Multibeam to Develop Full-Wafer, All-Maskless Patterning at 45 nm
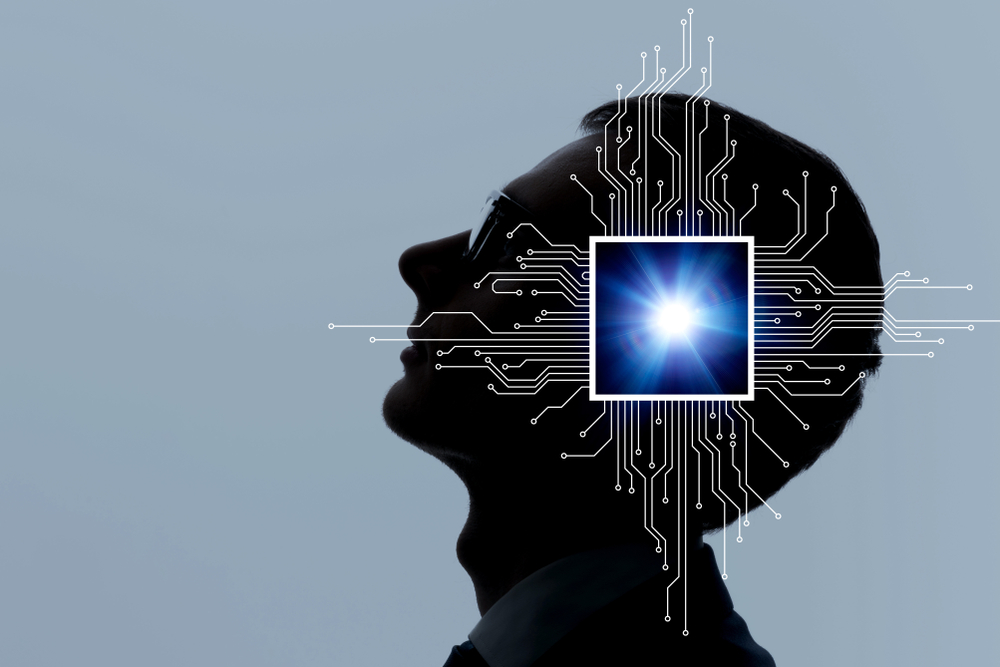
Multibeam Corporation has embarked upon a project to apply its innovative Multicolumn E-Beam Lithography (MEBL) technology to pattern entire wafers at 45nm and larger nodes, without the use of any masks, for back-end-of-line (BEOL) processing. Funded by the Department of Defense (DoD) and program-managed by the Air Force Research Lab (AFRL), Wright-Patterson Air Force Base, the $38 million contract award includes an option for the U.S. Government to purchase another MEBL production system from Multibeam.
“This contract award along with the Secure Chip ID application we have been developing under an earlier DoD contract highlights the versatility of our innovative MEBL platform,” said Dr. David K. Lam, Chairman/CEO of Multibeam. “Both applications are designed to run on our MEBL production systems.”
Assured and Trusted foundries typically produce a “low-volume, high-mix” of chips for the DoD. But optical lithography equipment leaders have little interest in such small quantities of chips with a large variety because their businesses are geared toward high-volume production. Moreover, there continues to be a need for early-generation chips with “mature” nodes. While masks for such nodes are less expensive, mask-related costs do add up. Masks in less demand often have long lead-times, negatively impacting fab productivity in production as well as cycles of learning in new-chip development.
IoT chips are generally small, simple SoCs that perform specific tasks and are ubiquitous on the Internet. Such chips have been credited for the dramatic rise in IC content in most Government, commercial, industrial, and consumer products. As a whole, IoT chipmakers are high-volume producers. But their batch sizes are relatively small because IoT applications are diverse and the IoT market is fragmented. Competing in this cost-sensitive market is a real challenge. Yet, low-volume, mature-node IoT chipmakers get little support from optical litho equipment leaders focused on high-volume manufacturing at cutting-edge nodes. As a result, there have been scant advances in DUV (193nm ArF dry or immersion) litho systems since 2007 when optical resolution reached its limit.