News Article
Simplifying MEMS pressure sensor technology
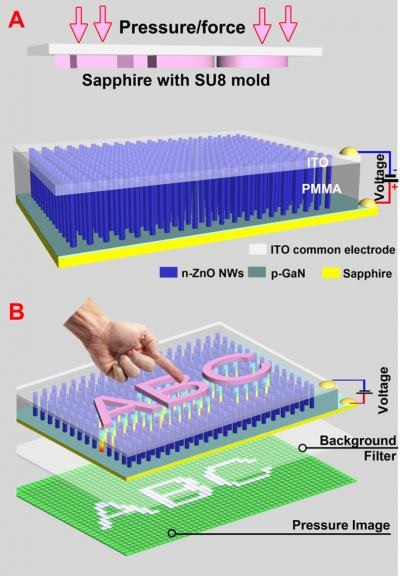
A new sensor incorporating gallium nitride and zinc oxide nanowires could provide an artificial sense of touch and be used in MEMS systems
Using thousands of nanometre-scale wires, researchers at the Georgia Institute of Technology have developed a sensor device that converts mechanical pressure - from a signature or a fingerprint - directly into light signals that can be captured and processed optically.The sensor device could provide an artificial sense of touch, offering sensitivity comparable to that of the human skin. Beyond collecting signatures and fingerprints, the technique could also be used in micro-electromechanical (MEMS) systems and biological imaging. And ultimately, it could provide a new approach for human-machine interfaces."You can write with your pen and the sensor will optically detect what you write at high resolution and with a very fast response rate," says Zhong Lin Wang, Regents' professor and Hightower Chair in the School of Materials Science and Engineering at Georgia Tech. "This is a new principle for imaging force that uses parallel detection and avoids many of the complications of existing pressure sensors."

Zhong Lin Wang holding the sensor device along with his research team in the backgroundIndividual zinc oxide (ZnO) nanowires that are part of the device operate as tiny LEDS when placed under strain from the mechanical pressure. They allow the device to provide detailed information about the amount of pressure being applied. Known as piezo-phototronics, the technology - first described by Wang in 2009 - provides a new way to capture information about pressure applied at very high resolution: up to 6,300 dots per inch.Piezoelectric materials generate a charge polarisation when they are placed under strain. The piezo-phototronic devices rely on that physical principle to tune and control the charge transport and recombination by the polarisation charges present at the ends of individual nanowires.
Grown on top of a gallium nitride (GaN) film, the nanowires create pixelled light emitters whose output varies with the pressure, creating an electroluminescent signal that can be integrated with on-chip photonics for data transmission, processing and recording."When you have a zinc oxide nanowire under strain, you create a piezoelectric charge at both ends which forms a piezoelectric potential," Wang explains. "The presence of the potential distorts the band structure in the wire, causing electrons to remain in the p-n junction longer and enhancing the efficiency of the LED." The efficiency increase in the LED is proportional to the strain created.Differences in the amount of strain applied translate to differences in light emitted from the root where the nanowires contact the GaN film. To fabricate the devices, a low-temperature chemical growth technique is used to create a patterned array of ZnO nanowires on a GaN thin film substrate with the c-axis pointing upward. The interfaces between the nanowires and the GaN film form the bottom surfaces of the nanowires. After infiltrating the space between nanowires with a PMMA thermoplastic, oxygen plasma is used to etch away the PMMA enough to expose the tops of the ZnO nanowires. A nickel-gold electrode is then used to form ohmic contact with the bottom gallium-nitride film, and a transparent indium-tin oxide (ITO) film is deposited on the top of the array to serve as a common electrode.When pressure is applied to the device through handwriting, nanowires are compressed along their axial directions, creating a negative piezo-potential, while uncompressed nanowires have no potential.
A schematic showing a device for imaging pressure distribution by the piezo-phototronic effect is shown at the top of this article. It shows a nanowire-LED based pressure sensor array before (a) and after (b) applying a compressive strain. A convex character pattern, such as "ABC," molded on a sapphire substrate, is used to apply the pressure pattern on the top of the indium-tin oxide (ITO) electrode.The researchers have pressed letters into the top of the device, which produces a corresponding light output from the bottom of the device. This output - which can all be read at the same time - can be processed and transmitted.The ability to see all of the emitters simultaneously allows the device to provide a quick response. "The response time is fast, and you can read a million pixels in a microsecond," says Wang.
When the light emission is created, it can be detected immediately with the optical fibre.
"The nanowires stop emitting light when the pressure is relieved. Switching from one mode to the other takes 90 milliseconds or less, Wang adds.
