Keep Calm and Carry On – Covid 19 and the Semiconductor Industry
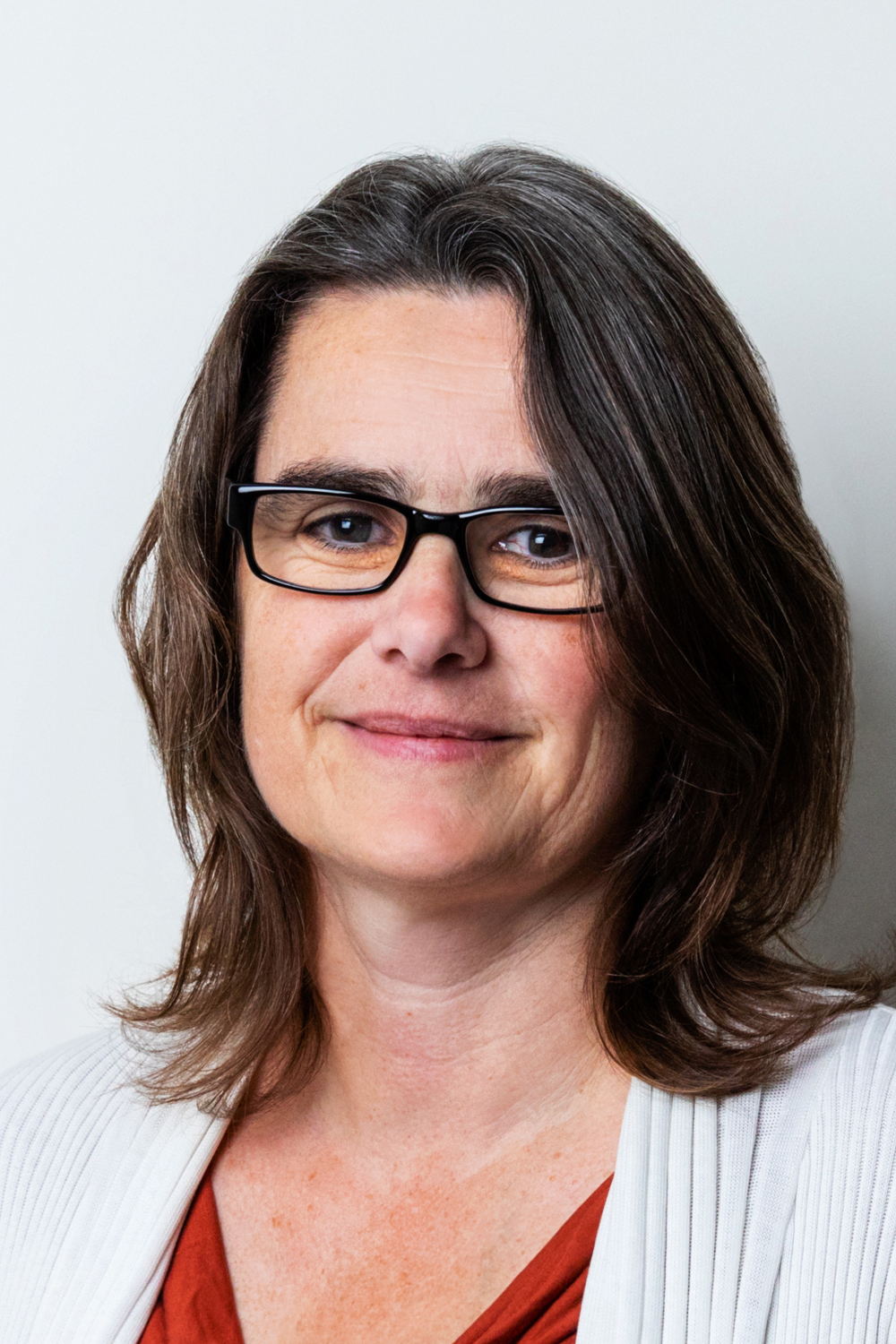
Kate Wilson, VP Marketing, Edwards Vacuum
We have all been challenged by the Covid-19 pandemic. As an essential part of an essential industry, Edwards has faced specific challenges in maintaining production and providing support to our customers. As with most challenges, we have found coping strategies that have allowed us to continue operating while minimizing disruptions and ensuring the health and safety of our customers, our employees, and the greater communities that we serve. In some cases, the challenges have become opportunities – where the new coping strategies have turned out to be more productive, or safer, or, in some other way, better than the old ways.
Our industry has been fortunate. At least until now, we have seen relatively little impact when compared to industries like hospitality and entertainment that have been devastated. According to the World Semiconductor Trade Statistics (WSTS) organization, worldwide sales of semiconductors (3-month moving average) were up almost 5% to $34.5 billion for June 2020 compared to $32.9 billion for June 2019, though off slightly from the $34.6 billion recorded the previous month (May 2020). Quarterly sales for Q2 2020 topped Q2 2019 by a little more than 5% but were down almost 1% from Q1 2020.
