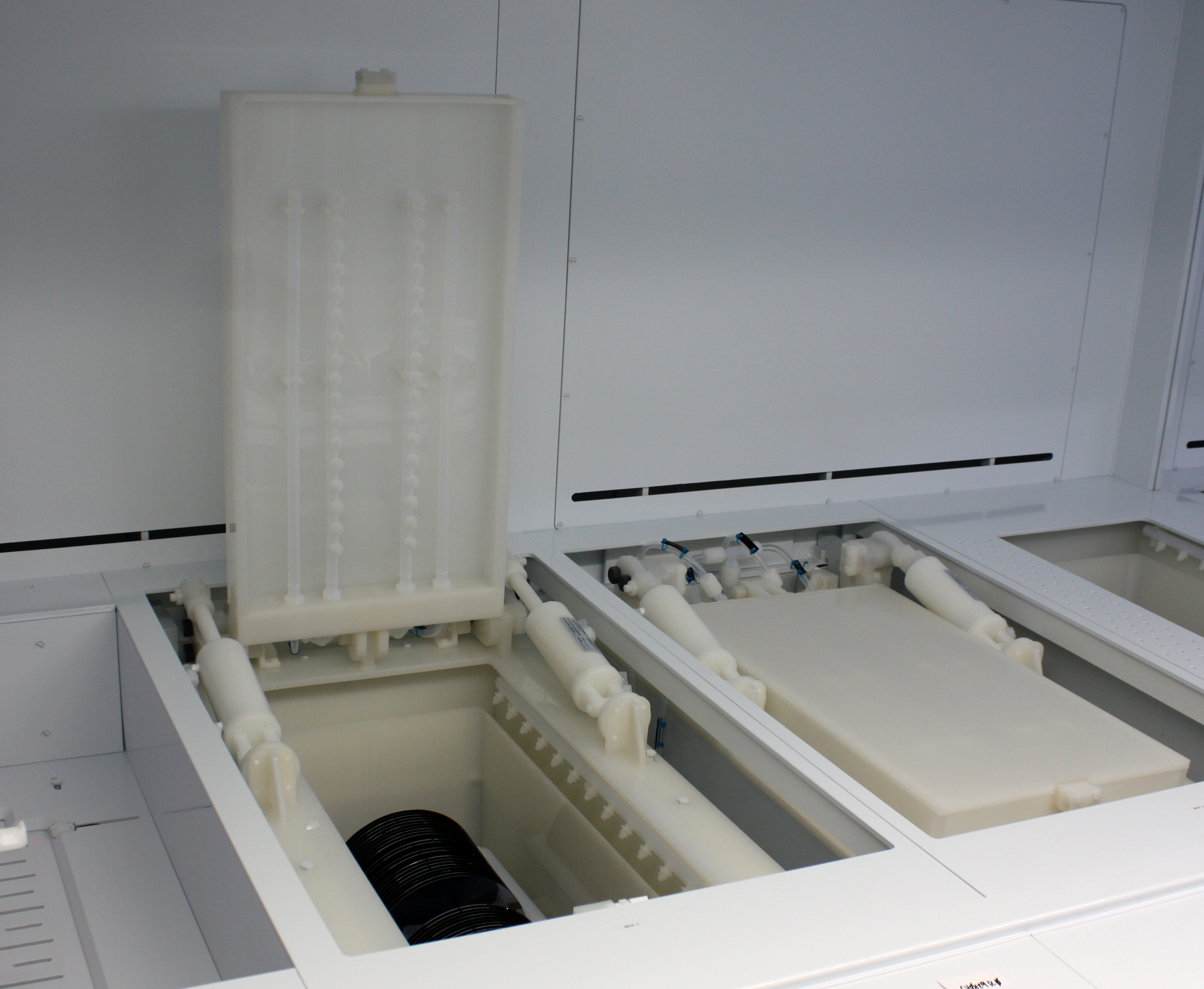
Cleaning, an integral part of many manufacturing and maintenance processes is often critical to the performance of a broad range of technologies in the semiconductor, defense, MEMS, photonics and biotech industries.
In this case, "cleaning" refers to the use of agents such as solvents, acids or bases to remove unwanted particulates and other contaminates from products ranging from optics to semiconductor and electronic devices.
It also refers to the etching process utilized in semiconductor fabrication, where the "cleaning" is the precision removal of thin layers of material.
In both cases, the "wet process" cleaning involved usually incorporates the chemical cleaning agents, an appropriate rinse bath, and a method of drying the material.