The researchers studied the stability and reproducibility of the sensor array by examining the light emitting intensity of the individual pixels under strain for 25 repetitive on-off cycles. They found that the output fluctuation was approximately 5 percent, much smaller than the overall level of the signal. The robustness of more than 20,000 pixels was studied.A spatial resolution of 2.7 µm was recorded from the device samples tested so far. Wang believes the resolution could be improved by reducing the diameter of the nanowires - allowing more nanowires to be grown - and by using a high-temperature fabrication process.
The researchers' study is described in detail in the paper, "High-resolution electroluminescent imaging of pressure distribution using a piezoelectric nanowire LED array," by Caofeng Pan et al in Nature Photonics (2013), published online on 11th August 2013. DOI:10.1038/nphoton.2013.191
This research was sponsored by the U.S. Department of Energy's Office of Basic Energy Sciences, the National Science Foundation, and the Knowledge Innovation Program of the Chinese Academy of Sciences.

Zhong Lin Wang holding the sensor device along with his research team in the backgroundIndividual zinc oxide (ZnO) nanowires that are part of the device operate as tiny LEDS when placed under strain from the mechanical pressure. They allow the device to provide detailed information about the amount of pressure being applied. Known as piezo-phototronics, the technology - first described by Wang in 2009 - provides a new way to capture information about pressure applied at very high resolution: up to 6,300 dots per inch.Piezoelectric materials generate a charge polarisation when they are placed under strain. The piezo-phototronic devices rely on that physical principle to tune and control the charge transport and recombination by the polarisation charges present at the ends of individual nanowires.
Grown on top of a gallium nitride (GaN) film, the nanowires create pixelled light emitters whose output varies with the pressure, creating an electroluminescent signal that can be integrated with on-chip photonics for data transmission, processing and recording."When you have a zinc oxide nanowire under strain, you create a piezoelectric charge at both ends which forms a piezoelectric potential," Wang explains. "The presence of the potential distorts the band structure in the wire, causing electrons to remain in the p-n junction longer and enhancing the efficiency of the LED." The efficiency increase in the LED is proportional to the strain created.Differences in the amount of strain applied translate to differences in light emitted from the root where the nanowires contact the GaN film. To fabricate the devices, a low-temperature chemical growth technique is used to create a patterned array of ZnO nanowires on a GaN thin film substrate with the c-axis pointing upward. The interfaces between the nanowires and the GaN film form the bottom surfaces of the nanowires. After infiltrating the space between nanowires with a PMMA thermoplastic, oxygen plasma is used to etch away the PMMA enough to expose the tops of the ZnO nanowires. A nickel-gold electrode is then used to form ohmic contact with the bottom gallium-nitride film, and a transparent indium-tin oxide (ITO) film is deposited on the top of the array to serve as a common electrode.When pressure is applied to the device through handwriting, nanowires are compressed along their axial directions, creating a negative piezo-potential, while uncompressed nanowires have no potential.
A schematic showing a device for imaging pressure distribution by the piezo-phototronic effect is shown at the top of this article. It shows a nanowire-LED based pressure sensor array before (a) and after (b) applying a compressive strain. A convex character pattern, such as "ABC," molded on a sapphire substrate, is used to apply the pressure pattern on the top of the indium-tin oxide (ITO) electrode.The researchers have pressed letters into the top of the device, which produces a corresponding light output from the bottom of the device. This output - which can all be read at the same time - can be processed and transmitted.The ability to see all of the emitters simultaneously allows the device to provide a quick response. "The response time is fast, and you can read a million pixels in a microsecond," says Wang.
When the light emission is created, it can be detected immediately with the optical fibre.
"The nanowires stop emitting light when the pressure is relieved. Switching from one mode to the other takes 90 milliseconds or less, Wang adds.
The researchers studied the stability and reproducibility of the sensor array by examining the light emitting intensity of the individual pixels under strain for 25 repetitive on-off cycles. They found that the output fluctuation was approximately 5 percent, much smaller than the overall level of the signal. The robustness of more than 20,000 pixels was studied.A spatial resolution of 2.7 µm was recorded from the device samples tested so far. Wang believes the resolution could be improved by reducing the diameter of the nanowires - allowing more nanowires to be grown - and by using a high-temperature fabrication process.
The researchers' study is described in detail in the paper, "High-resolution electroluminescent imaging of pressure distribution using a piezoelectric nanowire LED array," by Caofeng Pan et al in Nature Photonics (2013), published online on 11th August 2013. DOI:10.1038/nphoton.2013.191
This research was sponsored by the U.S. Department of Energy's Office of Basic Energy Sciences, the National Science Foundation, and the Knowledge Innovation Program of the Chinese Academy of Sciences.