Growing interest for thin film PZT in existing MEMS applications
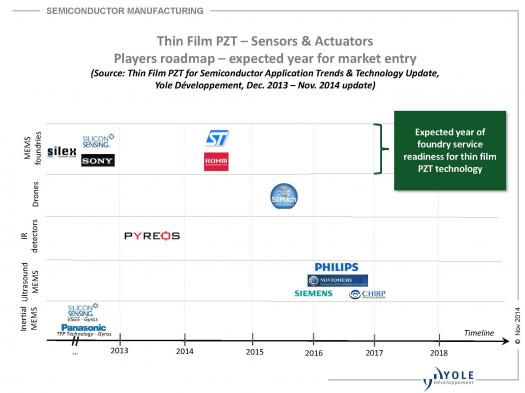
Last year, Yole Développement identified a growing market for thin film PZT, especially for MEMS applications that was assessed as worth $350M in 2013. Yole released a dedicated report, Thin Film PZT for Semiconductor Application Trends & Technology Update.
Since this release Yole has interviewed various suppliers of PZT Sol-Gel materials, Mitsubishi Materials Corp. (MMC) and its partner, SCREEN Semiconductor Solutions Co.,
Yole Développement also interviewed Silex Microsystems, a MEMS foundry, which is an end-user of MMC's solution. The aim of the interview was to get a better understanding of new materials and the equipment impact in the MEMS devices manufacturing process.
Silex Microsystems (Silex) has during late 2013 and 2014 with the support of MMC engineers successfully evaluated the PZT-N solution. "With the new N solution we obtained increased through-put using sub-layers in the 180-220 µm range instead of 50-80 nm as with our previously qualified PZT solution (3-4 X increase in deposition through-put)", explains Mr.Ebefors, Chief Technologist, Co-founder and VP R&D at Silex. "We also obtained improved dielectric properties (epsR), larger piezo effect (e31f) and similar excellent breakdown and defectivity properties as we achieve with our previous standard Sol-Gel PZT material", he adds. The company can repeatedly obtain breakdown voltages of Silex SG PZT films above 130 V/µm.
According to Silex, this point is very critical for many actuator applications such as µ-mirrors, inkjet heads and other active microfluidic fluidic devices. With proper optimization of the seedlayer process, Silex obtains high performance <100> oriented PZT films with a wide process window for the N-type PZT than with previously used materials. Previously there has been issues to obtain repeatable <100> PZT films with good performances (i.e. BD >80 V/µm) and hence <111> PZT films was often preferred. "With the optimized bottom electrode and seed layer process, we can now easily tune the PZT orientation to either <100> or <111> depending on our customers need. We can also obtain doped PZT films for further improved piezo properties", says Mr. Bauer, SVP Sales and Business Development, Silex. Latest developments from Silex, have resulted in I-V curves with drastically decreased leakage currents for its new PZT.
"Improved performance while at the same time offering much improved through-put is the first benefit identified by Silex engineers", says Mr.Ebefors. "The higher density allows fewer layers resulting in improved yield, lower material consumption and in the end lower cost", he adds.
Silex is carefully following the progress of various PZT technologies and new materials. Even though the strategic choice of Silex for the PZT back in 2011 was on the Sol-Gel solution, the company also carefully follows the development of other technologies like PVD and PLD. "We still believe the Sol-Gel technology has superior performance over these alternatives. And with this new PZT-N solution, the old disadvantage of low through-put for CSD technology has been solved", says Mr. Rimskog, Sales Director, North America and Japan, Silex.
Silex has also identified other Asian suppliers offering thick film PZT CSD solution. But the technical support is totally different than the one offered by the MMC's team. "To bring the new PZT-N solution to the market, a strong ecosystem of partners in various fields of piezo-MEMS has been established at Silex. Such approach does not only regard processing tool vendors and material suppliers; it also includes metrology experts such as aixACCT from Germany and various research institutes", details Mr. Ebefors.