However, while attention is typically focused on the chemicals used, along with time, temperature and agitation, matching precision drying to the cleaning process and even customizing it is an essential element that must be considered. In this effort, partnering with an expert can help to fine tune certain critical variables such as level of cleanliness and drying speed as well as any required adjustment for product geometry.
"You can wash to clean or etch but rinsing the entire chemical off and then drying is just as critical as the wash itself," says Louise Bertagnolli, president of JST Manufacturing (Boise, ID), a specialist in wet processing and precision cleaning equipment.
Selecting a Drying Process
There are many types of drying that can be incorporated into the cleaning process depending on the goal, according to Bertagnolli.
"Consideration must be given to the key factors in the drying process," says Bertagnolli. "This can be the final cleanliness of the surface with low residual particle counts, drying time, or a combination of both. The drying should be geared to do the most effective job based on your criteria."
While convection drying, N2 blowoff, and HEPA drying are sufficient for many applications, they may not be the best choice for those where low particle counts are important.
With convection drying, the drying chamber is heated to evaporate the water off the product, and hot, filtered nitrogen or clean dry air can assist the drying. While low cost, this can leave behind residue and water spots as the water evaporates. Depending on the volume of water, this can take a long time. The process is not suitable when a clean dry is required or when products are temperature sensitive.
In an N2 blowoff dryer approach, nitrogen is blown into the drying chamber through high pressure air knives. The moisture is blown off the product and down into the plenum where it is evacuated in the exhaust stream. Although the process is initially lower in cost, it uses a lot of nitrogen, may not totally dry product, and does not work with geometries that retain moisture when removed, including those with blind holes.
With a HEPA filtered blowoff dryer, hot clean air is blown through a HEPA filter and into the drying chamber where it evaporates the moisture. Once again, though the operational cost is low, it may not totally dry product, and does not work well with moisture retaining geometries.
To leave the least amount of particles, such as for silicon wafers, glass substrates, disc drives, or optics, Bertagnolli recommends either a Surface Tension Gradient (STG) Dryer or a closed loop isopropyl alcohol (IPA) vapor vacuum dryer.
Utilizing a STG dryer, the chamber is filled with water and then IPA vapor is slowly introduced into the chamber as the water is removed, replacing the water with IPA. The IPA is then evaporated. The process has several advantages. There is no water spotting and no moving parts to generate particles. It uses relatively little IPA and is environmentally friendly with low IPA emissions. The process, however, dissolves IPA in the water and drains it out. It also uses a large amount of deionized water for rinsing.
With a closed loop IPA vapor vacuum dryer like JST's CLV model, ultra clean vapor is generated and then introduced into a sealed drying chamber. The closed loop system allows fresh IPA vapor to rinse the surface to be dried, penetrating the surface areas and absorbing the moisture. A low pressure vacuum pulls any remaining moisture from the sealed chamber and away from the product being dried.
This process has a number of advantages. It offers the cleanest dry with no moving parts to generate particles. It dries blind holes and eliminates water spotting. It is also environmentally friendly with low IPA emissions.
Product Geometry and Features
Along with selecting a drying process, it is important to look at the geometry and features of the product being dried to optimize the entire procedure. The handling of non-standard items of various geometries, sizes and weights is a factor that most customers do not think about, says Bertagnolli.
"If you lift a product out of a chemical bath, it will carry some moisture with it," she says. "If flat, it will carry more than a sphere, so its geometry and how it is removed will dictate how the equipment should be optimized."
In these instances, the geometry of the product requires vacuum drying or oven drying. This is also the case with items that have blind holes, which are drilled, bored, or cast to a specific depth.
"When a product with many holes is soaked in a chemical bath, those holes can retain a lot of chemical so you might want to rotate it to dump out the chemical and/or rinse water before drying it," says Bertagnolli.
In another example, round shapes "“ such as silicone rods that are cleaned using wet processing "“ clean more easily than flat shapes, which are more prone to hold moisture when removed.
Paying attention to the carrier rack or fixture for the parts is also important to ensure no excess water is retained, according to Bertagnolli.
"It doesn't do any good to dry the part thoroughly if you leave the carrier or rack wet," she says. "So consider how both the product's features and the rack affect the drying process."
Even the rack's construction is important because materials like Teflon are porous and hold moisture.
"For the rack, it is better to use a non-porous construction because it quickly releases water," says Bertagnolli.
While cleaning involving temperatures and chemical concentrations is often the main concern of process industry professionals and research labs, considering how drying can be enhanced will significantly improve the entire process.