Keep Calm…
While we are grateful for our own good fortune, we are mindful of those who have suffered tragic personal and financial loss in the wake of the pandemic, and we must not allow our good fortune to lull us into complacency. The pandemic is far from over. In the best case, there remains considerable uncertainty about the future. In the worst-case–an extended economic downturn–none of us will be spared. Now is the time to look carefully at the things we can do to further mitigate the impact of the pandemic. An essential part of that is sharing knowledge of strategies and practices that have worked for us.
Supply Chain Management
Throughout the Covid-19 crisis, our global manufacturing facilities have remained open. We did have some short-term shutdowns at facilities in some parts of the world, but they were minor. Those facilities too are now open and running at 100% and continue to ship products. Our smaller service and support facilities have also remained open in most locations. Early in the year we even saw an acceleration of shipments as some customers pulled in delivery dates, perhaps in anticipation of trouble to come. Our biggest challenge has been in managing our supply chain, which extends around the world. Most of our suppliers have long maintained disaster preparedness plans, and, for the most part, those plans seem to have been effective. Overall, we have avoided major disruptions and credit is due in large part to the efforts of supply chain managers at Edwards and throughout the industry.
Customer Service and Support
Like politics, all service is local. As the virus has worked its way across the globe, it has confirmed our strategic commitment to prioritize the development of local service capability wherever possible. To be sure, we have had to adjust our assets and procedures to conform to local, virus-related requirements, always keeping the safety of our own and our customers’ personnel foremost. But the choice to load our service network “at the edge”, close to the customer, has allowed us to provide ongoing support through the pandemic while minimizing long-distance travel. Accommodating local regulations may be as simple as ensuring the availability of personal protective equipment, scrupulously following disinfecting protocols, and practicing social distancing.
While the pandemic has reinforced the importance of having the right person, in the right place, at the right time, we have also seen the real the power and effectiveness of remote support. Travel restrictions have reminded us how important it is to have global assistance readily available to assist local personnel through greatly improved data and personal communications technologies. This is indeed an area where a response to Covid-19 will likely persist long after the pandemic has run its course. Remote support cannot solve every problem, but, when it is successful, the elimination of travel time almost always delivers a faster resolution. Even when an in-person visit is ultimately required, an accurate remote diagnosis can shorten repair time by making sure the right people and parts are available. The keys to success lie in planning, preparedness and pre-positioning of parts and other resources.
Customer Relationships
Another challenge has been maintaining close working relationships with customers. Ours is an industry that changes rapidly. Technologies and processes are constantly evolving. Success requires intimate exchanges of information about plans and future requirements. Remote meetings can work, but they are unlikely ever to be as good as face-to-face contacts in building trusting relationships.
Organization Behaviors
Organizational impacts have certainly been greatest on employees who have suddenly found themselves working from home. While there may be some efficiencies (such as not having to dress for success, at least outside the view of the web cam) there are also deficiencies, most notably the loss of incidental contacts and casual personal interactions. Some have found it harder to stay motivated and focused. In other areas, such as my own – marketing, the organization was already far flung and interactions predominantly remote. Still there was a tendency to focus plans and projects around in-person meetings and bigger conferences. Eliminating in-person meetings may have reduced the inclination to wait for the meeting to get something done – do it now. We have also found that it helps to have shorter, more frequent, more focused meetings, and to intentionally design remote meetings to include opportunities for small talk and social interaction. We have become more flexible, but we have lost the comfort that comes from habitual behaviors.
And Carry On…
While the pandemic persists, we must do what we can to reduce or eliminate unnecessary contacts among individuals. When contact is necessary, it should as brief and involve as few people as possible, and all participants must follow procedures to reduce the likelihood of transmitting the virus.
· Apply global knowledge locally – Restrictions on travel have magnified the importance of local expertise. It is better to have a service engineer across town than across an ocean. At the same time, in our global industry, local expertise must be informed by the global knowledge available only from a central organization with broad reach and deep experience.
· Be proactive not reactive – Anticipate needs, predict maintenance, pre-position resources, minimize people/time in direct contact
· Improve reliability, reduce uncertainty – Design in reliability and serviceability. Reliable systems need less frequent maintenance and reduce the risk of collateral losses associated with unplanned downtime for maintenance or repair. Serviceable systems need less time to maintain or repair.
· Build trusting relationships – Data is the lifeblood of efforts to increase predictability and reliability, but it is also among our customers’ most valuable and closely guarded assets. Access to data is a major challenge, regardless of its potential benefits. Trusted partnerships, well-designed organizational policies, and secure communications and data storage infrastructure can encourage more open access.
· Integrate systems – Integrated vacuum and abatement systems offer significant benefits: Factory testing of fully assembled systems ensures fast installation and optimal performance out-of-the-box. Careful configuration and active thermal management optimize connections and prevent material deposition that can block pipes. Integrated systems have smaller footprints. Secondary enclosures improve safety. A single supplier clarifies responsibility and speeds troubleshooting and repair.
· Manage the supply chain - Plan for disruption and prepare for recovery.
Yes, we are all in this together.