MMC's solution combines chemicals and equipment. Aim of MMC's approach is to define all conditions of deposition and propose a combined and turnkey solution to its customers.As an end-user, Silex is currently fine tuning the process parameters for this PZT-N in its 6" line as a complement to the existing Sol-Gel technology in use since 2012. When high volume demands of PZT (>>50 µm/day) is required, the company will transfer the N-type PZT solution also to Silex 8" line. Silex recently got granted an EU project with the goal to demonstrate this capability.
"We still believe the Sol-Gel technology has superior performance over these alternatives. And with this new PZT-N solution, the old disadvantage of low through-put for CSD technology has been solved", says Silex.
According to Silex, first application to reach market using thin film PZT is most likely actuators like hard disc heads, ink-jet heads and other pumps and valves for microfluidics that require effective actuators. For some spatial light modulator (SLM) and micro-mirror application piezo-drive has advantages over traditional electrostatic comb drive actuators. Other optical MEMS devices would also gain from effective and fast long term stable piezo actuators.
In parallel, Silex is a partner in an R&D project developing PZT process technology for energy harvesting. This program may see commercial implementation some 3-4 years from now. Also for sensors, where the component designers use a combination of actuation/transmission and sensing/detection with same mechanical element and at the same time require low cross talk, Silex could offer good solutions: indeed, in addition to thin film PZT benefits, Silex has manufactured designs of multi axis motion sensors (gyroscope / accelerometer) and is currently optimizing process capability for ultrasound transducer elements (p-MUTs) operating at higher frequency than traditional bulk PZT solutions. These innovative MEMS devices are possible to make with the use of Silex proven PZT on silicon membrane technology.
Silex is already in the process qualifying new materials such as the new PZT-N solution that is on-going right now. "As a pure play foundry, we do not have our own roadmap as far as it comes to introduction in products to the end marker but the material is already under evaluation also by our customers", comments Mr Bauer.
Thin film PZT technology will be offered to Silex customers as a building block, to be incorporated into their designs. "Silex is a true Pure Play foundry, attracting primarily innovation leaders in the MEMS space that are looking for an "IP safe" manufacturing environment", explains Silex team.
"This also means, we explicitly refrain from offering application specific process platforms. Our approach at standardization takes place at a more granular level with our library of SmartBlock process modules that we combine together, facilitating the process of integrating a full manufacturing flow", they detail. PZT on C-SOI is already a fundamental SmartBlock applicable to a wide range of MEMS components. However this is often only part of the total process integration effort, and integration with other MEMS processes from Silex library is in most cases needed to enable the customers' actual design. Silex also has a proven track record as a leader when it comes to integration of, for example, TSV's and novel wafer level vacuum packaging technologies. "We are already used to integrating the PZT SmartBlock with such other SmartBlock technologies as well as with additional process blocks. For us, the PZT is a recent addition and goes along well with our other capabilities and our solid experience of fabricating innovative MEMS", comments Mr Bauer.
Silex sees a strong growing interest for thin film PZT in a multitude of existing MEMS applications. The company believes the MEMS market in general is also moving into a second wave of adoption and sees a larger crowd of engineers in various industries applying the potential of this rather new mechanical engineering discipline to create innovative solutions in the micro scale technology space that were not possible before. Silex has invested in a production solution for thin film PZT and is committed to being one of the leading MEMS foundry manufacturing providers for this technology. Thin film PZT clearly opens up a wide range of new opportunities to design novel micro scale structures and Silex true pure play business model is perfectly adapted to serve innovation leaders in this space looking to explore the multitude of new solutions made possible.
In its report, Yole Développement analyzed the strategy of the MEMS foundries and their positioning. According to the consulting company, every major MEMS foundry is today working on thin film PZT technology implementation and qualification, in their MEMS manufacturing processes.
The company adds: "TI, Silicon Sensing Systems and Silex seem to be the most advanced in this process as they have entered the process qualification stage"