Dry run over IC bridge
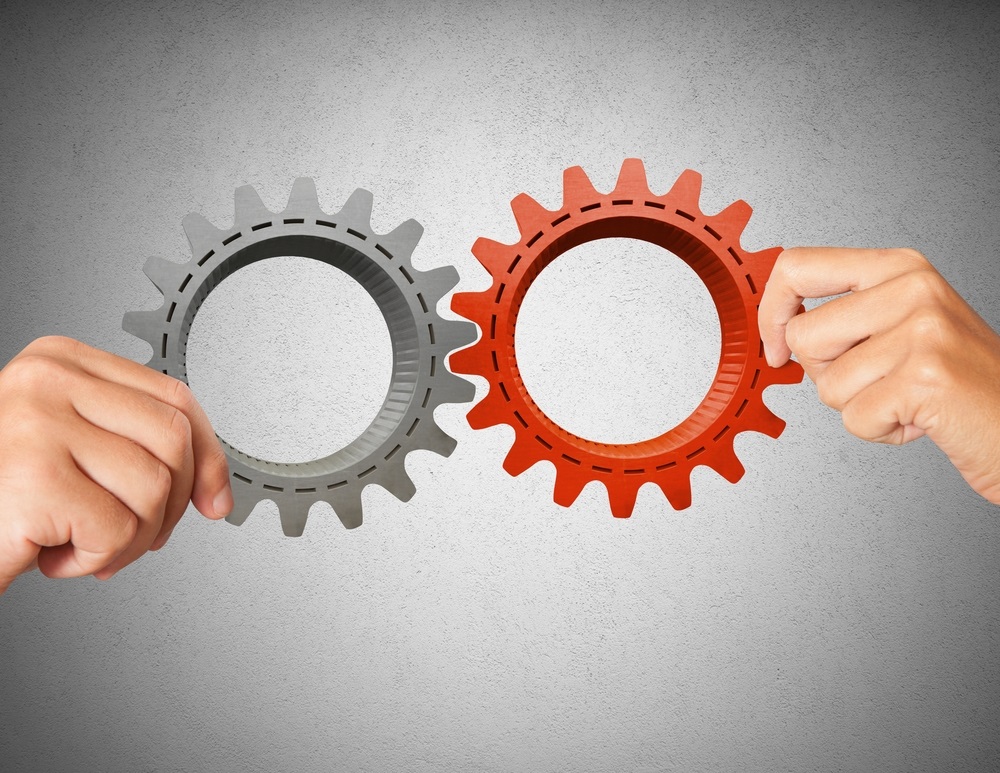
Keeping moisture out of electronic components before they enter the manufacturing process is a critical concern for the automotive sector. Melexis has tackled the problem and come up with a towering solution.
Cars have always needed to be safe, but safety is no longer just about having robust engine and chassis. With the shift in automotive technology being from mechanical to electronic, it is the performance of the electronic components that need to be completely reliable.
The consequences of failure can, of course, be devastating as these component manufacturers are all too aware. One of the leading players in the automotive semiconductor sensors market is Melexis, and it has recently completed the first phase of a new project to ensure components are delivered in the same impeccable condition that they were made in.
Moisture in semiconductors is a serious issue. Trapped moisture can vaporise and expand when subjected to the temperatures of a reflow oven during assembly. While this can lead to catastrophic failure of the part during the production process – an effect called ‘popcorning’ – it can also introduce cracks and weaknesses in the component that could present reliability issues once the assembly is out on the market. It is an issue that is obviously taken very seriously both by the electronics assembly sector in the way that they handle and store components, and also by the semiconductor makers themselves.
What Melexis was aiming to achieve with this latest project was to provide additional assurance for the step from its semiconductor factory in Ieper, Belgium to its assembly customers. The site works round the clock to test around 40 million ICs a month principally sensors for the automotive market, though their high performance has also led to applications in consumer and industrial.
Bertrand Leterme, Manufacturing Manager at Ieper, explained he was “looking to control temperature, humidity and timing. The Dry Tower project enables us to do this accurately.”
Dry Tower is the solution provided by Totech, a company that was already well-known to Melexis. “Totech solutions and tools are known and used internally and at our customers,” continued Leterme, who also recognised ‘Totech’s support and reactivity’.
This project was looking at the stage just before final packing and sending off to customers. All components will have had their final optical inspection before being taped and reeled, and then this final drying stage ensures components are completely dry before despatch. It is a stage that is standard – and defined by standards – within the industry. All components are held for a minimum of 24 hours at 1% RH (relative humidity).
Totech’s standard drying cabinets were already being deployed at an earlier stage in the Melexis process. However, to use these cabinets for the final drying application would have meant a footprint of around three times that of the adopted Dry Tower solution - and floor space was one of the key considerations.
After benchmarking against another main European supplier, it was considered that the Dry Tower would offer the best solution. Leterme said: “Totech provided more technical answers to our concerns. And has proved in the past year to give good support in case of trouble - important in our market.”
The Dry Tower is really designed for automated storage with precise and proven environmental control technology. However, its ability to tie in with inventory control systems made this an ideal solution to Melexis’ drying requirements. Leterme says: “It gives us the expected control and traceability for our products and our customers. There is also flexibility in the software to manage large batches of reels including a high automated quality control.”
Moreover, it will allow Melexis to continue to develop the project. “The tool is flexible and gives us capacity for potential future production automation projects,” Leterme commented. The next step over the coming year or so is to increase the level of automation with the addition of customised conveyors and other automated handling equipment - the Dry Tower is currently loaded and unloaded manually.
Perhaps, ultimately, the Dry Tower could play its part in a full ‘Smart factory’ scenario. All component data is saved into a data base, from when it enters the system after reeling to when it leaves the Tower for packaging and shipping.
It sounds like a complex arrangement for a one-day stop-over for components on their way to their end application, especially as they will already have passed their ‘final’ test. However, it is a stage that forms a crucial bridge connecting the often separate worlds of semicon and assembly, and it is imperative - if we are all to drive in efficient, comfortable and, most importantly, safe cars - that these components cross that bridge in perfect condition.