MEI's MEMS tool set to lift off
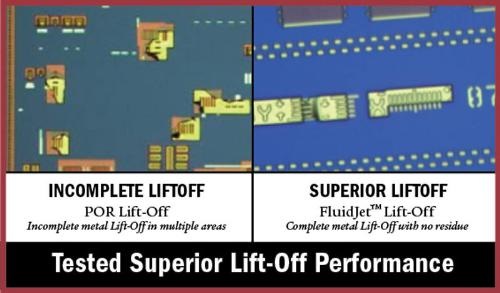
The FluidJet metal liftoff system is claimed to eliminate device damage, while using 80 percent less chemical than current single wafer processing solutions
MEI has revealed its FluidJet batch wet processing system for metal liftoff in MEMS manufacturing, delivering higher yielding, more cost effective metal liftoff processing.

MEI says its FluidJet batch wet processing system for metal liftoff achieves no metal re-deposition on either the front side or back side of the wafer, eliminates device damage, while using 80 percent less chemical than current single wafer processing solutions.
FluidJet also enables efficient, easily obtained gold and metal reclaim, reducing waste and downtime. FluidJet could also save manufacturing floor space by reducing the wet process footprint requirement by at least 60 percent over comparable throughput single wafer spray tools.
"By adopting the FluidJet metal liftoff system, semiconductor manufacturers will increase yield while reducing downtime and chemical costs and disposal," says Dan Cappello, President and CEO, MEI LLC. "FluidJet cleans the surface gently improving metal liftoff performance at a lower cost. Side by side "split lot" comparison data demonstrates superior performance on liftoff and resist strip layers while also reducing defects."
MEI says its FluidJet metal liftoff system is unlike conventional single wafer metal liftoff systems. Conventional metal liftoff solutions rely on high-pressure sprays that produce metal debris that can scratch or tear fine metal features. Metal debris can also redeposit, causing shorts.
The FluidJet batch immersion system's gentle removal and self cleaning tanks enable lifted metals to be more easily and completely reclaimed. Strainer baskets are emptied in minutes and sized to easily hold several thousand wafers worth of lifted metal.
MEI's FluidJet targets semiconductor and MEMS processing applications where Metal Liftoff is required to create GaAs BiFET device structures for mobile communications